Rock Slicing Machines: Techniques and Innovations
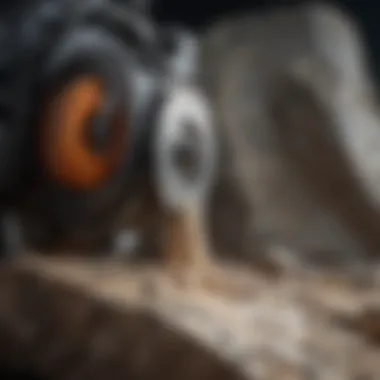
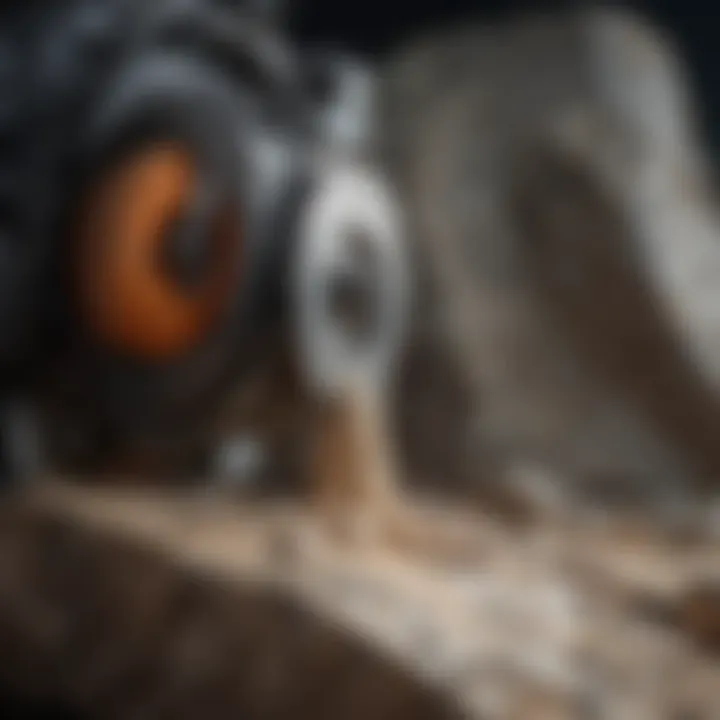
Intro
Rock slicing machines have fundamentally reshaped the landscapes of geology, paleontology, and fossil collection. These sophisticated tools enable researchers and enthusiasts alike to meticulously prepare and study specimens, thus unlocking a wealth of information held within the Earth’s history. As technology advances, the techniques and applications of rock slicing machines continue to evolve. This guide delves into their intricate workings, historical roots, and the myriad ways they have impacted the fields of geology and paleontology. It aims to bridge the gap between solid scientific understanding and collection practices, all while appreciating the innovations shaping the future of rock preparation.
History and Origins
Overview of Collectibles, Rocks, and Fossils
The fascination with rocks and fossils dates back to ancient civilizations. Rocks were not only used as tools but also held significant aesthetic value. Early humans recognized the unique characteristics of various stones and fossils, often using them for decorative or ritualistic purposes. This deep-rooted appreciation laid the groundwork for modern geology and paleontology. Collectors began seeking unique specimens, which in turn fueled advancements in the techniques used for excavation and preservation.
Historical Significance and Cultural Impact
Throughout history, rock slicing machines have evolved from rudimentary tools to advanced technologies. In the 19th century, the advent of more sophisticated slicing techniques revolutionized the study of thin sections. Scientists could examine minerals under microscopes, leading to significant discoveries about Earth’s composition. Cultural practices have also changed; where once stones were merely collected, they are now analyzed for their past and present utility. This has reshaped not only scientific inquiry but also contributed to education and hobbyist activities worldwide.
Identification and Classification
Guide to Identifying Rocks and Fossils
Understanding how to identify rocks and fossils is crucial for collectors and scientists. Key identification factors include:
- Color: The hue of a rock can hint at its mineral content.
- Texture: This refers to the feel and appearance of the rock surface, indicating the process of formation.
- Hardness: Measuring how easily a mineral can be scratched helps determine its identity through the Mohs scale.
Proper identification equips collectors with the knowledge to appreciate the geological history encapsulated within their specimens.
Common Types and Variations
Rocks can be classified into three main types:
- Igneous: Formed from the cooling of molten material.
- Sedimentary: Created through the compaction of layers of material, often containing fossils.
