Exploring Rock Cutting Tools: Techniques and Applications
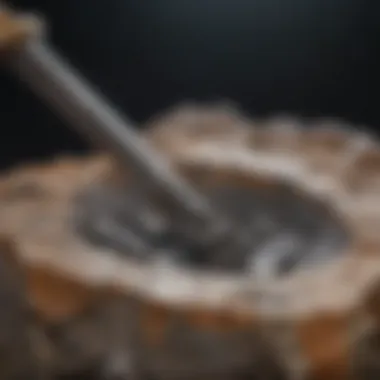
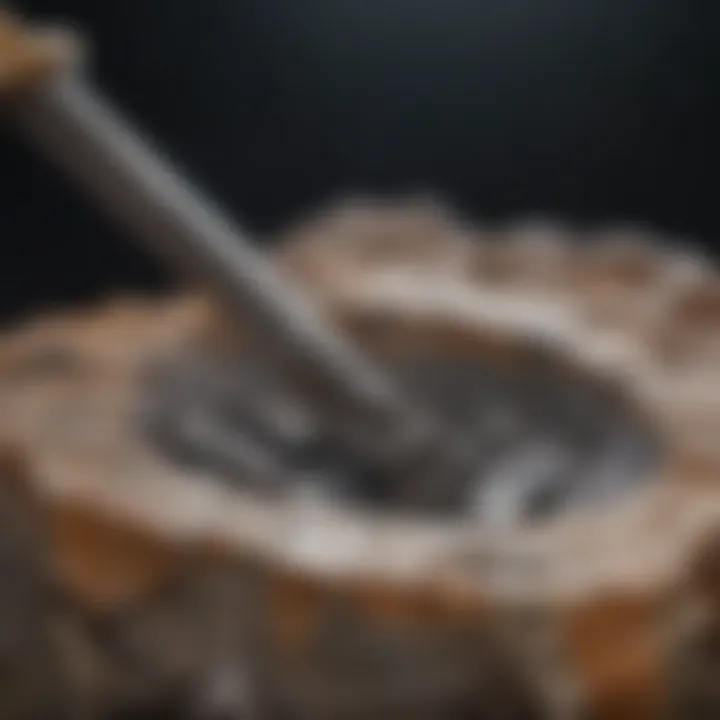
Intro
In the realm of geology and construction, the tools we use to cut through rock are more than just equipment—they are the lifelines that connect various industries. Every swing of a drill or rotation of a saw blade holds significance, especially when colossal natural materials are involved. Rock cutting tools are not merely artifacts of industry; they are technological marvels that embody engineering prowess and evolutionary advancements. In this exploration, we will uncover the types of rock cutting tools, the materials that form them, the technologies that propel them forward, and their multifaceted applications in fields such as mining, construction, and even paleontology.
History and Origins
Overview of Rocks and Fossils
The history of rock cutting tools is intertwined with humanity's desire to manipulate the natural world. From early stone implements used by our ancestors to today’s sophisticated machines, we have witnessed an incredible evolution. Initially, humans might have relied on quartzite or flint to create sharp edges for cutting. Over millennia, as civilizations advanced, so did the complexity and variety of tools.
Rocks, in their varied forms, have fascinated people for centuries. Early rock and fossil collectors discovered that within these natural resources lay evidence of our planet's history. Fossils, often preserved in sedimentary rock, tell stories of life that walked millennia before, capturing the imagination of scientists and enthusiasts alike.
Historical Significance and Cultural Impact
The impact of rock cutting tools extends beyond mere functionality. In many ancient cultures, stone tools were vital for survival and were often regarded as sacred objects. The transition from simple stone tools to advanced machinery mirrors humanity's journey toward civilization. For instance, the use of iron in tools marked a significant technological leap.
Rock cutting also had economic implications; mining tools transformed regions, influencing trade routes and economic power dynamics. Additionally, cultural artifacts, such as sculptures carved from marble, highlight how tools could elevate artistic expression, reinforcing their significance beyond the practical.
"Tools shape our interaction with the world—through them, we carve our niche in the fabric of history."
Identification and Classification
Guide to Identifying Rocks and Fossils
Understanding rock cutting tools requires a keen eye for identification. Different types of rocks and fossils demand specific tools tailored to their characteristics. For example, identifying sedimentary, igneous, and metamorphic rocks involves knowing their textural and mineralogical traits. This knowledge is essential for collectors and professionals alike.
