Comprehensive Analysis of Rock Cutting Equipment
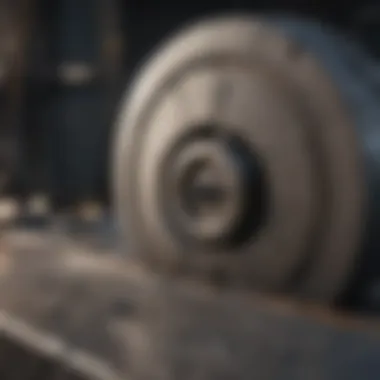
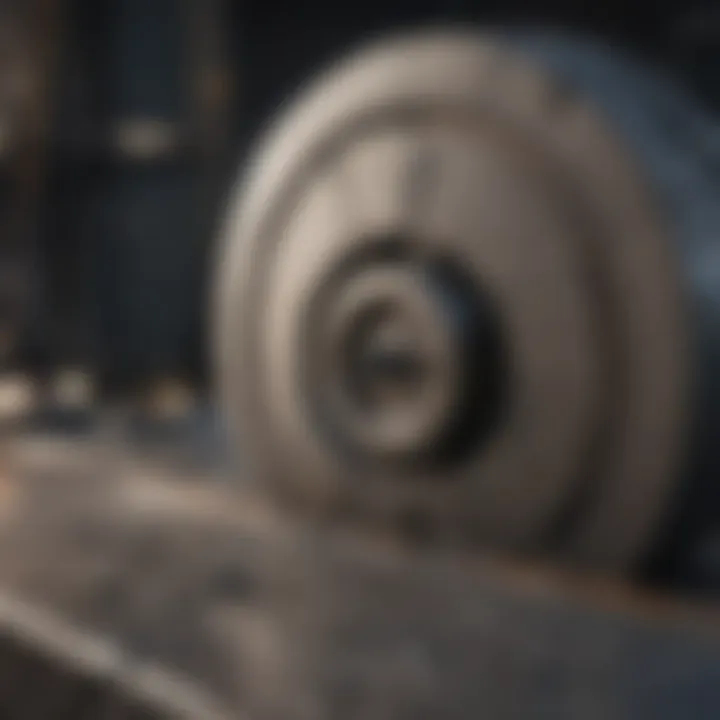
Intro
Rock cutting equipment plays a pivotal role in both geology and construction. It includes various tools designed for the effective fragmentation of solid materials, particularly rocks. This industry has evolved tremendously, reflecting advancements in technology and methodologies. The richness of this subject is evident in its historical context and modern applications. Many enthusiasts and professionals alike are keen to explore the intricacies surrounding this essential equipment, making it a worthwhile topic to analyze comprehensively.
History and Origins
Overview of Collectibles, Rocks, and Fossils
The history of rock cutting equipment dates back to ancient civilizations. Early humans used primitive tools for extracting minerals and creating beautiful stone artifacts. As societies progressed, so did the technology surrounding rock extraction. Eventually, the need for more efficient tools led to the development of advanced rock cutting equipment.
Collectors of rocks and fossils often seek these historical tools to understand their significance and evolution. Many tools are now seen as collectibles, treasured by those who appreciate the art of geology. These items provide insights into past techniques, methodologies, and cultures.
Historical Significance and Cultural Impact
Rock cutting tools have not only enabled the extraction of geological materials, but they have also shaped construction practices throughout history. From monumental buildings in ancient times to modern infrastructure, understanding the historical context of these tools highlights their cultural impact. In many cultures, specific tools became symbols of technological advancement and craftsmanship, embodying the skills of the people who used them.
According to a source on historical tools, "The evolution of rock cutting equipment mirrors the development of society's understanding of geology."
Identification and Classification
Guide to Identifying Rocks and Fossils
The identification of rocks and fossils is crucial for both collectors and scientists. Collectors often start by examining the physical characteristics of specimens, including texture, color, and hardness. Experts use various methods such as the Mohs scale of mineral hardness, acid tests, or even UV light to determine the composition of specific rocks and fossils.
Common Types and Variations
Different types of rock cutting equipment have emerged to cater to various geological tasks. Understanding various tools helps enthusiasts appreciate the complexities of rock cutting. Here are a few examples of common equipment:
- Diamond Wire Saws: Used for precise cutting of hard materials.
- Hydraulic Splitters: Effective for breaking large rocks without excessive vibration.
- DTH Hammers (Down The Hole): Ideal for drilling and blasting in construction and mining.
Each tool serves a specific purpose, making it essential for collectors to recognize the variety of equipment available.
