Insight into Rock Cutting and Polishing Machines
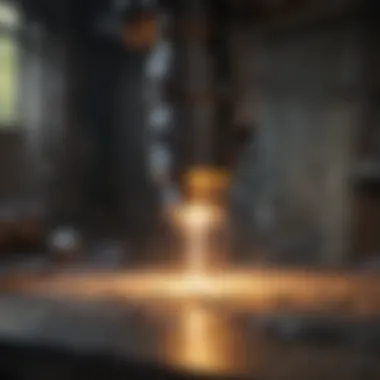
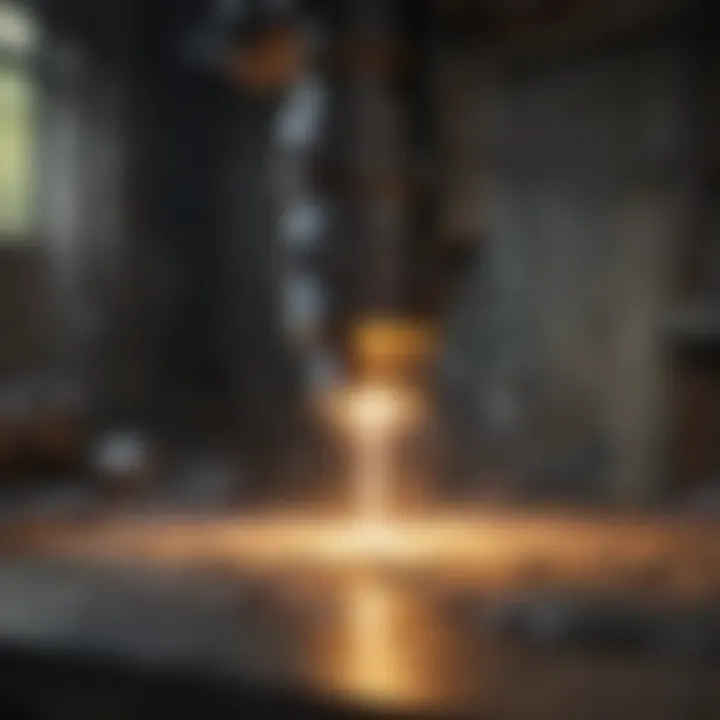
History and Origins
The journey into the world of rock cutting and polishing machines not only dives into the mechanical prowess but also sheds light on the rich history that surrounds them. Understanding the origins of these machines offers insight into their evolution and significance within the geological and collectibles communities.
Overview of Collectibles, Rocks, and Fossils
For millennia, humans have had an intrinsic fascination with rocks and fossils. From early man using in situ stones for tools to the contemporary hobbyist hunting for that perfect specimen, the allure of these natural treasures never fades. Collectibles such as quartz crystals, agates, and fossils not only serve decorative purposes but also provide educational opportunities through their study.
Rock cutting and polishing machines emerge as key players in this narrative, converting rough stones into polished gems. For collectors, this process is invaluable. Without these machines, many beautiful yet rugged pieces would remain hidden in their raw forms, untouched by the artistry that categorizes them as collectibles. The trend has shifted over time; many hobbyists now seek machines themselves, taking the craft into their own hands, rather than relying solely on external sources for rock processing.
Historical Significance and Cultural Impact
Digging deeper, you find that the crafting of stones has roots that stretch back thousands of years. The ancients recognized the beauty and utility of various minerals, employing rudimentary tools to shape them. Fast forward to the 19th century, technological advancements brought about powered machines that drastically transformed the gem and fossil industries. In the age of industrialization, machines like the lathe and saw were crucial for efficiently cutting and shaping stones, reducing labor and increasing production.
"History shows us that technology does not merely create jobs; it transforms what we believe is possible. Rock cutting machines exemplify this principle in action."
Today, rock cutting and polishing machines are not merely tools; they reflect culture's embrace of art in nature. In many communities around the world, these machines have paved the way for small businesses and craftspeople, allowing individuals to foster relationships with clients who appreciate the beauty and uniqueness of their craft. The machines enable a three-dimensional exploration of nature’s artistry, encouraging a more nuanced appreciation of the stones we see every day.
Identification and Classification
Understanding the machinery used for rock processing creates a foundation for collectors to identify and classify their specimens more effectively. This section provides an essential guide to recognizing various types of stones and fossils, enhancing the learning experience further.
Guide to Identifying Rocks and Fossils
Identification begins with observation. To the untrained eye, a rock might seem like just a stone, but with knowledge, one can uncover its backstory. Texture, color, and hardness are among the primary characteristics to consider. A simple scratch test can differentiate between a quartzite and other, softer materials. To facilitate identification, keep a field guide handy or utilize smartphone apps that are specifically designed for rock identification.
A useful strategy is to follow processes:
- Examine for luster: Is it shiny, dull, or glassy?
- Assess the grain: Is it coarse or fine?
- Conduct the scratch test: What surface does it leave behind?
Common Types and Variations
Different rocks and fossils vary broadly, and being informed about distinct categories can significantly enhance one’s collecting experience.
- Igneous Rocks: Formed from cooled magma or lava, examples include granite and basalt.