Common Types and Variations
When it comes to rock cutting tools, there's a vast range. Here are some common types:
- Diamond saws: Often used in slicing through hard rock, they offer precision and durability.
- Rotary drills: These tools are essential for creating boreholes in mining.
- Wire saws: Preferred for their ability to cut through stone without excessive waste.
- Chisels and hammers: Basic yet effective for manual cuts, still used by artisans today.
Each type of tool has its unique set of specifications and requires understanding the materials being handled. Whether dealing with granite or limestone, the right tool can make all the difference.
Prolusion to Rock Cutting Tools
Rock cutting tools hold a pivotal role in a variety of industries by shaping and manipulating materials that constitute our natural world. The relevance of these tools cannot be humbly stated; they facilitate everything from resource extraction to infrastructure development. Understanding rock cutting tools involves dissecting their types, operational mechanisms, and areas of application. This lays the groundwork for appreciating the evolution and future trajectory of technologies that shape our physical landscape.
The advent of robust rock cutting methods has propelled advancements in fields such as mining and construction. Specialists in these domains must select tools adeptly tailored to handle varying rock conditions, leading to more efficient operations. Techniques can range from mechanical cutting to laser applications. The rise of automation and smart technologies introduces a new chapter in rock cutting where precision and efficiency align with the growing need for productivity.
Hammering down on the fundamentals, it’s vital to grasp the definitions and historical context before delving deeper into the intricate web of modern rock cutting technologies.
Defining Rock Cutting Tools
Rock cutting tools are instruments designed to slice, carve, or fracture rock with efficiency. Tools can be mechanical, using physical force, or incorporate advanced technologies like lasers and water jets that employ different principles of physics.
These tools are not mere accessories; they dictate how effectively rock can be managed in various situations. Mechanical tools include items like saws and grinders, while diamond tools utilize the exceptional hardness of diamonds to penetrate even the toughest materials. Each tool serves a specific purpose, indicating the importance of careful selection based on the task at hand. Understanding this foundational concept sets the stage for an exploration of their classifications and applications.
Historical Overview
The historical journey of rock cutting tools can be traced back thousands of years. Early humans used rudimentary implements made of stone and wood for their basic rock cutting needs. As technology advanced, so did the tools – from primitive chisels to the sophisticated devices we see today.
In the 19th century, the industrial revolution sparked a wave of innovations. The arrival of steam-powered machinery transformed rock cutting methods, enabling mines to penetrate deeper and extract minerals more efficiently. This was a major breakthrough; however, it was not without challenges. Early machinery was often unwieldy and inefficient, highlighting the necessity for continual improvement and adaptation.
As we moved into the 20th century, the introduction of diamond and carbide cutting tools marked a significant turning point. These materials brought about a new era of precision and performance that laid the groundwork for modern-day tools.
Today, we are witnessing a dual revolution fueled by electronic innovations and environmental considerations. Making sense of this historical backdrop offers valuable insights into current practices and foreshadows future developments in rock cutting technologies.
Classification of Rock Cutting Tools
In the vast & ever-evolving landscape of rock cutting, knowing the various types and their specific uses becomes key. Classification of rock cutting tools isn't just a dry academic exercise; it plays an essential role in selecting the right tool for the job, impacting efficiency, cost, and ultimately, success in both industrial and hobbyist applications like collecting fossils. Understanding these classifications helps users make informed decisions and optimizes their cutting processes.
Mechanical Tools
Mechanical rock cutting tools have been around for ages and remain a staple in many operational settings. These tools generally use physical force to break down rock into manageable pieces. A good old-fashioned example includes chisel and hammer—simple yet effective when precision is needed in smaller areas. Traditional drills often fall under this category as well, employing various bits to bore through rock.