- Metamorphic: Resulting from the alteration of existing rock through heat and pressure.
Each type hosts various specimens, each possessing distinct characteristics relevant to collectors and researchers. Understanding these types enhances appreciation for the diversity of Earth’s materials and their geological narratives.
"The study of rocks and fossils is not just an exploration of time; it is a journey into the core of our planet's evolution."
Prelude to Rock Slicing Machines
The introduction of rock slicing machines marks a significant advancement in geology and paleontology. These machines serve not only as tools but as essential instruments for precise specimen preparation and analysis. Their ability to create thin slices of rocks or fossils facilitates detailed examinations that are crucial for scientific research and education. From understanding geological layers to examining microstructures in fossils, rock slicing machines provide clarity that would be almost impossible to achieve with manual methods.
The benefits of using rock slicing machines include improved efficiency and enhanced accuracy. Traditional slicing methods are often time-consuming and can lead to inconsistent results. With machines designed for this specific purpose, operators can achieve uniform slices with reproducible thickness. This is essential for comparative studies, where the integrity of the specimen must be preserved while allowing for thorough investigation.
Moreover, the precision of modern rock slicing machines has opened new avenues for research. As studies in geology and paleontology become more detailed, the need for advanced tools becomes apparent. Collectors and researchers alike can leverage the capabilities of these machines to prepare samples that meet high standards required in academic and professional settings.
In sum, the importance of rock slicing machines lies in their ability to cater to both practical needs and scientific inquiry. They enable a deeper understanding of geological materials and fossils, transforming the way researchers approach their studies. The reliance on slicing machines is growing, reflecting the increasing complexity of the tasks that geologists and paleontologists undertake every day.
The Importance of Rock Slicing in Geology
Rock slicing plays a critical role in geology, enabling scientists to study the internal structures of rocks. Understanding these structures enhances our knowledge of the Earth's history, formation processes, and material composition.
The following points highlight the significance of rock slicing in this field:
- Detailed Analysis: Thin slices allow experts to observe crystallography and mineralogy, which are essential for understanding rock origins and transformations.
- Sample Integrity: Machines create slices without causing damage, preserving essential geological features that could be lost with traditional methods.
- Research Advancements: Enhanced precision multiplies the volume of information and analysis possible from each sample, leading to more significant advancements in geological research.
"Slicing machines are not just tools; they are gateways to unlocking secrets held within the Earth."
Overall, the integration of rock slicing machines into geological studies is not merely a matter of convenience. It represents a paradigm shift in how research is conducted. The implications of using these machines extend far beyond practical applications; they redefine the boundaries of what can be achieved in the quest to understand our planet.
Types of Rock Slicing Machines
Understanding the different types of rock slicing machines is essential for maximizing efficiency and producing quality slices. Each type of machine offers distinct advantages that can greatly impact the outcome of rock preparation. The right choice depends on various factors, including the specific characteristics of the rock being cut, the desired thickness, and the level of precision required. This section will delve into three primary types of rock slicing machines: diamond wire saws, flat saws, and band saws.
Diamond Wire Saws
Diamond wire saws represent a significant advancement in rock slicing technology. They utilize a thin wire embedded with diamond segments to perform precise cuts through hard rocks. This method minimizes waste and reduces the amount of heat generated during the slicing process. Hence, diamond wire saws are particularly suitable for difficult materials such as granite and marble.
Benefits of Diamond Wire Saws:
- Precision cutting: Provides extremely accurate slices with minimal effort.
- Versatility: Can cut various types of rocks with different hardness levels.
- Reduced material loss: Efficient cutting reduces the amount of rock waste.
When choosing a diamond wire saw, consider factors such as wire diameter, cutting speed, and the machine's power supply. Knowledge of these aspects can optimize performance and results in rock slicing projects.
Flat Saws
Flat saws are another type commonly used in rock slicing. These machines employ a flat blade that rotates at high speeds to create slices. They are ideal for producing uniform thickness slices across a range of rock types. The design of flat saws allows for easy adjustments to the depth and thickness of the slice, making them highly adaptable for various cutting tasks.
Key Considerations for Flat Saws:
- Cutting speed can be adjusted for different materials.
- Versatility allows use for a wide range of rocks and sizes.