- Sedimentary Rocks: These come from accumulated particles or organic material, like limestone and sandstone.
- Metamorphic Rocks: Created under pressure from other rocks, such as marble and schist.
When it comes to fossils, understanding the forms they may take can be a game changer for collectors. From impressions in sedimentary rock to preserved intact specimens encased in amber, they tell stories of life from ages gone by. Taking the time to identify the elements and stories behind these pieces significantly enhances the emotional connection to one’s collection.
By learning the history and classifications, collectors can appreciate their materials more deeply, forging a path to a richer involvement in their passion.
Understanding Rock Cutting and Polishing Machines
Rock cutting and polishing machines hold a unique place in the realms of geology and the collectibles industry. Their significance, while perhaps taken for granted by some, can hardly be overstated. These machines not only allow for the transformation of raw minerals into beautifully polished specimens but also enhance the understanding of the materials themselves. This narrative aims to unearth the details around their definitions, historical aspects, and the pivotal role they play in both collecting and industry.
Definition and Purpose
At its core, a rock cutting and polishing machine serves two primary functions: cutting and polishing. These machines come in various forms and sizes, but they all share the common goal of manipulating the physical characteristics of natural materials. Cutting machines typically employ various blades, like diamond blades or wire saws, to precisely slice through harder materials, yielding clean edges ready for further processing. Meanwhile, polishing machines finish the product, using laps and compounds to bring out the shine in stones, turning rough gems into eye-catching pieces of art.
The purpose goes beyond aesthetics as well. For collectors, a well-cut and polished rock enhances not only the display quality but also the perceived value. It’s about taking nature's artwork and enhancing it for presentation and appreciation. The meticulous process involved speaks to the craftsmanship that comes with achieving a perfect finish, showing the true colors and patterns of the rock or mineral.
Historical Background
The history of rock cutting and polishing technology is as rich as the minerals themselves. Humans have been utilizing tools to shape stones for thousands of years, starting from simple hand tools in ancient cave dwellings to more sophisticated machines seen today. Early on, stones were shaped and polished by hand, often using basic abrasives found in nature. Over time, as technology advanced, people began to invent powered machines that could perform these processes more efficiently.
The introduction of diamond blades in the 20th century marked a significant leap forward. Diamond, known for its hardness, significantly improved the precision and efficiency of cutting operations, making it feasible to work with tougher materials like granite and quartz. In the mid-20th century, the advent of motors and electrical energy transformed these machines, enabling mass production and bringing rock processing into the modern era.
Importance in Collecting and Industry
The role of rock cutting and polishing machines is critically important for various stakeholders in the industry. For collectors, these machines are not just tools; they are gateways to understanding the beautifully complex structures of the earth's crust. A collector who has access to high-quality cutting tools can unlock the hidden beauty within a rough specimen. It allows them to redefine their collections, showcasing not just the stones themselves but the stories they tell about their era, composition, and origin.
Moreover, within the industry, these machines provide commercial viability for miners and traders. A polished stone, be it a gem or a mineral specimen, fetches a higher price than its unrefined counterpart. The economics of natural resources heavily rely on the efficiency of these machines in enhancing product quality. Thus, the investment in rock cutting and polishing technology often yields significant returns, benefitting collectors, businesses, and enthusiasts alike.
In the end, understanding rock cutting and polishing machines is essential for anyone involved in geology or collecting, as it paves the way toward appreciating the natural beauty of rocks and their potential as refined art.
Types of Rock Cutting Machines
The world of rock cutting machines features a variety of tools designed for specific tasks. Each type of machine has its own set of benefits and considerations, making it essential for collectors and hobbyists to understand the differences among them. With a range of options, selecting the right machine can dramatically enhance efficiency and results. This section will explore three primary types: Diamond Blade Saws, Wire Saw Machines, and Water Jet Cutters.
Diamond Blade Saws
Diamond blade saws are among the most popular and versatile cutting tools in the industry. Equipped with blades embedded with diamond particles, these saws excel in slicing through hard materials like granite and quartz with remarkable precision.
Due to their hard-hitting nature and ability to handle various shapes and thicknesses, they are indispensable in both geological research and the crafting of beautiful specimens for collectors. Here are some key points about diamond blade saws:
- Efficiency: The cutting speed is exceptional, allowing for faster processing of materials.
- Longevity: Diamond blades are known for their durability, often outlasting other types of blades, which can save money in replacements.
- Precision: The fine cuts made by diamond blades reduce the need for extensive finishing work, retaining the integrity of intricate designs.
However, collectors must consider costs associated with initial investment and maintenance, as these saws can be pricey. Yet, many believe that the investment pays off through the flawless results they deliver.
Wire Saw Machines
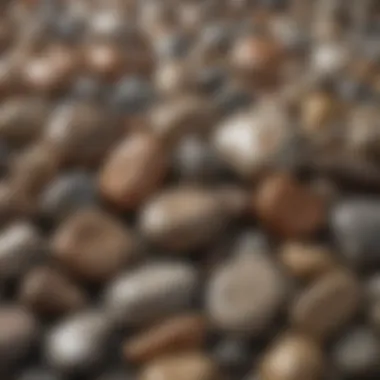

Wire saw machines offer a unique method for cutting rocks, utilizing a thin wire that is often coated with diamond segments. This technology allows for a variety of cutting styles, and its flexibility makes it suitable for both complex geometries and large blocks of material.