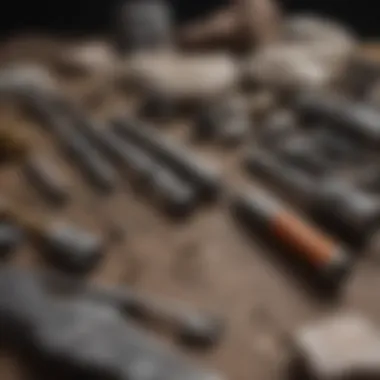
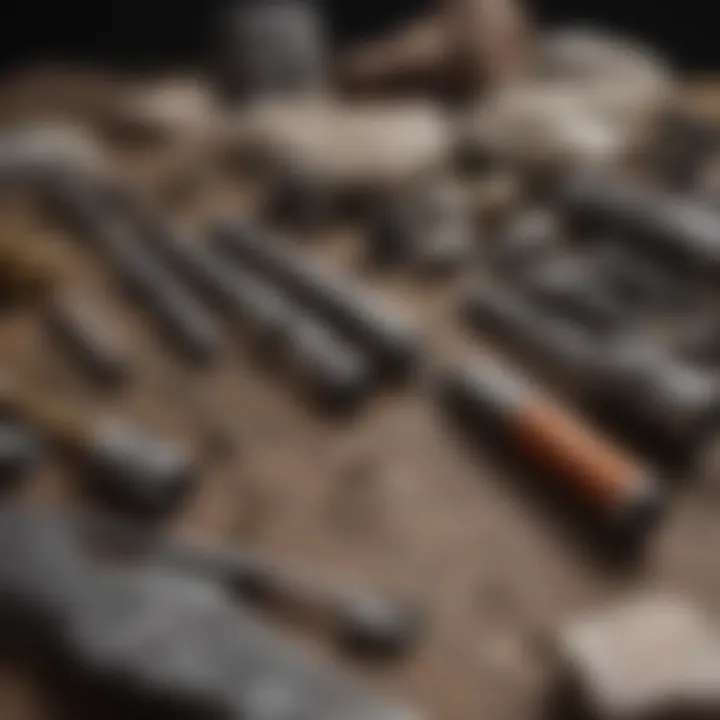
It's worth mentioning that these tools require skill and a certain level of physical strength, but they also offer fine control. For instance, quarrymen have used hand drills in historical sites, where every strike counts—both for the quality of cut and the preservation of the surrounding material. However, as jobs became more substantial and time-sensitive, heavy machinery like jackhammers or rig-mounted drills became necessary.
Some benefits of mechanical tools include:
- Direct control over cutting depth and angle.
- Lesser initial investment in specialized equipment.
- Enhanced tactile feedback for artisans and skilled workers.
Diamond Tools
When it comes to efficiency and cutting speed, diamond tools are in a league of their own. Infused with industrial-grade diamonds, these tools provide unmatched hardness, making them ideal for cutting through incredibly tough materials.
Examples of diamond tools include saw blades and grinding wheels. While diamond tools can be expensive, their longevity and cutting precision can save substantial costs in the long run. Moreover, their versatility makes them suitable for various applications from mining to construction and even intricate work required in paleontology, like preparing fossils for display.
Here are some points about diamond tools:
- High durability: They last much longer than their metal counterparts.
- Versatility: Can cut various materials with ease.
- Precision: Enables fine detailing, especially when working on complex features.
Water Jet Tools
Water jet cutting represents a unique approach, utilizing the force of high-pressure water to slice through rock. This method is particularly effective for materials sensitive to temperature changes since it doesn't generate heat, thus avoiding thermal distortion.
Water jet tools are gaining traction in various industries, including surgery, where precise cuts are indispensable. Moreover, rock collectors find that a water jet can facilitate delicate tasks without altering the rock's characteristic appearance. The advantages of water jet tools include:
- Precision cutting: Maintains the integrity of complex rock structures.
- Minimal waste: It’s an efficient process, saving both time and materials.
- Environmental friendliness: Uses water as the cutting medium, reducing harmful emissions.
Laser Cutting Tools
Laser cutting tools have emerged as one of the most sophisticated options in the rock cutting realm. This technology involves using focused laser beams to melt away rock material in a controlled manner. The precision of laser cutting tools allows for intricate and clean cuts that other methods simply can’t achieve. It's especially useful in applications where detail matters, such as crafting small decorative pieces with fossils.
Despite their advantages, cost can be a limiting factor for some users. However, for serious professionals or collectors, investing in laser technology can yield significant benefits over time. Key points about laser tools include:
- High precision: Capable of achieving intricate designs and cuts.