In the analysis, we will further explore the technological advancements that shape the future of rock cutting tools and practices, vital for understanding the ongoing relevance in geological and construction industries.
Foreword to Rock Cutting Equipment
Rock cutting equipment plays a significant role in various industries, including construction, mining, and geology. Understanding its purpose and function is crucial for enthusiasts and professionals alike. This section outlines the key elements and benefits of rock cutting equipment, offering insights into its applications and importance.
First and foremost, rock cutting is essential for the extraction and shaping of materials. This process allows for the precise removal of rock, making it possible to access mineral deposits and create structures. The tools used are designed to handle different types of rock, including granite, marble, and sandstone. Each of these materials presents unique challenges, requiring specific tools and techniques to effectively cut through them.
The efficiency of rock cutting equipment can directly influence project timelines and costs. For instance, modern equipment like diamond saws and water jet cutters allows for faster operation compared to traditional methods. This not only saves time but also reduces labor costs, making projects more economically viable. The benefits extend beyond cost-saving; precise cuts minimize waste, further enhancing the efficiency of the process.
However, there are several considerations to keep in mind when selecting rock cutting equipment. Factors such as blade quality, cutting speed, and power supply can significantly impact performance. It is crucial to ensure that the equipment chosen aligns with the specific requirements of a project. Additionally, selecting reliable brands can lead to longer-lasting equipment, thereby reducing the frequency of replacements and maintenance.
In sum, the importance of rock cutting equipment cannot be overstated. It plays an integral role in the successful execution of various projects across multiple sectors. A thorough understanding of the equipment available, coupled with knowledge of operational factors, enhances both the efficiency and effectiveness of rock cutting processes. This article aims to provide a comprehensive analysis of these aspects, guiding readers through the complexities of rock cutting equipment.
Historical Background
The historical context of rock cutting equipment is essential to understand its development and significance in various industries. This background provides valuable insights into how these tools have evolved over time, influencing methods and practices in construction, mining, and geology. Historical knowledge highlights the necessity of innovation and adaptability in the equipment used for rock cutting. It also illustrates how ancient techniques laid the foundation for modern advancements, emphasizing the importance of learning from the past to improve future practices.
Early Methods of Rock Cutting
In ancient times, rock cutting primarily relied on simple and manual tools. Early humans utilized crude implements made from stones and bones to shape and carve rock for shelter or tools. The introduction of bronze and iron tools brought about more effective methods. For instance, the use of chisels made from these metals allowed for more precise cuts.
Around 3000 BCE, civilizations like the Egyptians employed techniques for quarrying, particularly for building their monumental structures. They used wooden wedges to split rock, pouring water into the cracks to expand them, which made cutting easier. This time, it involved significant manpower and artisanal skill.
Evolution of Technology
As centuries passed, the evolution of technology transformed rock cutting practices. The Middle Ages saw the introduction of advanced tools, including various forms of saws and drills. The Industrial Revolution in the 18th century marked a significant turning point. Steam power allowed for greater efficiency in quarrying stones and cutting rock, leading to the production of large structures without compromising quality.
In the 20th century, the introduction of diamond blades revolutionized the industry. These blades enabled faster and more efficient cutting of hard materials. The commercialization of water jet cutting machines further advanced rock cutting technology, allowing for precision jobs without damaging surrounding materials.
The last few decades have seen a surge in automation and digital solutions in rock cutting equipment. Computer Numerical Control (CNC) machines have integrated software that enables extremely precise cuts based on computer designs. As technology continues to advance, the methods and tools available for cutting rock are becoming increasingly sophisticated, allowing for efficiency and accuracy that were previously unimaginable.
"The evolution of rock cutting equipment reflects a history of ingenuity, showcasing the relentless pursuit of improvement in efficiency and precision."
Understanding this historical trajectory enables rock and fossil collectors to appreciate the techniques and technology behind their tools and urges manufacturers to innovate while respecting traditional methods.
Types of Rock Cutting Equipment
In the evolving field of geology, construction, and mining, understanding the different Types of Rock Cutting Equipment is crucial. Each type of equipment serves distinct purposes and offers unique benefits depending on the specific needs of the task at hand. The proper selection of equipment can significantly improve efficiency, quality of work, and safety in operations. This section explores the four predominant types of rock cutting equipment, analyzing their characteristics and applications in various sectors.