One significant advantage of wire saws is their ability to minimize material loss. This is especially beneficial when working with high-value rocks, where even the smallest loss can impact the final product's value. Additionally, the following points highlight their advantages:
- Versatility: Wire saws can easily adjust to different thicknesses and shapes of rock, making them useful for diverse applications.
- Reduced Waste: The fine width of the wire leads to less rock removed during the cutting process.
- Cool Operation: Wire saws generally run cooler than other saw types, which can be beneficial in preserving the quality of the rock.
Despite these advantages, wire saws require specialized training and knowledge to operate effectively. Understanding the mechanics and best practices is vital for harnessing their full potential.
Water Jet Cutters
Water jet cutters utilize a high-pressure jet of water, sometimes mixed with abrasive materials, to cut through various substances. This method is particularly advantageous when it comes to preserving the natural structure of the rock.
The emergence of water jet technology has opened doors for collectors, allowing them to explore creative design possibilities without concerns about damaging delicate specimens. Here are several advantages of water jet cutters:
- Precision and Clean Cuts: The high-pressure nature of the water jet results in clean edges and minimal chipping.
- Non-thermal Process: Since there’s no heat generated during cutting, it prevents thermal distortion in the rock.
- Environmentally Friendly: Water jet cutting is clean and generates no toxic waste, aligning with eco-friendly practices favored by many in the field.
Even so, users should be aware of the cost of operation and setup, which can be higher due the equipment and initial preparations.
"Understanding the strengths of each type of rock cutting machine can make a world of difference in honing skills and improving the final product’s quality."
In summary, recognizing the variability in rock cutting machines—from diamond blade saws providing speedy cuts, to wire saws minimizing waste, and water jet cutters ensuring clean edges—arms collectors and enthusiasts with the knowledge to choose the right tools for their specific needs. Each machine plays a crucial role in the crafting and refinement process, contributing significantly to the beauty and value of the final specimens.
Polishing Machines Overview
Polishing machines play an intricate role in the world of rock cutting and polishing, offering both functionality and precision in enhancing the natural beauty of stones and minerals. Unlike cutting machines that focus primarily on shaping materials, polishing machines bring out the luster and detail hidden beneath rough surfaces. Their significance extends beyond aesthetics; they are vital in preserving the intrinsic value of specimens, especially for collectors and hobbyists alike. When properly selected and operated, these machines can dramatically improve the quality of finished products, transforming ordinary rocks into smooth, shiny gems.
Rotary Tumblers
Rotary tumblers are perhaps the most common polishing machines used in the hobbyist community. They operate by placing rough rocks, grit, and water inside a rotating barrel. The motion causes friction, which leads to the gradual smoothing of the rock surfaces. One key aspect to remember here is the duration of tumbling.
A few points to consider about rotary tumblers include:
- Processing Time: Typically, it takes several weeks to achieve desired results, requiring patience but rewarding the effort with beautifully polished stones.
- Grit Selection: Start with a coarse grit to smooth out the rocks followed by progressively finer grits. This multi-step process ensures that scratches from earlier grits do not remain.
- Capacity: Choose a tumbler that matches your workload; small barrels are ideal for hobbyists while larger ones suit commercial use.
Incorporating rotary tumblers into one’s toolkit can deliver a delightful satisfaction as one witnesses the transformation of rough stones into polished treasures.
Flat Lap Machines
Flat lap machines are ideal for those who take their crafting seriously. Unlike rotary tumblers, which tumble stones around, flat laps use a flat disc to polish the surface. The stone is held against a rotating disc covered in abrasive material. This method allows for precision and control, making it suitable for creating intricate shapes or cabochons.
Important considerations with flat lap machines include:
- Speed Variation: Being able to adjust the speed increases versatility, allowing for different techniques that can be tailored to specific types of stones.
- Disc Selection: Various discs offer different results, with diamond pads being popular for their efficiency and longevity.
- Dust Management: As they create dust during the polishing process, it may be necessary to employ safety measures like masks or a dedicated workspace.
Employing a flat lap machine often appeals to those wanting a hands-on approach in their crafting, especially when detailing various aspects of gemstones.
Cabochon Makers
Cabochon makers take the art of stone polishing a step further. These machines enable users to create uniquely shaped stones known as cabochons, which are often used in jewelry making. The cabochon cutting process takes meticulous attention to detail and specific techniques that ensure the end product is visually stunning.
Key factors to consider when working with cabochon makers include:
- Shape and Size Options: Cabochon makers provide templates or guides for different shapes, optimizing the creation process.
- Material Compatibility: Certain machines may be tailored for specific materials; understanding the characteristics of various stones is crucial.
- Finishing Options: The final polish is important as it can influence the overall value of the cabochon.
A cabochon maker can be seen as an investment. For anyone serious about shaping and polishing stones, it allows for creative freedom and a personal touch to each piece created.