- Minimal maintenance: Unlike mechanical tools that get wear and tear, lasers often require less upkeep.
- Speed: Can perform cuts significantly faster than traditional methods, allowing for higher productivity.
Materials Used in Rock Cutting Tools
Understanding the materials used in rock cutting tools is fundamental for anyone interested in the field, especially rock and fossil collectors. Each tool is crafted from specific materials that not only determine its effectiveness but also play a significant role in its durability and performance. With the right choice of material, rock cutting becomes more efficient, allowing for precise cuts with minimal wear on the tools.
Selecting appropriate materials impacts various aspects of rock cutting, including the type of rock being worked on, the cutting speed, and the wear resistance of the tools. This section will examine the primary materials utilized in the production of rock cutting tools, providing insights into their unique properties and applications.
Steel Alloys
Steel alloys are crucial in the creation of robust rock cutting tools. These materials are blended with other elements, enhancing their properties. For instance, adding chromium improves corrosion resistance, while nickel is known for enhancing toughness.
- Versatility: Steel alloys can be tailored to meet specific demands. This means tools can be made harder for cutting tougher rocks or softer for more delicate operations.
- Cost-Effective: Compared to other materials, steel alloys offer an economical option without sacrificing quality.
- Widely Available: As a material, steel is abundant and accessible, which makes it a popular choice among manufacturers.
However, it’s essential to consider that while steel is durable, it may not always be the best choice for extremely hard rocks like granite. When encountering such materials, a different approach, perhaps utilizing superhard materials, may be required to ensure effective cutting.
Hard Metals
Hard metals, often referred to as cemented carbides, are created by sintering metal powders under high temperature and pressure. These substances enable the manufacturing of tools that can withstand high forces without deforming or breaking.
- Incredible Hardness: Hard metals exhibit superior hardness, making them ideal for cutting operations in various mining and construction applications.
- High Wear Resistance: Tools made from hard metals maintain their cutting edges over prolonged use, enhancing their operational lifespan.
- Heat Resistance: They perform exceptionally well in high-temperature environments, which is often the case during rock cutting.
A common application of hard metals can be seen in drill bits used for mining operations. Their strength and durability ensure that they remain effective even when working on the toughest rock formations.
Carbide and CBN
Carbide, particularly tungsten carbide, serves as the backbone of many rock cutting tools. It boasts remarkable hardness and is often favored for its ability to retain sharp edges. CBN, or Cubic Boron Nitride, is another tough material that's increasingly used in cutting applications.
- Longevity: Tools made with carbide and CBN last significantly longer than those made with traditional materials, reducing the need for frequent replacements.
- Precision Cutting: These materials allow for finer cuts, which is particularly important in industries like paleontology, where precision is critical for fossil preservation.
- Cost Efficiency Over Time: While the initial cost may be higher, the extended product life leads to lower overall expenses in the long run.
It’s worth mentioning that both carbide and CBN tools excel in environments that demand high wear resistance, making them suitable for various applications that involve hard or abrasive materials.
"Choosing the right material for rock cutting tools not only extends their life but also enhances the precision and effectiveness of operations."