Diamond Saws
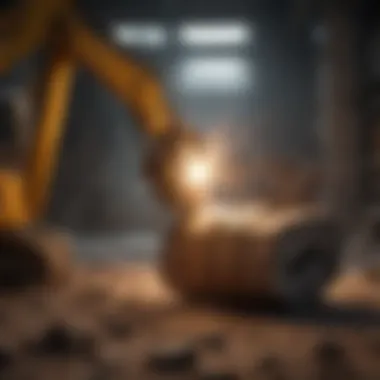
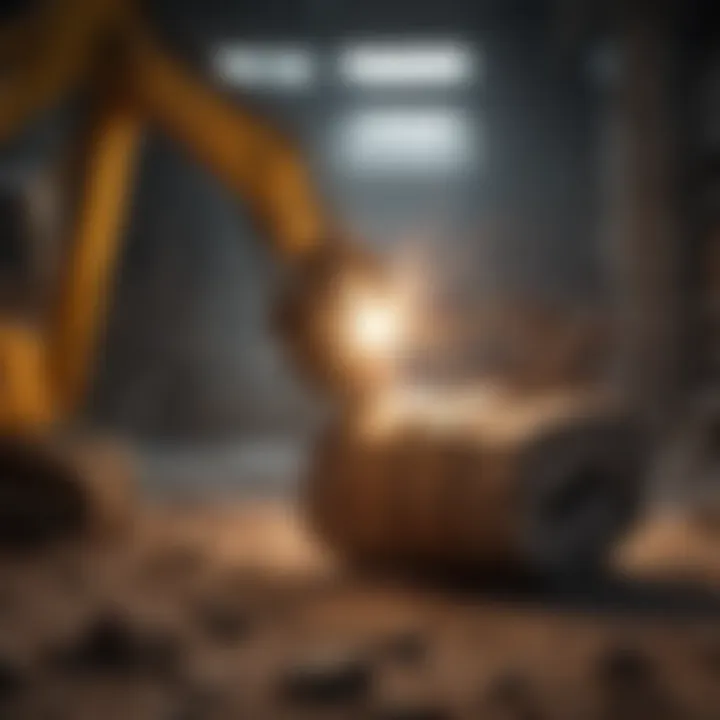
Diamond saws are one of the most widely used tools for cutting hard rock and materials. Their effectiveness stems from the use of diamond blades, which provide an unparalleled cutting ability. The main advantage of diamond saws is their precision; they can create clean, straight cuts, reducing the likeliness of material damage. Additionally, these saws can operate at higher speeds, thus increasing productivity in industries like construction and stone quarrying.
Key Benefits:
- Exceptional accuracy in cuts
- Versatile for different materials
- Increased cutting speed compared to traditional saws
Diamond saws also require proper maintenance and technique for optimal performance. When used correctly, they minimize wear, extend the life of the equipment, and help in achieving desired results in rock fragmentation.
Wire Saws
Wire saws utilize a continuous loop of wire, usually embedded with diamonds, to achieve cutting. This type of equipment is particularly beneficial for quarrying large blocks of stone. The thinness of the wire minimizes waste, allowing for more efficient material extraction. Wire saws excel in producing smooth surfaces, which is often necessary in the artistic stone cutting industry.
Considerations for Wire Saws:
- Minimal waste generation
- High flexibility for intricate cuts
- Lower operational costs in the long run
Their ability to maneuver around tight curves and create detailed shapes makes wire saws pivotal in stone masonry projects. However, they need to be operated with a skilled hand to maximize their potential in complex cutting tasks.
Water Jet Cutting Machines
Water jet cutting machines employ high-pressure water jets, often mixed with abrasives, to sever rock and other materials. This technique is known for its ability to handle a diverse range of materials effectively. One of the standout features of water jet machines is the lack of heat generation during cutting, which prevents thermal distortion of the material.
Benefits of Water Jet Cutting:
- No heat affect on material
- Capable of cutting intricate designs
- Environmentally friendly due to minimized waste
Moreover, water jet cutting can be used on varying thicknesses, making it a versatile tool in both industrial and artistic applications. Operators should consider factors like water temperature and pressure settings for optimizing the cutting process.
CNC Machines
CNC (Computer Numerical Control) machines represent an advanced method of rock cutting. These machines are programmed to perform precise cuts based on digital designs. The use of CNC technology enhances the cutting process by ensuring repeatability, which is vital for production environments. It simplifies complex operations and allows for intricate designs that would be challenging to achieve manually.
Advantages of CNC Machines:
- High precision and repeatability
- Capability to execute complex designs
- Reduced manual labor increases safety
However, the initial investment and training associated with CNC technology can be substantial. The resulting efficiency and quality can outweigh these costs in the long term, especially for businesses focused on large-scale projects.
"Investing in advanced rock cutting equipment can significantly enhance competitive advantage in today’s demanding industrial landscape."