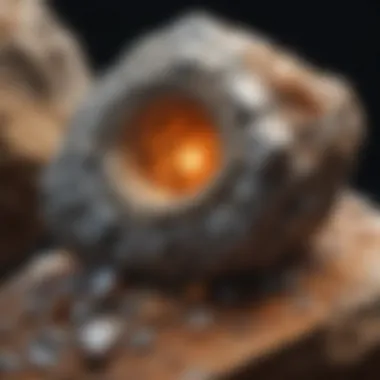
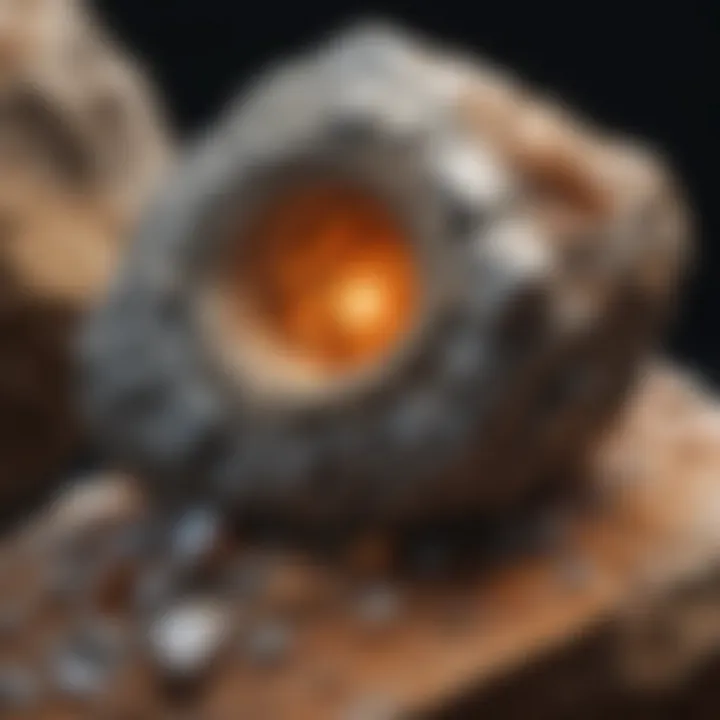
Flat saws are often more budget-friendly compared to other machines, making them an attractive option for hobbyists and researchers needing optimal performance without extensive investment.
Band Saws
Band saws feature a long, continuous blade that moves in a loop around wheels, allowing for dynamic cutting movements. This design enables band saws to create curvilinear cuts as well as straight slices, offering unique capabilities in rock preparation. They are particularly advantageous for larger blocks of rock where intricate shapes are required.
Advantages of Band Saws:
- Ability to cut intricate shapes along with straight slices.
- Suitable for larger pieces of rock, allowing flexibility in projects.
For operators, understanding the specifications and limitations of band saws is crucial to ensure suitable operations, especially when dealing with larger or more complex samples.
In requiring tailored solutions for rock slicing, selecting the correct type of machine proves fundamental in achieving the desired output and preserving rock integrity.
Technical Specifications of Rock Slicing Machines
Understanding the technical specifications of rock slicing machines is essential for anyone working in geology or fossile preparation. These specifications dictate how machines can be used effectively. When choosing a machine, it is crucial to consider factors such as slicing capacity, power requirements, and precision standards. These aspects determine not only the efficiency but also the quality of the sliced specimen. Therefore, being aware of these specifications ensures optimal performance and satisfaction in outcomes for both professionals and enthusiasts alike.
Slicing Capacity and Thickness Adjustments
The slicing capacity refers to the maximum width and length of the rock that the machine can accommodate. Different machines have varying capacities. For example, diamond wire saws offer larger slicing capabilities compared to band saws. This makes them suitable for larger specimens.
Thickness adjustments are equally important. Many modern machines feature adjustable settings to alter thickness, allowing users to produce slices that meet specific research or collection needs.
- Flexibility in Thickness: Being able to adjust thickness is particularly beneficial when dealing with delicate fossils or rare minerals.
- Efficiency: Machines with wide slicing capabilities enable rapid processing, which is crucial in large-scale research projects.
In this regard, selecting a machine with suitable slicing capacity and adjustable thickness can significantly impact research and collection efforts.
Power and Energy Requirements
Power and energy requirements play a vital role in the operational capacity of rock slicing machines. Machines typically require a certain amount of electric power to ensure efficient slicing. High-performance machines may demand higher energy yet provide better results in terms of speed and quality.
- Voltage and Wattage: Higher wattage often equates to improved performance, but assessing the electrical supply in the workspace is essential to ensure compatibility.