Polishing machines, while distinct in operation, collectively cater to a variety of needs. Their ability to enhance both aesthetics and value shows the importance of these tools in the journey of rock and mineral collection.
How Machines Operate
Understanding how rock cutting and polishing machines operate is vital to grasping their role in both the geological community and the collectibles market. The operation of these machines is not just a matter of routine; it’s about precision, functionality, and adapting technology to meet specific demands.
Mechanism of Cutting
Rock cutting machines employ various mechanisms to slice through hard materials. At their core, these machines use blades, wheels, or wires embedded with diamonds or other hard materials. Imagine a cake being sliced with a sharp knife; that’s similar to how these machines work, except they tackle stones that are many times tougher.
- Diamond Blade Saws: They operate using a rotating diamond-coated blade that not only cuts but also removes material efficiently.
- Wire Saw Machines: These machines utilize a thin wire with diamond segments, cut through hard rock with precision, much like a finely-tuned violin string slicing through the air.
Understanding these mechanisms allows enthusiasts to choose the right machine for their cutting needs, balancing efficiency with the desired finish. Each machine type has its own set of pros and cons, impacting factors like speed and cost.
Polishing Techniques Explained
Once the cutting process is complete, the next step is polishing. Polishing machines vary greatly, each employing specific techniques to achieve a smooth, lustrous surface on rock specimens.
- Rotary Tumblers: These rely on a tumbling action, where rocks and polishing agents are swirled together in a barrel. This method is akin to making a fine wine where the right conditions lead to the best outcome.
- Flat Lap Machines: With flat laps, stones are placed on a flat surface where they are polished through friction against increasingly finer grits. This technique is similar to sanding down wood until it’s perfectly smooth.
- Cabochon Makers: These machines can shape and polish stones into cabochons, which are polished gems typically used in jewelry. The precision required in this process is crucial, as even a slight miscalculation can lead to a less than desirable final product.
By knowing these techniques, collectors can better appreciate the artistry that goes into enhancing their specimens.
Automation and Technology
Advancements in technology continue to revolutionize the way machines operate. Today, many cutting and polishing machines incorporate automation, streamlining operations and improving consistency. Imagine programming a coffee maker to brew just the right cup; similar technology now exists in the stone industry.
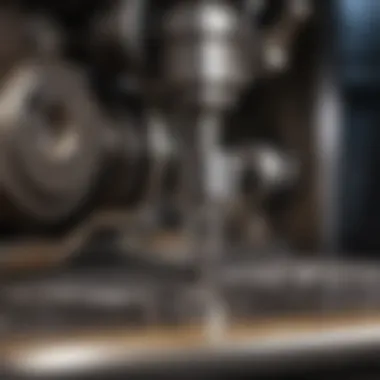
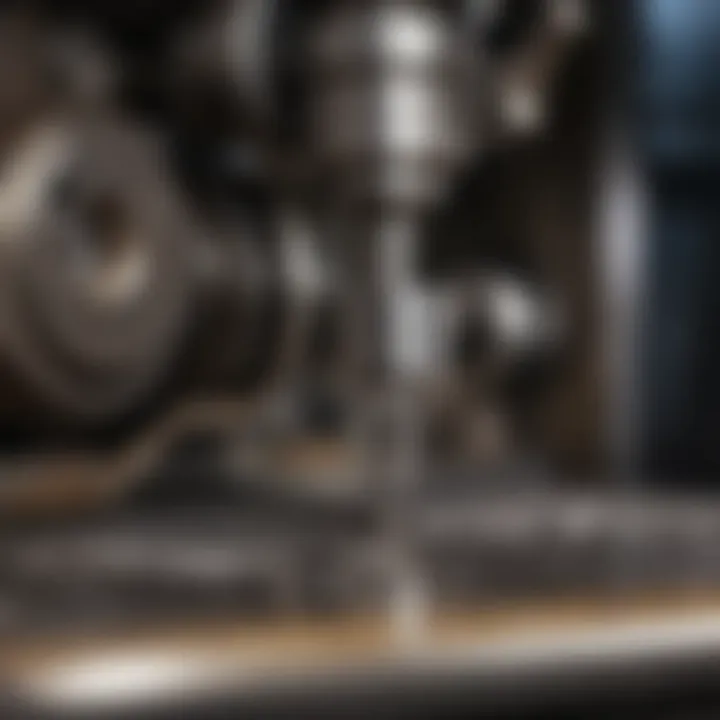
- Computer Numeric Control (CNC): These machines allow for precise cuts that were previously unimaginable. CNC technology translates design files into machine instructions, enabling any novice to achieve professional results.
- Smart Technologies: Emerging smart technologies are also making waves. These include sensors that monitor the machine’s performance in real time, ensuring that everything is running smoothly, much like the way a pilot relies on instruments in the cockpit.
Choice of Material
Choosing the right materials for rock cutting and polishing machines is more than a mere footnote in the operational guide; it’s the very foundation of effective performance. The components selected can significantly influence the precision, durability, and results of the work performed. Like choosing the right tool for a carpenter, the cutting and polishing machinery needs to have the appropriate disks, blades, and materials that align with the tasks at hand.