Mechanics of Rock Cutting
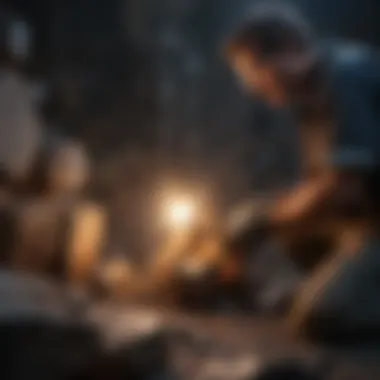
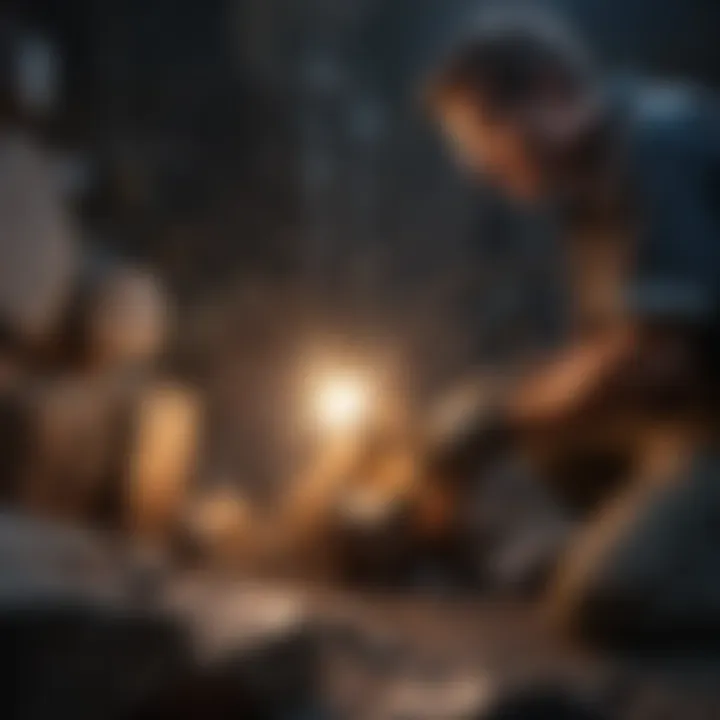
The mechanics of rock cutting play a vital role in understanding how various rock cutting tools perform in different contexts. This area of focus not only encompasses the cutting processes involved but also dives into the material properties that affect how tools interact with rock. By grasping these mechanics, enthusiasts and professionals alike can make informed decisions when selecting the right tools for their tasks.
Cutting Processes and Strategies
Different rock cutting methods have different ends. Choosing the right cutting strategy can often mean the difference between a job well done and a frustrating experience. One of the fundamental processes is abrasion, where hard materials grind away softer rock through friction. This method is common with diamond tools, which excel in cutting hard rock due to their toughness.
A second popular strategy is shearing, typically employed in mechanical tools, which slice through rock with sharp cutting edges. This method relies on the application of consistent force to ensure that the tool penetrates effectively without causing undue wear.
- Key cutting strategies include:
- Abrasion: Utilizes friction and particles to grind away rock.
- Shearing: Uses sharp edges to slice through rock material.
- Hydraulic: Employs high-pressure water to erode rock, commonly seen in water jet cutting tools.
Each strategy has its considerations. For instance, while water jet cutting offers a clean edge and minimal dust, it may struggle with harder materials. Conversely, using traditional mechanical tools might generate significant vibrations, impacting precision.
Understanding Material Properties
To properly engage in cutting rock, one must have a firm grasp of material properties. The hardiness and composition of the rock dictate how effective cutting tools can be. Rock hardness is measured on the Mohs scale, ranging from talc, the softest, to diamond, the hardest. Tools made coon with materials like carbide and CBN (Cubic Boron Nitride) shine in cutting through tougher rock, allowing for efficient operations in mining or construction.
- Key material properties to consider include:
- Hardness: Affects the choice of cutting tool.
- Brittleness: Determines how the rock will fracture under stress.
- Grain structure: Influences the overall ease of cutting and tool wear.
Before embarking on any project, it's crucial to analyze both the rock and the tools. Understanding these factors helps ensure that the selected tools will perform effectively and increase durability, thus optimizing outcomes.
Applications of Rock Cutting Tools
The applications of rock cutting tools span various industries, each leveraging the unique characteristics and functionalities of these tools to meet specific needs. Understanding these applications provides critical insights into their significance and versatility. From mining to construction, these tools are pivotal in shaping materials efficiently while balancing value and performance. Now, let's dive deeper into three primary areas where rock cutting tools shine: mining operations, the construction industry, and paleontological research.
Mining Operations
In the heart of our planet, rock cutting tools serve as the backbone of mining operations. Extracting valuable minerals and metals from the earth is no small feat, and the methods employed are crucial. The use of specialized cutting tools, such as diamond saws and water jet cutters, allows miners to precisely carve through hard rock layers, leading to higher yield and reduced waste. Not only does this enhance productivity, but it also makes the process safer.
- Efficiency: The precision provided by rock cutting tools, especially those utilizing diamonds, means less time spent on each cut.
- Safety: Tools designed for effective cutting minimize the risks associated with traditional drilling methods. Fewer vibrations result in more stability within tunnels and shafts.
- Environmental Considerations: Innovative practices like water jet cutting minimize dust and pollution, a growing concern in mining today.