- Energy Efficiency: Opting for machines built with energy efficiency in mind can lead to significant cost savings over time.
Ultimately, understanding power and energy needs helps users avoid common pitfalls associated with excessive energy consumption and underperformance.
Precision and Accuracy Standards
Precision and accuracy are critical when slicing rock specimens. The quality of cuts can directly affect the value and study of geological specimens. Manufacturers often provide detailed specifications on the precision capabilities of their machines.
Users should consider:
- Measurement Tools: Many machines come equipped with tools that allow users to measure thickness and align rocks accurately.
- Calibration: Regular calibration is necessary to maintain chronic precision and accuracy in repeat cuttings.
"Precision in rock slicing machines ensures that researchers and collectors obtain the best possible specimen without losing essential details."
A machine that meets high precision standards will not only extend its longevity but also enhance the overall outcome of the slicing process. Hence, investing in machines that uphold stringent accuracy requirements can significantly benefit users in their geological endeavors.
Operational Procedures for Using Rock Slicing Machines
Operational procedures are the backbone of efficient and effective use of rock slicing machines. Understanding these procedures is crucial for geologists and fossil collectors alike. The steps involved in operating these machines not only ensure precision in slicing but also enhance the safety and quality of samples being prepared.
Preparing the Rock Sample
Before starting the slicing process, it is essential to prepare the rock sample thoroughly. This involves selecting a suitable specimen based on its size and type. The rock should be clean and free of loose material. Often, collectors should wash the rock with water to remove any debris.
Once cleaned, trim excess protrusions and irregularities, using tools like a hammer or chisel. This helps achieve uniformity, which is vital for the slicing process to ensure even cuts. Additionally, knowing the internal structure of the rock can be helpful. Some rocks may have layers or features of interest that require special handling.
Setting Up the Machine
Properly setting up the rock slicing machine is key to achieving optimal performance. Before beginning, ensure that the machine is placed on a stable surface. Check that all mechanical parts are in good working condition, avoiding any potential malfunctions during operation.
The next step is to secure the rock sample into the machine’s fixture. Make sure the rock is clamped tightly to avoid any movement while slicing. This ensures accuracy and prevents unwanted vibrations. Additionally, set the slicing parameters on the machine. Adjust the thickness of the slice according to the desired end product, keeping in mind the specifications of the machine.
Executing the Slice
Once everything is set, it is time to execute the slice. Engage the machine slowly, allowing the blade to make contact with the rock gently. Patience is key at this stage. Rushing the process can lead to irregular slicing and may even damage the rock. Keep a constant check on the operation to ensure the machine is performing as expected. It’s advisable to monitor the path of the blade closely, as this can reveal any adjustments needed during the process.
After the slicing is completed, carefully disengage the machine and allow the blade to stop before removing the slice. Repeat the procedure as necessary for additional cuts.
Safety Protocols
Safety is paramount when operating rock slicing machines. First, always wear protective gear, including safety glasses and gloves, to shield yourself from flying debris. Ensure that the workspace is clear and organized to prevent accidents.
Regularly inspect the equipment for any signs of wear or damage. Make sure to follow the manufacturer’s guidelines regarding the maintenance of the machine. Familiarize yourself with the emergency stop feature and ensure that it's functional. If at any point the machinery behaves unexpectedly, stop the operation immediately to assess the situation.
It is also recommended to work in a well-ventilated area. Many rocks can produce harmful dust when cut. Taking precautions seriously can prevent injuries and ensure a smooth workflow.
"A thorough preparation and adherence to operational procedures can significantly enhance the quality of rock samples prepared for analysis and display."