Materials dictate how smoothly the cutting or polishing occurs and can affect the aesthetics of the final product. Each rock type holds its own unique properties, influencing how it reacts during processing. %A slight oversight in material choice could lead to disastrous outcomes: wasted time, money, and, most importantly, flawed artifacts. In our age where time is gold, selecting appropriate materials is a critical step that cannot be brushed under the rug.
Selecting Disks and Blades
Selecting the right disks and blades for cutting machines is akin to picking a sharp knife for the kitchen; if it’s not right, the job can go sideways quickly. The most common cutting tools for rock processing include diamond blades, which are renowned for their hardness and cutting efficiency. They slice through tougher materials with the grace of a hot knife through butter, providing a fine finish without leaving room for unpleasant chats about chips or cracks.
Moreover, it's worth noting that different rocks require different types of blades—granite can be tough to handle, necessitating blades specifically designed for its density. Likewise, softer stones like alabaster may require a completely different approach with less aggressive blades to avoid excessive wear and tear.
- Diamond Blades: Excellent for various types of rock, offering longevity and sharpness.
- Carbide Blades: Suitable for softer rocks like limestone; less expensive but may wear out quickly.
- Sapphire Blades: Mostly for very specific applications, including crafting delicate pieces.
When it comes to the matter of selecting which blade will do the job best, a bit of research is beneficial. As the saying goes, “an ounce of prevention is worth a pound of cure.” Knowing your materials and their compatibilities with various blades can save a world of trouble down the line.
Compatible Materials for Cutting
In the landscape of rock processing, not every material plays nice with each other. Knowing what rocks are compatible for cutting will help avoid pitfalls. Harder materials tend to require tools made with more durable substances—think diamond or metal matrix tools for those tougher jobs.
Here’s a rundown of popular rocks commonly encountered by both hobbyists and professionals:
- Granite: A dream for those cutting competitions; requires high-quality diamond blades.
- Marble: A bit more forgiving, but means one should still choose blades that won’t abrade too quickly.
- Limestone: Soft, but messy when cutting; use carbide blades for a more effective approach.
- Soapstone: Gentle on cutting equipment, means less wear on blades but prone to scratching during polishing phase.
"The right tools don't just make the work easier; they help in attaining high-quality results that resonate with the very essence of the rock’s beauty."
In every cutting endeavor, understanding the compatibility of materials not only enhances the process but also reflects the quality benchmark of the end products. When collectors and enthusiasts work with the right combinations, they don't just cut— they create. It’s about melding artistry with machinery, forming a duet that sings the praises of natural beauty. Through careful selection, the potential for magnificent results is transformed from a mere possibility into a promise.
Operational Best Practices
When dealing with rock cutting and polishing machines, understanding operational best practices is not merely advisable but essential for anyone working with these tools. These practices ensure safety, enhance efficiency, and prolong the lifespan of the machines, ultimately leading to better results in rock processing.
Safety Considerations
Safety should always be the first thought on a machine operator’s mind. Rock cutting and polishing machines involve various risks that range from minor injuries to severe accidents if mishandled. Here are key safety considerations:
- Personal Protective Equipment (PPE): Wearing appropriate PPE is non-negotiable. At a minimum, this includes goggles, gloves, and ear protection. These items can safeguard against flying debris, loud noises, and sharp tools.
- Regular Equipment Checks: Before starting a cutting or polishing task, inspect the machine. Look for any signs of wear and tear—this includes checking blades, cords, and water supply systems. Regular maintenance can prevent equipment malfunction and resultant injuries.
- Workspace Organization: Maintain a clean and organized workspace. Clutter can lead to accidents, so having a designated area for tools and materials can make a significant difference.
- Emergency Procedures: Make sure to familiarize yourself with emergency shutoff locations and procedures. Knowing how to quickly respond in an emergency can save lives.
"Prior preparation prevents poor performance" – a saying that rings particularly true in the menagerie of rock cutting.
Effective Operating Procedures
Effective operating procedures help streamline tasks and improve the overall quality of rock processing. Delving into these procedures can vastly enhance the functionality of rock cutting and polishing machines:
- Reading the Manual: It's astonishing how many users overlook this simple step. The manuals contain critical information tailored for specific machines, detailing best settings and operation modes.
- Consistent Training: Regular training sessions for operators can create a culture of safety. Sometimes, sharing experiences about mishaps can prevent future occurrences.
- Progressive Adjustments: Start with lower speeds and gradually increase as you become more comfortable with the machine's behavior. Each stone behaves differently; hence finding the right cutting speed and pressure is fundamental.
- Lubrication and Cooling: Properly lubricate the tools and ensure that cooling systems function, especially in extreme conditions. Apprising operators on these minor operations can prolong machine life significantly.
- Documentation and Review: Keeping track of methods and results can lead to continuous improvement. Take note of what works well and what doesn't, then adjust the approach accordingly.
By adopting these operational best practices, users not only bolster their own safety but also elevate the standard of their rock processing work, making it more efficient and effective. The holistic approach encompasses thorough knowledge, meticulous planning, and strict adherence to safety and operational norms.