Understanding these various types of rock cutting equipment allows professionals in the industry to choose the appropriate tools for their specific needs, ultimately leading to improved operational success.
Applications in Different Sectors
The application of rock cutting equipment spans various industries, highlighting its necessity and versatility. This section examines how specific sectors leverage these tools, thereby driving advancements and efficiencies. By exploring the construction, mining, and fossil excavation industries, we can understand the multifaceted impacts of rock cutting technology.
Construction Industry
In the construction industry, rock cutting equipment plays a crucial role in project execution. It facilitates the creation of foundations, tunnels, and other structures. The accuracy and efficiency provided by advanced cutting tools enable contractors to achieve precise shapes and sizes, minimizing the need for additional adjustments. This results in significant time savings and cost reductions.
Key benefits include:
- Enhanced Precision: Cutting tools like diamond saws ensure that materials are shaped accurately.
- Improved Safety: Reduced manual labor decreases the risk of injuries on job sites.
- Versatile Applications: Rock cutting is essential for both large-scale projects, such as highways, and smaller developments like residential buildings.
The construction sector continues to evolve, with integrating automation and innovative material usage. This evolution demands an understanding of how to operate and maintain rock cutting tools effectively. Regular training on safety standards and operational protocols is imperative.
Mining Industry
In mining, rock cutting equipment is indispensable for extracting valuable resources. This sector relies on various cutting technologies to navigate rock formations efficiently. The tools used not only influence production rates but also affect the overall profitability of mining operations.
Noteworthy considerations include:
- Resource Recovery: Advanced cutting methods improve the yield from mining sites.
- Operational Efficiency: Enhanced technology allows for faster and more effective drilling and cutting.
- Safety Standards: Robust machinery reduces risks associated with rock falls and landslides.
Furthermore, automation in mining technology has introduced precision drilling processes, thus safeguarding human operators while maximizing output. The shift towards sustainability in the mining sector also means that companies need to adopt equipment that minimizes environmental impact.
Fossil Excavation
Fossil excavation highlights the significance of rock cutting tools in paleontology. Researchers rely on sophisticated equipment to extract fossils without damaging the delicate structures beneath. The precision offered by tools is vital for preserving the integrity of finds, which are often thousands of years old.
Important elements in this area include:
- Preservation of Finds: Gentle cutting techniques protect fragile fossils from breakage.
- Accessibility: Advanced equipment can reach and excavate harder rock layers, unveiling buried specimens.
- Research and Education Opportunities: The excavation process informs scientific understanding and educates the public, revealing insights into Earth’s history.
Each of these sectors underlines the diverse applications of rock cutting equipment. The influence of cutting technologies extends beyond mere functionality; they serve as key drivers of progress, ensuring that operations are reliable, efficient, and safe. As innovations continue to emerge, the relevance and importance of rock cutting equipment in various sectors will only increase, shaping industries for the future.
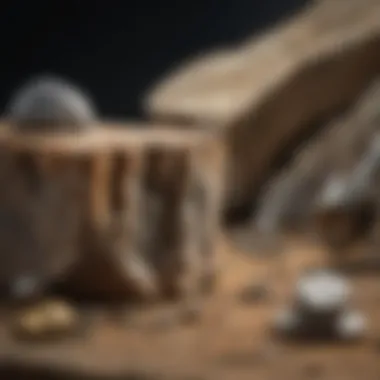
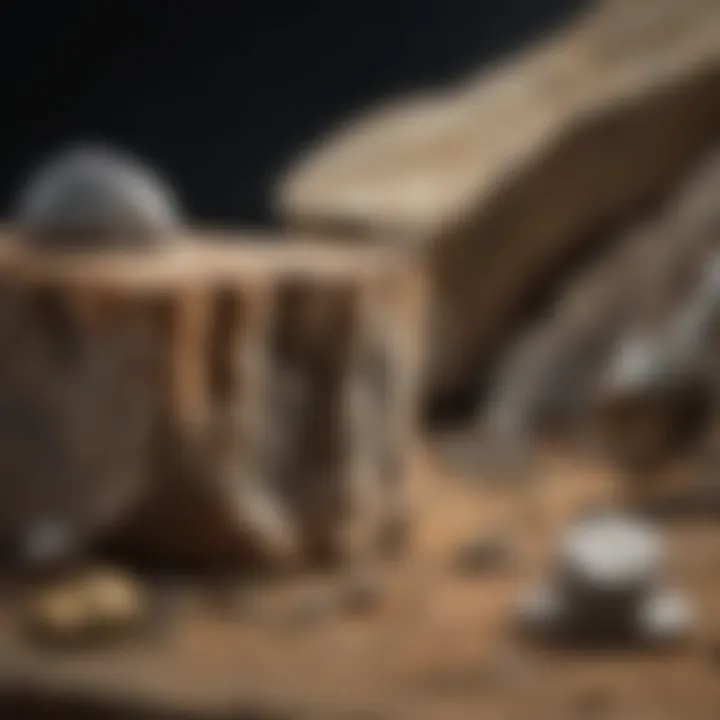
Technological Advancements
Technological advancements play a crucial role in the evolution of rock cutting equipment. They significantly enhance both efficiency and precision in various applications, which is essential for both industrial sectors and hobbyist collectors. As technology progresses, equipment becomes more sophisticated, enabling operators to achieve intricate cuts with minimal effort.