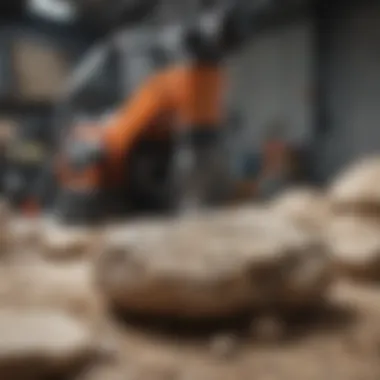
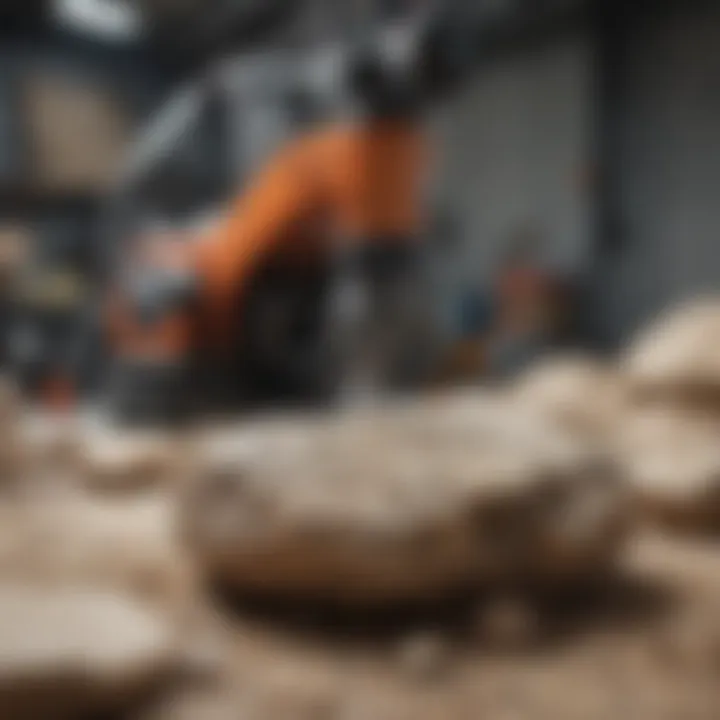
Applications of Rock Slicing Machines
In the field of geology and paleontology, the applications of rock slicing machines are crucial. These machines serve various purposes, making them indispensable tools for researchers, collectors, and enthusiasts. Understanding the different facets of these applications enhances the appreciation and utilization of rock slicing technologies.
Use in Geology Research
Rock slicing machines are vital in geology research for several reasons. They allow for precise slicing of rock samples into thinner sections without damaging the specimen. Thin sections are essential for microscopic analysis, helping geologists to study mineral composition, grain size, and structural features.
By preparing rock slices with accuracy, researchers can gather critical data that enhances their understanding of geological formations and processes. Through this, valuable insights into the Earth’s history and evolution emerge. Furthermore, advanced slicing technologies improve repeatability and consistency in sample preparation, making results more reliable.
Collection Preparation for Mineral Enthusiasts
For mineral collectors, rock slicing machines play a significant role in preparation and presentation. Properly sliced specimens can highlight unique mineral characteristics, making them more visually appealing. Collectors often seek to display their collections in ways that enhance their natural beauty and uniqueness.
These machines enable enthusiasts to create polished, uniform slices of minerals, which can be used for display or further study. Ensuring that the sections are appropriately cut enhances both aesthetic appeal and educational value. With the right slicing techniques, collectors can reveal internal structures or color variations that may not be visible in bulk specimens.
Fossil Preparation Techniques
Fossil preparation is another intriguing application of rock slicing machines. Fossils, often embedded within rock matrices, require careful extraction to prevent damage. By using these machines, paleontologists can create thin slices of the surrounding rock, allowing them to analyze fossils while keeping them intact. This is crucial for studying the fine details and patterns that inform researchers about ancient life forms and their environments.
Slicing also aids in the preservation of fossils. By minimizing mechanical stress during preparation, the likelihood of fractures or other damages is reduced. Prepared fossils can then be studied or displayed in museums, providing insight into the history of life on Earth.
"Rock slicing technology not only enhances the quality of specimen preparation but also expands the horizons of scientific research in geology and paleontology."
In summary, the applications of rock slicing machines extend beyond simple cutting. They are tools capable of transforming research methodology, enriching mineral collections, and preserving invaluable fossils. Understanding these applications allows users to maximize the potential of their equipment, ensuring precision and quality in their work.
Innovations in Rock Slicing Technology
The field of rock slicing has seen remarkable advancements in recent years. These innovations not only enhance efficiency but also improve the quality of the slices produced. Understanding these changes is essential for both professionals and enthusiasts. The modern rock slicing machines integrate innovative technologies that tailor the process to various rock types and intended applications. This section discusses key aspects such as numerical control systems, advanced blade designs, and digital imaging integration.
Numerical Control Systems
Numerical control systems have revolutionized the operation of rock slicing machines. These systems allow for precise control of cutting parameters. Settings such as speed, feed rate, and blade position can be adjusted with extreme accuracy. This level of control reduces material waste and ensures that every slice maintains a consistent thickness.