Maintenance Strategies
In any field dealing with machinery, maintaining equipment is key, and rock cutting and polishing machines are no exception. Without proper care, even the most advanced machines can run into troubles that lead to costly repairs or even replacements. Regular maintenance not only extends the lifespan of the machines but also ensures they operate at their maximum efficiency, producing high-quality finishes on rocks and minerals. For collectors and enthusiasts, this means consistently beautiful specimens that attract the eye and the pocket.
When it comes to maintenance, it’s not merely a checklist to tick off. It involves understanding how each component works, recognizing the signs of wear and tear, and having knowledge about routine upkeep. Following are some crucial elements tied to maintenance strategies:
- Longevity: Just like any tool, frequent use and lack of attention can lead systems to crumble. Regular check-ups can help catch issues early, preventing bigger problems down the road.
- Performance: Well-maintained machines perform better and deliver better results. Dull and unkempt tools are bound to underperform, impacting the quality of the finished product.
- Safety: Machines not kept up-to-date can be hazardous. A failing component could lead to accidents, putting users at risk. Ensuring equipment is in good working order mitigates these dangers.
- Cost Efficiency: Investing time and resources into maintenance can save you money in the long run. Repairing a small issue is far less costly than replacing an entire unit.
"A stitch in time saves nine." This saying rings especially true in the world of machinery upkeep.
Routine Maintenance Tasks
Routine maintenance tasks vary from machine to machine, but there are some universal practices that can be applied broadly:
- Regular Inspection: Set aside time each week to inspect blades, belts, and motors for signs of wear. Look for cracks, uneven surfaces, or loose screws.
- Cleaning: After each use, clean off any dust or debris. Dust buildup can affect motor function and overall efficiency. A simple brush can go a long way.
- Lubrication: Machinery with moving parts needs lubrication. Depending on the model, this may involve oils or greases. Ensure you adhere to manufacturer recommendations.
- Calibration: Periodically recalibrate the machines to ensure that settings are accurate. Off-calibrations can lead to uneven cuts and poor polishing results.
- Documenting Usage: Keeping records of operation hours helps in understanding wear patterns. This knowledge can aid in predicting when parts may need replacing.
Troubleshooting Common Issues
Even well-maintained machines can act up from time to time. Below are common problems you may face with some potential solutions:
- Overheating: If your machine frequently overheats, it may indicate a lack of lubrication or dust buildup around the motor. Make sure you’re up to date on cleaning and lubrication schedules.
- Vibration: Excessive vibrations during operation could point to an unbalanced blade or a loose component. Stop the machine and check all connections and fix any imbalances.
- Cuts Becoming Uneven: If your cuts aren't smooth and even, it could be a sign that the blade has dulled. Replace or sharpen the blade as necessary.
- Motor Malfunctions: If the motor is making strange noises or failing to start, check the electrical connections and any circuit breakers. In some cases, the problem may require professional attention.
Keeping these elements in check can make the difference between a seamless experience or a headache-inducing struggle. With the right approach to maintenance, rock cutting and polishing machines can serve collectors well for years to come.
Applications in Various Sectors
The use of rock cutting and polishing machines transcends mere hobbyist endeavors; they permeate various sectors, imparting value and functionality in ways that escalate their importance. Gaining insights into these applications helps to understand how they contribute to society and industries at large. These machines do more than just slice through rocks; they're tools of advancement, bridging the gap between nature's raw beauty and human craftsmanship. Let's delve into two key sectors: geological research and retail and crafting, exploring their distinctive contributions and implications.
Geological Research
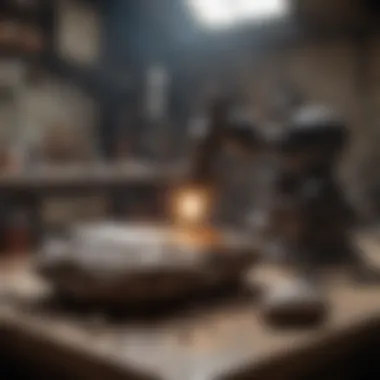
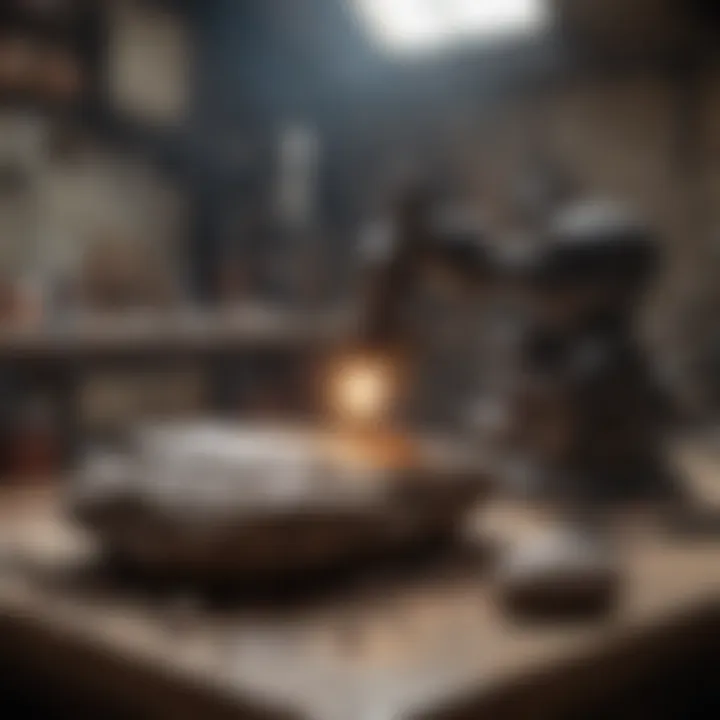
In the realm of geoscience, the role of rock cutting and polishing machines is nothing short of pivotal. Researchers depend on these devices for several reasons. Firstly, precision is crucial when it comes to studying mineral structures and formations. These machines allow scientists to cut samples with exactitude, facilitating the analysis of mineral properties that may otherwise remain hidden behind rough exteriors.