One of the main benefits of advancements in technology is the integration of smart features. Many modern machines come with automation, which streamlines operations. Automation reduces the need for human intervention, thereby decreasing the chances of errors and improving overall safety on site. Operators can realize higher productivity levels as a result of these innovations.
Another important aspect is the introduction of improved materials used in the construction of cutting devices. Innovations in manufacturing techniques lead to the production of stronger and more durable blades and accessories. This not only prolongs the lifespan of the equipment but also enhances cutting performance across various materials, including granite and quartz.
From an economic standpoint, these advancements result in cost-effectiveness. Although the initial investment in cutting-edge equipment might be higher, the long-term savings associated with reduced maintenance and rapid cutting capabilities can significantly offset these costs.
"Investing in cutting-edge technology not only provides immediate advantages but also positions companies for future growth and adaptability."
Automation in Rock Cutting
Automation in rock cutting refers to the use of technology and machinery to perform cutting tasks with minimal human input. This advancement has revolutionized the industry by introducing various automated systems and software that enhance cutting precision. The intelligent operation of machines, such as CNC machines, allows for repeatable and accurate cuts, reducing both time and material waste.
Key benefits of automation include:
- Increased Efficiency: Automated systems can run continuously without fatigue, which results in higher production rates.
- Enhanced Accuracy: High-precision automated machines ensure that each cut is uniform, improving the quality of the final product.
- Safety Improvements: Reducing human involvement minimizes the risks associated with manual cutting methods, protecting operators from potential injuries.
Overall, the move towards automation in rock cutting aligns with current trends towards digitalization and Industry 4.0, making it a strategic focus for companies wishing to stay competitive.
Improved Materials Used
The advent of new materials in the construction of diamond blades and cutting tools has propelled performance in rock cutting. Enhanced durability, higher thermal resistance, and improved cutting characteristics are just a few of the benefits associated with these materials. Modern blades are often constructed from high-grade diamonds arranged in a matrix that provides superior cutting ability even under extreme conditions.
Some notable advancements include:
- Enhanced Diamond Composition: New diamond synthesis technologies allow for finer and more uniform diamonds, contributing to sharper cutting edges.
- Advanced Bonding Techniques: Improved bonding materials ensure that diamonds remain fixed to the blades even after prolonged use, thus prolonging their life.
- Lightweight Materials: The use of lighter materials in machinery design enhances maneuverability and reduces operator fatigue, making cutting tasks easier.
The integration of these improved materials signifies a tremendous leap not only in performance but in the longevity of the cutting tools used across various industries, catering to both commercial needs and the demands of fossil collectors.
Factors Influencing Operation Efficiency
Operation efficiency in rock cutting equipment is critical. It determines the productivity and cost-effectiveness of engineering, mining, and construction projects. Understanding this concept involves looking at several key factors that impact how effectively these machines function. Attention to these specifics can lead to improved performance, reduced operational costs, and longer equipment lifespan.
Blade Quality
Blade quality plays a crucial role in the efficiency of rock cutting tools. High-quality blades can cut through materials more effectively and with less friction. This not only improves cutting speed but also minimizes wear and tear on the machine itself. Poor quality blades tend to dull quickly, resulting in increased downtime and higher costs for replacements. Furthermore, superior blades are often made from materials that withstand heat and wear better than standard options. For professionals in rock and fossil collection, investing in the right blade quality means more precise and cleaner cuts, preserving the integrity of specimens.
Cutting Speed
Cutting speed is another important factor influencing operational efficiency. This refers to how quickly the cutting tool can pierce through rock. Higher cutting speeds can lead to reduced time spent on projects. However, it is crucial to find a balance. Excessive cutting speeds can cause undue stress on the equipment and may lead to overheating or damage. Factors such as the type of rock being cut and the specific machinery being used dictate optimal cutting speeds. Proper calibration ensures that cutting speed maximizes productivity without compromising safety or equipment longevity. For collectors, faster cutting means better access to more specimens within shorter time frames.