With numerical control, operators can easily replicate slicing processes across multiple samples. This consistency is important for research purposes, where reproducibility is crucial. Furthermore, modern systems come with user-friendly interfaces, enabling quick learning curves for new users. As a result, these systems cater to both advanced users and beginners, supporting their various needs in the rock slicing process.
Advanced Blade Design
The design of blades used in rock slicing machines has evolved significantly. Recent advances focus on improving durability and efficiency. For instance, diamond blades, known for their hardness, are increasingly popular. They provide cleaner cuts with minimal chipping. Innovations in blade manufacturing also include the development of specialized coatings that enhance performance and lifespan.
Additionally, the geometry of blades is being optimized. This involves alterations in thickness and shape to suit different materials. A well-designed blade can improve overall slicing speed and reduce energy consumption. Collectors and researchers benefit from these advancements, as they permit finer details in their specimens without compromising structural integrity.
Integration with Digital Imaging
The integration of digital imaging technologies alongside rock slicing machines offers substantial advantages. This method allows collectors to capture high-resolution images of the slices during the cutting process. Such imaging facilitates better analysis and documentation of samples.
With advanced imaging, users can assess the internal structures of rocks and fossils before making critical cuts. This proactive approach minimizes the risk of damaging valuable specimens. Furthermore, with the ability to document every step, sharing findings within the geological community has become seamless. Collaborations are easier as practitioners can visually present their work through digital media.
These innovations are not merely technical upgrades; they represent a transformation in how geological specimens are prepared and studied.
Overall, these advancements in rock slicing technology do not just improve cutting efficiency. They contribute to the overall experience for collectors and expedite research in geology. Understanding and adopting these innovations can vastly improve outcomes, whether in professional or amateur contexts.
Comparative Analysis of Rock Slicing Machines
The comparative analysis of rock slicing machines is an essential aspect of understanding the broad landscape of tools available for geology and paleontology. In an environment where precision and efficiency are paramount, a well-done comparison helps researchers and collectors make informed choices. It considers various factors like cost, performance, and specific user needs. This section highlights these crucial elements and their implications for both hobbyists and professionals.
Cost versus Efficiency
The balance between cost and efficiency can dictate purchasing decisions for rock slicing machines. It is critical to assess how much one is willing to invest against how effectively the machine performs its tasks.
- Price Range: The market offers a variety of machines, from entry-level options costing several hundred dollars to professional-grade machines exceeding tens of thousands.
- Operating Cost: Beyond initial outlay, users must consider ongoing costs such as blade replacements and electricity.
- Slice Quality: Cheaper machines may save upfront cash, but they can compromise slicing quality, leading to wasted material and additional effort in refining the samples.
A key point here is to match the machine's capabilities with the expected workload and the budget available. Spending a bit more upfront for a higher-efficiency machine can result in greater long-term savings, both in time and resources.
Portability and Size Considerations
When selecting a rock slicing machine, portability and size become significant factors, particularly for users who may need to transport their machines or work within limited spaces.
- Weight and Dimensions: Lightweight and compact machines can be more convenient but may not have the same slicing power as larger models. Conversely, heavy machines often provide stability but can be cumbersome when moving between locations.
- Workspace Availability: Potential users should assess their workspace dimensions. Machines that are too large can limit operational efficiency and may not fit well in smaller labs or workspaces.
- Mobility Features: Some models incorporate wheels or other mobility aids that enhance portability, catering to fieldwork demands or mobile laboratories.
A thoughtful analysis of these factors can steer users toward a machine that best suits their operational environment, enhancing their overall productivity.
"The decision-making process surrounding the purchase of a rock slicing machine requires careful consideration of both cost and functional performance to maximize satisfaction and efficiency in operations."
Maintenance of Rock Slicing Machines
Maintenance of rock slicing machines is critical for ensuring their longevity and performance. These machines represent a significant investment for collectors and researchers. Regular maintenance can help prevent unexpected breakdowns, improve operation efficiency, and maintain slicing accuracy. A well-maintained machine can also enhance the quality of rock specimens prepared for study or display. Thus, it becomes paramount for users to adopt a diligent maintenance routine.