- Facilitating Analysis: By slicing rocks into thin sections, geologists can examine their petrology under microscopes, uncovering valuable data regarding formation processes and properties.
- Field Work Enhancement: Instead of transporting large specimens, cutting machines allow geologists to sample effectively on-site, thus reducing logistical challenges and enhancing fieldwork efficiency.
- Collaboration with Universities: Educational institutions often benefit from the enhanced visual aids that polished specimens provide, enabling clearer discussions and findings in lectures.
The ability to prepare specimens for X-ray diffraction or scanning electron microscopy is essential. The lessons learned through geological research can lead to advancements in resource exploration, environmental studies, and more reliable predictions in natural disaster occurrences.
"A well-prepared geological sample opens doors to understanding Earth's history, thus influencing our future."
Retail and Crafting
Within the retail and crafting sectors, rock cutting and polishing machines serve as the backbone of gemstone adornment and decorative arts. Artisans and retailers utilize these tools to transform raw materials into stunning pieces, whether they're selling jewelry or crafting home decor. Their importance can be dissected into several areas:
- Value Addition: Raw stones hold potential, but it’s the transformation through cutting and polishing that elevates them—creating a marketable product valued for its beauty and craftsmanship.
- Customization: Many artisans are embracing bespoke items, where they can tailor pieces according to client specifications. Machines allow for intricate designs, from cabochons to elaborate sculptures.
- Showcasing Creativity: Given that polished stones shine with such brilliance, they can be used to create stunning displays in shops, attracting customer attention and increasing sales.
The proliferation of these machines among hobbyists and small business owners has spurred a renaissance in local craftsmanship. By facilitating accessibility to high-quality cutting and polishing techniques, these machines enable individuals to bridge the gap between labor and artistry.
In essence, the applications of rock cutting and polishing machines in geological research and retail craftsmanship reflect their invaluable role in shaping not just raw materials, but also the human experience and our connection to the Earth.
Impact on Collectibles and Artifacts
When considering the role of rock cutting and polishing machines, one can’t overlook their profound impact on collectibles and artifacts. These machines transform rough stones and minerals into stunning works of art. Collectors rely heavily on these tools to enhance the visual appeal of their specimens, creating pieces that not only capture the eye but also tell a story of the Earth’s incredible geological history.
Enhancing Aesthetics of Specimens
The aesthetic enhancement provided by cutting and polishing machines is nothing short of remarkable. A raw rock, although fascinating, often does not showcase its true beauty until it undergoes processing.
For instance, a dull piece of agate can be meticulously polished to reveal vibrant layers and intricate patterns that draw the attention of any onlooker.
Using machines such as rotary tumblers, collectors can achieve a smooth finish that brings out the colors and textures buried beneath the rough exterior. Each turn in the tumbler gradually refines the surface, transforming it into a lustrous display piece. This meticulous process not only showcases natural artistry but also elevates the overall appeal of a collector's display.
- Visual Appeal: Polished specimens command a higher visual impact. The light reflects beautifully off smooth surfaces, highlighting unique features.
- Marketability: Well-finished rocks and minerals tend to attract buyers and fetch higher prices at auctions or retail. Collectors see a direct correlation between aesthetics and value.
The art of polishing requires a blend of skill and technology, leading to conversations about the science behind color reflection and mineral composition. Taking time to understand how light interacts with different stones can offer deeper insights into successful polishing techniques.
Regardless of whether it’s quartz or jade, the thrilling glow of a meticulously cut and polished stone carries a narrative of time and transformation.
Value Addition through Processing
Processing, though focused on aesthetics, also significantly contributes to the value of rocks and artifacts. Raw stones are often perceived as having a lower value compared to their finely polished counterparts.
Rock cutting and polishing machines play a crucial role in bridging this gap.
- Quality Enhancements: Tools like diamond blade saws provide precision cuts that preserve the integrity of the material while enhancing its overall appearance. This meticulous attention to detail can greatly increase a stone’s desirability.
- Market Trends: As consumers shift toward appreciating handcrafted items, the demand for polished stones has surged. This has resulted in better pricing for finished products over their raw versions.