"The right cutting tools can make or break a mining operation, both in terms of financial viability and safety."
Construction Industry
In construction, the versatility of rock cutting tools can’t be overstated. Building roads, laying foundations, or carving out tunnels all have one common need—effective material removal. Durable tools that can handle various types of rock contribute significantly to the efficiency of construction projects. In addition, rock cutting technology has advanced, enabling better control over the cutting process, which translates to:
- Precision Work: Tools designed for specific tasks can create clean cuts and fitments, improving the overall quality of construction.
- Reduced Downtime: Robust tool designs mean less wear and tear, keeping projects on schedule. This is crucial for contractors who face penalties for missed deadlines.
- Cost-Effectiveness: Investing in high-quality cutting tools can actually lower project costs by reducing repair and replacement expenses over time.
Paleontological Research
In a rather unexpected realm, rock cutting tools also play an essential role in paleontology. When researchers uncover fossils, they need to be delicate, yet thorough. The right tools allow paleontologists to extract fossils with care, preserving their integrity while providing access for study. The tools commonly used in this field include:
- Micro-Jets: These are small, precise water jets that can cut through rock without damaging the surrounding fossil.
- Diamond Drills: Ideal for making smooth cuts around fragile specimens, allowing for detailed research while ensuring minimal loss of material.
Through these applications, one can see that rock cutting tools are not merely utilitarian; they are instrumental in advancing various fields. The impact of these tools in mining, construction, and research highlights the intricate relationship between technology and achievement. As these industries continue to evolve, so will the tools that power their progress.
Key Factors in Selecting Rock Cutting Tools
Choosing the right rock cutting tool is pivotal for optimizing performance in various applications. Whether you're in mining, construction, or paleontological research, understanding the essential factors that contribute to the effectiveness of these tools can significantly impact both efficiency and overall results. Let's explore several key considerations that guide this selection process.
Rock Hardness and Composition
When it comes to cutting rock, one can't overstate the significance of the material's hardness and composition. Different rocks, such as granite, limestone, or sandstone, each present their own unique challenges. For instance, granite is notoriously tough due to its high level of quartz and other minerals, which demands the use of high-performing diamond or carbide tools.
Understanding the characteristics of the rock you intend to cut is crucial. Higher hardness translates often to a need for advanced tools that might come at a higher cost but ultimately save on time and maintenance. Conversely, if you're working with softer stones, the tools can be less complex and more affordable.
In selecting the right rock cutting tool, consider:
- Rock type: Identify if it's igneous, metamorphic, or sedimentary.
- Mineralogical composition: Knowing the minerals present can guide you to the best cutting technique.
- Hardness scale (Mohs scale): This scale helps measure how resistant the rock is to scratching.
The alignment between the tool choice and rock hardness doesn't just ensure faster cutting; it can also minimize tool wear and optimize working lifespan.
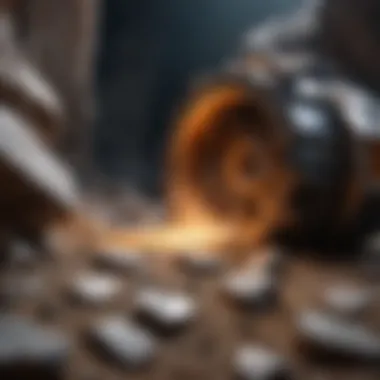
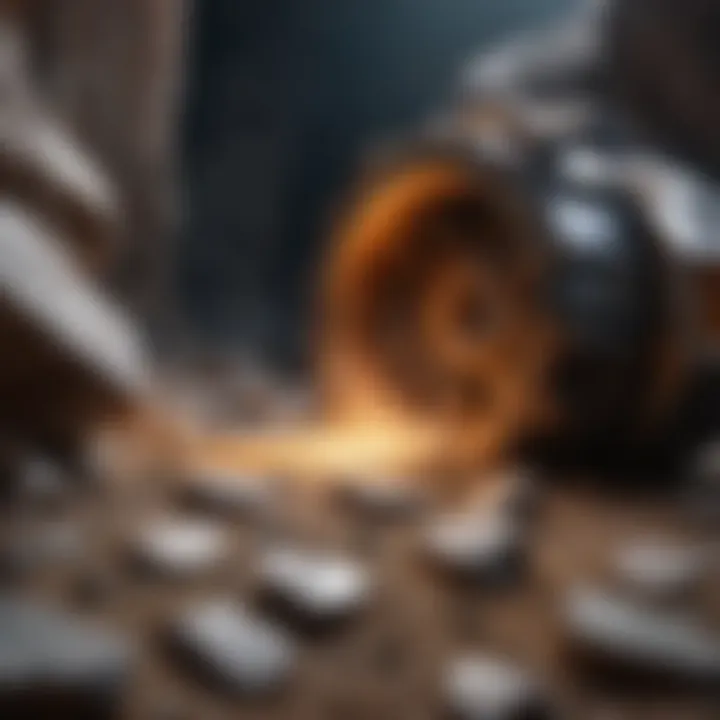
Tool Durability and Maintenance
Tool longevity and maintenance are also fundamental in ensuring cutting efficiency and cost-effectiveness. A cheap tool might fit the budget, but if it breaks or wears out quickly, it could cost more in the long run due to frequent replacements and repairs.