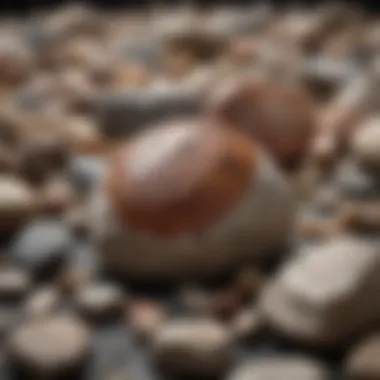
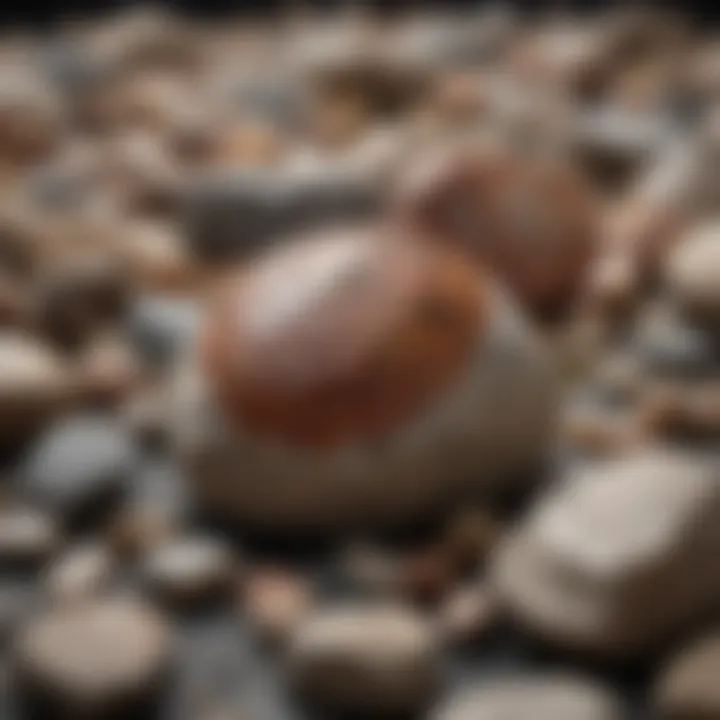
Routine Maintenance Checks
Routine maintenance checks serve as the foundation for the effective functioning of rock slicing machines. These checks should include:
- Cleaning: Regularly removing dust and debris from machine surfaces, especially around cutting blades, can prevent wear.
- Lubrication: Machines often contain moving parts that require lubrication to function smoothly. Delaying this can lead to mechanical issues.
- Blade Inspection: Periodic checking of slicing blades for dullness or damage is vital. Using a worn blade will negatively affect slice quality.
- Calibration: Ensuring that the machine is properly calibrated for thickness and angles aids in achieving precise cuts. This is especially important for research purposes.
Failure to perform these checks may lead to serious technical problems and could compromise the integrity of specimens.
Troubleshooting Common Issues
Even with regular maintenance, users may encounter issues with their rock slicing machines. Knowing how to troubleshoot common problems can save time and minimize frustration.
- Uneven Slices: This can be caused by an improperly calibrated machine or a dull blade. Users should recalibrate and inspect the blade.
- Vibrations: Excessive vibrations can indicate loose parts or improper setup. Inspect all components and tighten any loose screws.
- Excessive Heat: If the machine overheats, it may signify insufficient lubrication or that it is overloaded. Operators should ensure that the machine is not being pushed beyond its capacity, along with confirming proper lubrication.
For deeper insights into operational efficiencies and machine maintenance, users can explore resources like Wikipedia or community discussions on Reddit.
"Proper maintenance is not only a matter of keeping a machine operational; it significantly enhances the quality of the specimens prepared."
Considerations for Choosing a Rock Slicing Machine
Choosing the right rock slicing machine is crucial for anyone engaged in geology or fossil preparation. Each machine serves different purposes, and a selection must reflect personal or professional needs. This decision affects the quality of work, efficiency, and overall satisfaction. Key factors include user requirements, budget constraints, and available space.
User Requirements and Expectations
The first step in selecting a rock slicing machine involves understanding user requirements. Geologists and collectors may have varied expectations depending on their application.
- Type of Rock: Different rocks require specific cutting methods. For instance, a diamond wire saw might be ideal for hard materials while a flat saw can handle softer stones.
- Precision Needs: High-precision cuts are vital for research samples, whereas rough cuts may suffice for general collection purposes.
- Ease of Use: Machines should cater to the skill level of the user. Beginners may prefer user-friendly models, while seasoned professionals might seek advanced features for intricate tasks.
Clearly defining these expectations helps narrow choices significantly. Having clarity on the intended use reduces the chances of dissatisfaction.