- Specialized Market Segments: Certain processing techniques, such as creating cabochons or unique artistic designs, allow collectors to attract niche markets. Each polished piece tells a unique story and holds a distinct value in the eyes of enthusiasts.
"The transformation from rock to a refined specimen not only captures history but also enhances its value and charm."
By investing in quality machines and understanding their mechanics, collectors can turn their passion into a prosperous venture.
Future Trends in Machine Technology
The world of rock cutting and polishing machines is not static; it’s in a constant state of evolution. Staying abreast of future trends in machine technology is pivotal for collectors, hobbyists, and professionals. It’s about more than just the machinery itself; it reflects broader shifts in how we interact with the materials we love and the ways we preserve their beauty.
Technological advancements reconfigure our approach to these crafts, improving precision, efficiency, and safety. For instance, with the rise of eco-friendly practices in various industries, there is a growing demand for machines that reduce wastage and optimize resource use. Collectors, in particular, can benefit greatly from these advancements, as they seek to enhance both the aesthetic quality and the preservation of their specimens without excessive impact on the natural environment.
Moreover, these improvements allow enthusiasts to produce works that were previously complex and time-consuming. Investing in new technology can also lead to increased value in one’s collection or business, as those who utilize the latest tools often see superior results.
Innovations on the Horizon
The next wave of innovations is expected to fuse traditional craftsmanship with cutting-edge technology. Here are a few noteworthy developments we might see:
- Enhanced Cutting Tools: Expectations revolve around cutting tools engineered with advanced materials, such as graphene-infused blades, which will not only increase durability but also improve cutting precision.
- Artificial Intelligence Integration: Machines that utilize AI can adapt their cutting and polishing techniques based on the type of material being processed. This personalized approach can lead to better outcomes, matching the needs of various rock types.
- 3D Printing Synergies: As 3D printing technologies advance, they may combine with cutting machines to create customized tools or components on-demand, tailoring specially to the user’s preferences.
These innovations promise to revolutionize the crafting of specimens, allowing for increased creativity and enhanced results.
Integrating Smart Technologies
The integration of smart technologies into rock cutting and polishing machinery cannot be overlooked. As machines get smarter, they create opportunities for users to experience their craft in new and exciting ways. Some of the considerations include:
- Monitoring Systems: Smart machines often come equipped with monitoring systems that track tool wear, ensuring timely maintenance and reducing downtime.
- Data Analytics: With built-in capabilities to analyze performance, users can gather insights into their operations, leading to better decision-making for future projects.
- Remote Operation: Emerging technologies allow machines to be operated remotely through smart devices. This means users can manage their work when they’re on the go, adding a layer of convenience that matches today’s fast-paced lifestyle.
Incorporating such advancements not only streamlines the technical processes but also enhances user experience, making the craft accessible and more enjoyable.
“Machines are not just tools; they are the foundation upon which artistry and science converge in the rock cutting and polishing realm.”
Each leap in technology potentially opens doors to new techniques and ideas, ensuring that the world of rock collecting remains vibrant and full of potential.
Epilogue
As we wrap up this exploration, it’s important to spotlight the intrinsic value of rock cutting and polishing machines within the geological and collecting communities. These machines reveal the hidden beauty of rocks and minerals, showing what lies beneath their rough exteriors. Without the precision and capabilities of these tools, many specimens that collectors cherish would remain unappreciated in their natural state.
Reflecting on the Role of Technology
Technology plays a significant role in enhancing the functionality and efficiency of rock cutting and polishing machines. Over the years, advancements in materials and techniques have led to the development of tools that not only provide a superior finish but also emphasize safety and ease of use. For instance, diamond blade saws and water jet cutters have become staples in the industry, offering unparalleled cutting precision.
Moreover, automation in the processes has made it possible to achieve consistent results with a fraction of the manual effort required in the past. This shift not only saves time but also allows hobbyists and professionals alike to focus on the creative aspects of their work rather than getting bogged down by the mechanics of cutting and polishing.
Technology also opens avenues for new applications and innovative approaches to rockworking. Smart technologies are being integrated into these machines, offering real-time monitoring and adjustments based on materials being processed. This brings an added layer of sophistication to the craft, ensuring that enthusiasts can tackle a diverse range of projects with confidence and skill.
Ultimately, the effectiveness of these machines hinges on their technological foundation, which continuously evolves to meet the growing demands of the market.
Encouraging Continued Exploration and Learning
One of the most rewarding aspects of working with rock cutting and polishing machines is the endless opportunity for exploration and learning. For both seasoned collectors and novices, understanding the ins and outs of these tools can significantly enhance the overall experience. From knowing how to select the right blades for the job to mastering various polishing techniques, the journey to honing one’s skills is both fulfilling and beneficial.
Collectors should consider engaging with community forums such as reddit.com or participating in local workshops. These platforms can provide invaluable insights, ranging from first-hand experiences of using different machines to tips on maintenance strategies that ensure longevity and performance.
Additionally, as the field of geology is ever-evolving, staying abreast of new trends and technologies can foster a deeper appreciation for the art of rockworking. Attending trade shows or expos can also expose enthusiasts to innovative tools and methods that can be incorporated into their workflows.