Power Supply Considerations
Reliable power supply is fundamental to effective rock cutting operations. Equipment needs sufficient and consistent power to function correctly. Fluctuations in power can lead to inefficiency and reduced performance quality. Using generators or backup power sources may be necessary in remote areas where electrical supply is unstable. Additionally, energy-efficient machines are becoming increasingly relevant. These models can maintain high operational speeds while consuming less energy, aligning with industry trends toward sustainability. Professionals should prioritize selecting equipment that not only meets power requirements but does so efficiently to optimize operational output.
"Investing in high-quality equipment and understanding these factors leads to not just operational efficiency but enhanced effectiveness in achieving project goals."
Maintenance Practices
In the realm of rock cutting equipment, maintenance practices are not merely routine tasks; they are crucial for extending the lifespan and performance efficiency of these machines. Given the harsh conditions under which these tools operate, applying systematic maintenance measures can mitigate breakdowns, enhance precision in cutting, and ultimately, result in cost savings. Effective maintenance contributes directly to operational safety, performance reliability, and compliance with industry standards.
Regular Inspections
Regular inspections serve as the backbone of a solid maintenance program. These inspections should be conducted frequently to ascertain the operational status of equipment. Focus areas during these inspections include checking for wear and tear on blades, verifying the integrity of hydraulic systems, and assessing electrical components for any signs of malfunction.
These inspections enable operators to identify potential issues before they escalate into serious problems. Maintaining a detailed log of inspection results can also help in tracking performance over time. Following a set inspection schedule can reduce unexpected downtime and improve overall productivity. Each inspection contributes to a comprehensive understanding of equipment health, allowing for informed decisions on repairs or replacements.
Proper Lubrication Techniques
Proper lubrication plays a pivotal role in maintaining rock cutting equipment. Without adequate lubrication, friction increases, leading to excessive heat and rapid wear on components. Identifying the right type of lubricant based on manufacturer guidelines is essential. Each type of machine may have its specific requirements regarding the frequency and amount of lubrication needed.
Operators should not overlook the importance of cleaning components before applying new lubricant. This process prevents contaminants from causing further damage. Implementing a systematic lubrication schedule, including seasonal considerations, helps ensure that all parts function smoothly. Implementing an unforeseen breakdown increases equipment longevity significantly, making it a sound investment.
Replacement of Worn Parts
Despite the best maintenance practices, some parts will inevitably wear out. Timely replacement of these worn parts is essential to avoid diminishing performance and safety hazards. Operators should be keen on indicators that signal a need for a replacement, such as unusual sounds, decreased cutting efficiency, or visible damage.
Establishing a planned replacement schedule for components known to wear quickly—like blades and belts—can help maintain operational efficiency. Keeping spare parts and components readily available can ensure that operations are not interrupted. Additionally, utilizing high-quality parts for replacements guarantees they meet safety and operational standards.
Key Consideration: Consistent attention to maintenance practices can prevent minor issues from evolving into major failures that disrupt work flow or increase operational costs.
In summary, adopting robust maintenance practices is not optional but essential for any entity involved in rock cutting. Inspections, lubrication, and timely part replacements are foundational to achieving optimal equipment performance. Engaging in these practices not only enhances productivity but also underscores a commitment to safety and operational excellence.
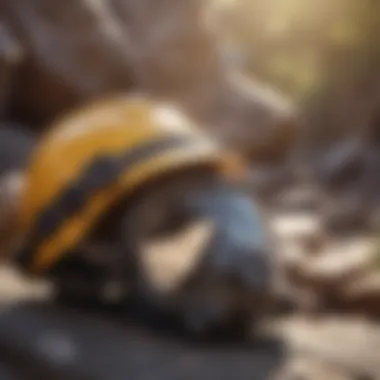
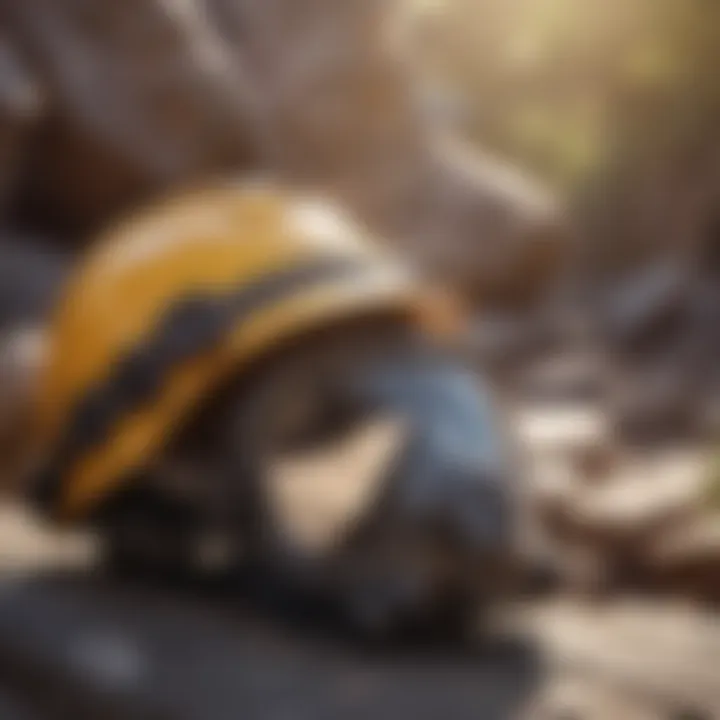
Safety Standards and Guidelines
Safety is paramount when operating rock cutting equipment. The dangers associated with handling heavy machinery, cutting tools, and materials can pose significant risks to operators and bystanders alike. This section outlines essential safety standards and guidelines that aim to minimize hazards and ensure a secure working environment.