Durability covers several aspects:
- Material quality: Tools made from high-grade steel or specialized alloys generally outperform their cheaper counterparts. The grade of material will often dictate the lifespan in tough conditions.
- Design features: Consider tools designed for ease of maintenance. Features such as replaceable parts or straightforward cleaning methods can play a significant role in long-term usage.
- Manufacturer reputation: Well-known brands often invest more in research and development, resulting in tools that are both effective and durable. Recommendations from colleagues or industry forums can guide you toward the best models.
Regular maintenance practices are critical, too. Here are some tips:
- Keep the tools clean and lubricated to prevent rust and damage.
- Sharpen the blades regularly to maintain cutting efficiency.
- Inspect for wear and tear before and after each use.
In summary, choosing rock cutting tools is more than a mere transaction; it’s about understanding the interplay between your project requirements and the tools available. By considering factors like rock hardness and tool durability, you can navigate the market effectively and make informed choices that pay off down the line.
Technological Advancements in Rock Cutting
The field of rock cutting has seen some remarkable innovations over the past few decades. With the increasing demand for efficiency and precision across various industries, the advancement of rock cutting technologies stands as a key factor in maximizing productivity. These technological strides not only enhance the effectiveness of the tools used but also offer significant benefits in terms of time and resource management.
Automated Cutting Technologies
Automated cutting technologies are revolutionizing the way rock cutting operations are conducted. By minimizing human intervention, these technologies improve safety and accuracy. For example, automated systems can operate in extreme conditions where manual labor might pose risks, such as deep mines or remote geological sites. These machines use advanced sensors and algorithms to analyze materials and optimize cutting paths, ensuring minimal waste and maximum efficacy.
One notable example is the use of robotic arms fitted with diamond-tipped cutters. These machines can adjust their cutting speed and pressure based on real-time feedback. The implementation of such tech not only increases the speed of operations but also reduces wear and tear on tools, prolonging their lifespan.
In addition, automated technologies can be programmed for various cutting patterns, giving operators the flexibility to adapt to different rock types and project specifications without starting from scratch each time. Moreover, these systems are often integrated with monitoring software, allowing for data collection and analysis to continuously improve cutting strategies.
Smart Cutting Systems
Smart cutting systems are another key development in rock cutting technologies. These systems utilize artificial intelligence and machine learning to enhance the performance of rock cutting tools. Unlike traditional cutting techniques, smart systems process vast amounts of data to predict the optimal cutting conditions. They can learn from past operations, identifying when to adjust parameters for better outcomes. For instance, if a specific rock type proves difficult to cut, the system can automatically alter the speed, angle, or pressure applied without needing human input.
A prominent feature of smart cutting systems is their connectivity. With the rise of the Internet of Things (IoT), these systems can communicate with other devices, sharing performance metrics and operational data. Such connectivity promotes a collaborative work environment, allowing teams to address performance issues promptly. As a result, these innovations not only enhance efficiency but also pinpoint areas for further development in cutting strategies.
"The integration of AI in cutting technologies ensures precision and adaptability, tackling the complexities of rock types encountered on site."
Future Trends in Rock Cutting Tools
The rock cutting tools industry is on the brink of revolutionary transformations. As demands for efficiency, precision, and sustainability grow, adopting innovative technologies becomes crucial. In this section, we explore future trends enhancing rock cutting practices and shaping the tools themselves.