Budget Constraints
Budget plays a significant role in the decision-making process. Users should consider their financial capacity before purchasing a machine.
- Initial Cost: Rock slicing machines vary in price based on type and sophistication. Higher-end models offer advanced features but come at a premium.
- Operating Costs: Beyond initial investment, users should account for long-term expenses like maintenance, replacement parts, and energy consumption. These factors cumulatively impact the overall cost of ownership.
- Cost-Benefit Analysis: Analyze the benefits derived from the machine relative to its cost. A more expensive option may be justified if it significantly enhances productivity or quality.
Balancing budget against features can lead to better purchasing decisions.
Space Availability
The physical space available for machinery setup is another essential consideration. Space constraints can significantly influence machine choice and operational efficiency.
- Size of the Machine: Some machines require considerable space for installation and operation. Compact models may fit better in smaller workshops but might not offer the same functionalities as larger options.
- Operational Flow: Consider how the machine will integrate with the existing workspace. Efficient layouts improve workflow and can ultimately enhance productivity.
- Storage Needs: Additionally, ensure there is adequate space for storing tools and materials associated with the slicing process.
Being aware of spatial limits ensures a smooth transition to machine use without disruptive adjustments.
Choosing the right rock slicing machine involves careful evaluation of user expectations, budget restraints, and applicable space. Understanding these elements facilitates informed decisions, ensuring the right tools are utilized to meet specific geological or paleontological needs.
Future Trends in Rock Slicing Machines
The field of rock slicing machines is evolving rapidly. As technology advances, it is crucial to consider how these innovations will shape the future operations of these machines. Considering factors such as efficiency, sustainability, and user-friendliness can provide significant benefits to both professionals and hobbyists in geology and paleontology. Understanding these trends will not only inform better purchasing decisions but also enhance the overall user experience.
Automation and Robotics
Automation is becoming a prominent feature in rock slicing technology. The integration of robotics enhances both precision and efficiency in the slicing process. An automated system can minimize human error, which is vital for maintaining the integrity of delicate rock samples. As automation becomes more common, operators can focus on critical tasks such as analyzing sample quality rather than performing repetitive slicing actions.
There are several advantages to this trend:
- Increased Accuracy: Robots can execute slices with consistent precision, reducing wastage.
- Time Efficiency: Automated machines can operate continuously, significantly increasing output compared to manual processes.
- User Accessibility: Operating these advanced machines will require less technical skill, allowing more individuals to engage in rock slicing.
Eco-friendly Operations
Sustainability is a pressing concern across all industries, and rock slicing machines are no exception. Future designs will likely focus on eco-friendly operations to minimize environmental impact. From energy-efficient motors to the use of biodegradable lubricants, manufacturers are under pressure to innovate toward more sustainable practices.
Benefits of eco-friendly operations include:
- Reduced Carbon Footprint: Utilizing renewable energy sources will lower emissions during the slicing process.
- Waste Reduction: Improved designs can lead to better management of off-cuts and waste materials.
- Long-term Cost Savings: While initial investments in eco-friendly technologies might be higher, the reduced operating costs can offset expenses over time.
“The shift toward sustainable practices is vital not just for the environment but also for ensuring the longevity of resources within geology.”
Ending
In the realm of geology and paleontology, rock slicing machines play a pivotal role. These machines allow for the precise preparation of rock samples, crucial for research and study. The ability to slice rocks not only aids in enhancing the clarity of samples but also contributes to the accuracy of both geological and paleontological findings.
Summarizing the Importance of Rock Slicing Machines
Rock slicing machines enable professionals and hobbyists alike to achieve a level of detail that manual techniques simply cannot. They provide several distinct benefits:
- Precision: The ability to adjust blade settings ensures consistent slicing, allowing specimens to be prepared without damage.
- Efficiency: Modern machines reduce the time spent preparing samples significantly, thus increasing productivity.
- Versatility: These machines are applicable across various research fields, including geology, archeology, and paleontology, making them essential tools for many scientists.
Furthermore, the recent innovations in rock slicing technology—such as advanced digital systems and eco-friendly operations—highlight the importance of these machines in the future. Collectors benefit immensely from understanding the different types and operational techniques associated with rock slicing machines.
"The evolution of rock slicing machines is crucial to the advancement of geological and paleontological research."
As the demand for detailed and accurate specimens grows, so too must the understanding and appreciation for the machines that make such work possible.