Personal Protective Equipment
The use of personal protective equipment (PPE) is a critical component of safety in rock cutting operations. PPE includes various items designed to protect the user from potential injuries. Commonly recommended protective gear includes:
- Safety Helmets: Protect the head from falling objects or debris.
- Safety Goggles: Shield the eyes from flying particles and dust generated during cutting.
- Ear Protection: Reduce noise exposure from cutting machinery, preventing hearing loss.
- Respiratory Masks: Essential in environments where dust and harmful particles are present.
- Steel-Toed Boots: Provide protection for the feet from heavy objects and accidental impacts.
Using the appropriate PPE not only adheres to safety regulations but also sets a standard of care within the workplace. Regular training on the importance of PPE and proper usage techniques can foster a safety-conscious culture among operators.
Operational Protocols
Establishing clear operational protocols is vital for promoting safety in rock cutting processes. These protocols outline step-by-step instructions and best practices to ensure safe and efficient operations. Important elements to consider include:
- Pre-Operational Checks: Inspect equipment for any defects or malfunctions before starting work. Look for proper functioning of safety features and the integrity of cutting tools.
- Training Sessions: Regular training for operators on proper handling techniques, emergency procedures, and equipment operations. This training should be updated frequently to incorporate new technologies or safety findings.
- Communication Signals: Employ visual and auditory signals to maintain communication among team members, especially in noisy environments.
- Emergency Response Plans: Have clear plans in place for emergencies, outlining procedures for accidents or injuries.
"Adhering to operational protocols not only protects individuals but also enhances the overall productivity of rock cutting operations."
By implementing comprehensive safety standards and guidelines, stakeholders ensure that rock cutting operations proceed with minimal risk, fostering a safer work environment for all involved. The commitment to safety ultimately contributes to a more effective and responsible industry, where the welfare of workers is prioritized.
Environmental Considerations
In recent years, the importance of environmental considerations in rock cutting equipment has gained attention. The mining and construction sectors are often scrutinized for their ecological impact. Mitigating this impact is essential for sustainable practices and compliance with regulations. This section outlines key aspects of environmental considerations, focussing on the significance of waste management and energy efficiency.
Waste Management Practices
Effective waste management practices are crucial in the field of rock cutting. The waste generated can include dust, debris, and discarded materials. Implementing measures to reduce waste not only meets legal requirements but also fosters a more sustainable approach. Here are several strategies:
- Recycling Materials: Reusing rock fragments can decrease the environmental footprint. Industries can process waste into aggregates for construction projects.
- Dust Control Techniques: Using water sprays or dust suppressants during cutting operations can minimize airborne particles, improving air quality in surrounding areas.
- Proper Disposal: Following protocols for disposing of hazardous materials prevents contamination of soil and water sources. Logistics to ensure proper disposal can help mitigate long-term environmental damage.
Overall, by prioritizing waste management, companies can enhance their sustainability efforts and demonstrate responsible operations.
Energy Consumption and Efficiency
Energy consumption in rock cutting operations is another significant environmental concern. High energy use can lead to increased greenhouse gas emissions, thus affecting climate change. Therefore, enhancing energy efficiency is vital. Some aspects to consider include:
- Modern Equipment Utilization: Advanced machinery often uses energy more efficiently than older models. Investing in newer technologies can yield better performance while using less energy.