Sustainability Considerations
In recent years, the conversation around sustainability in the mining and construction sectors has gained significant traction. Adopting greener practices is not just a trend but a necessity that many organizations are embracing. The global focus on reducing environmental impact has led to several advancements in rock cutting tools.
- Eco-friendly materials in tool production reduce the carbon footprint. Manufacturers are investigating the use of recycled or bio-based materials without compromising durability.
- Waste management has become a priority. Innovations in cutting techniques are now trying to minimize waste generation during rock removal processes. For instance, improvements in precision cutting lead to less rubble, ultimately benefiting both the environment and cost efficiency.
- Energy-efficient processes are also at the forefront. Newer tools are designed to consume less power during operation, which not only reduces costs but also supports sustainability goals.
Taking these factors into account means companies can contribute positively to the environment while still meeting their operational goals.
Integration of AI in Cutting Techniques
Artificial Intelligence (AI) is transforming various industries, and rock cutting is no exception. The integration of AI in rock cutting tools marks a significant step towards smarter cutting solutions. Here’s how AI is influencing the field:
- Predictive Analysis: AI algorithms can analyze vast amounts of geological data. By doing so, they predict rock behavior under different cutting conditions, enabling operators to adjust parameters for optimal performance and reduced wear on tools.
- Automation: Increasing levels of automation are reducing the need for manual intervention in rock cutting. Automated systems equipped with AI can operate 24/7, which enhances productivity and minimizes human error.
- Feedback Systems: With integrated sensors, tools can provide real-time data on performance and conditions. AI analyzes this data, allowing for adjustments to be made on the fly to ensure effective and efficient cutting operations.
- Training Programs: AI can enhance the training of operators by simulating various scenarios, enabling hands-on experience without the associated risks.
"The integration of AI not only improves efficiency but also catalyzes innovation in rock cutting technologies, aligning with the industry's push towards smarter and more capable solutions."
Embracing these tech advancements will propel the rock cutting industry into a new era, one characterized by efficiency, sustainability, and a greater capability to meet today's challenges. As trends evolve, keeping an eye on these innovations will be key for professionals looking to maintain a competitive edge in rock cutting practices.
Culmination
The significance of concluding a discussion on rock cutting tools can't be understated. In this article, we've traversed a wide array of facets related to these essential instruments in various industries. Rock cutting tools, with their intricate designs and specialized materials, play a pivotal role in sectors such as mining, construction, and even in the study of paleontology. Understanding these tools isn’t just for the specialists but also for those who have a budding interest in geology or rock and fossil collecting.
Summarizing Key Insights
- Diversity of Tools: We've examined a variety of rock cutting tools, from the robust mechanical tools to advanced laser cutting techniques. Each type serves a unique purpose, adapting to the diverse hardness and composition of the rocks being worked on.
- Material Composition: The materials used in crafting these tools, including steel alloys and diamond, play a crucial role in their effectiveness. Different environments and rock types necessitate different materials for optimal performance.
- Mechanics and Applications: An understanding of the physics behind rock cutting, combined with practical applications, equips both professionals and enthusiasts with the knowledge necessary to make informed decisions.
- Technological Advancements: The article touched on the latest innovations in rock cutting technologies, emphasizing the importance of staying updated as the field evolves. Trends like automated systems and AI integration are paving the way for more efficient and sustainable practices.
Ultimately, knowing these elements helps establish a strong foundation for further exploration within the field and enhances the appreciation for the tools that shape our interaction with the Earth.
Future Research Directions
As we look ahead, several avenues warrant further investigation:
- Sustainability Practices: With increasing emphasis on environmental stewardship, researching sustainable practices in the production and use of cutting tools is crucial. How can we ensure that the extraction processes do not compromise ecological integrity?
- AI Applications: As artificial intelligence continues to grow, its potential application in rock cutting apparatuses could revolutionize the field. Future studies could explore how machine learning can enhance precision or predict maintenance needs.
- Material Innovation: Delving into newer materials—such as composites or recycled materials—could yield tools that are not only effective but also environmentally friendly.
By addressing these prompts, researchers and enthusiasts alike can help in pioneering advancements that may redefine rock cutting practices for generations to come.