- Optimizing Cutting Techniques: Utilizing optimal cutting speeds and techniques can reduce energy consumption. Staff training on best practices often leads to significant energy savings.
- Alternative Energy Sources: Exploring renewable energy options, such as solar or wind, can decrease reliance on fossil fuels, further minimizing environmental impact.
It is essential for the industry to recognize and act upon its environmental responsibilities. Shifting towards sustainability can improve both public perception and regulatory compliance.
By focusing on these two critical aspects of environmental considerations, the rock cutting industry can not only fulfill its ethical obligations but also operate more efficiently. Achieving a balance between productivity and environmental stewardship is increasingly viewed as a standard practice, necessary for the future of the industry.
Future Trends in Rock Cutting Technology
The evolution of rock cutting technology is pivotal, not just for enhancing operational efficiency but also for addressing larger environmental and economic challenges. This section discusses significant upcoming trends that are reshaping how industries approach rock cutting. Advances such as artificial intelligence integration and eco-friendly innovations are not only improving efficiency but also establishing a new standard for sustainability in the sector.
Integration of AI
Artificial Intelligence (AI) is becoming a crucial component in the field of rock cutting equipment. The integration of AI-driven technologies enhances both precision and efficacy in operations. Machine learning algorithms enable better predictive maintenance, minimizing downtime and operational costs. For instance, AI systems can analyze data from cutting processes to identify patterns. This analysis can predict when a part might fail, allowing for timely replacement before issues arise.
Moreover, AI enables advanced automation in rock cutting machines. Robots can be programmed for specific tasks, leading to consistency in output while reducing human error. These machines can adapt to varying rock hardness and structure. As a result, they maintain optimal cutting speeds, which boosts productivity.
In addition, AI systems contribute to safety by monitoring real-time data for hazardous conditions. This proactive measure can significantly reduce accidents in high-risk environments. Through this holistic integration of AI, the future of rock cutting presents a promise of improved efficiency and safety standards.
Sustainability Innovations
Sustainability is a rising priority within the rock cutting industry. As concerns about environmental impacts grow, innovations focused on minimizing ecological footprints are appearing. New technologies are being developed to reduce energy consumption during the cutting process. For example, energy-efficient machines can consume less power while maintaining performance efficiency. By adopting such technologies, companies can not only cut costs but also reduce greenhouse gas emissions.
One noteworthy development is the use of water recycling systems in water jet cutting machines. These systems allow for the recirculation of water used in cutting processes, significantly reducing water waste. This addresses concerns related to water scarcity in many regions where mining or construction activities take place.
Promoting the usage of biodegradable lubricants is another innovation gaining traction. These alternatives pose less environmental risk compared to conventional lubricants, aligning with heightened regulatory standards.
Additionally, the push for sustainable sourcing of materials used in rock cutting equipment is gaining momentum. Manufacturers are now seeking out recycled or sustainably sourced raw materials, contributing to a circular economy.
The combined adoption of these sustainability innovations positions the rock cutting industry toward a more responsible future while meeting the demands of environmentally conscious consumers.
The integration of AI and sustainable practices marks a significant shift, leading the rock cutting industry toward enhanced professionalism and accountability.
The End
The conclusion section plays a pivotal role in summarizing the critical insights presented throughout this article. It encapsulates the essence of rock cutting equipment, which is essential for various industries, like construction and mining. Understanding the complexities surrounding these tools is more than just academic; it informs practical applications that impact safety, efficiency, and innovation.
In this article, several aspects were highlighted. We explored the historical background and technological advancements of rock cutting equipment. The implications of technological improvements, particularly automation and AI integration, are reshaping how industries operate. Collectors and enthusiasts alike must consider these trends as they see how tools will adapt in response to the changing demands of society.
Furthermore, discussions on maintenance practices and safety protocols underscore the importance of keeping equipment in optimal condition. Regular inspections, proper lubrication techniques, and timely replacement of worn parts contribute not just to operational efficiency but also to worker safety. Adhering to safety standards is paramount, as it protects the well-being of professionals who rely on these machines daily.
Moreover, environmental considerations are becoming more important, demanding improved waste management practices and efficient energy consumption strategies. As the industry evolves, adopting sustainable practices will be crucial. The future of rock cutting equipment is contingent upon the balance between technological growth and environmental responsibility.
In summary, this conclusion serves to remind us that rock cutting equipment is more than just tools; they represent the convergence of history, technology, and contemporary challenges. Engaging with this knowledge equips rock and fossil collectors, as well as industry professionals, with insights essential for navigating future developments. Investing time in understanding the nuances of these tools ensures preparedness for the advancements yet to come, making this topic invaluable in the broader scope of geology and construction.