Polishing Stones for Metal: An In-Depth Exploration
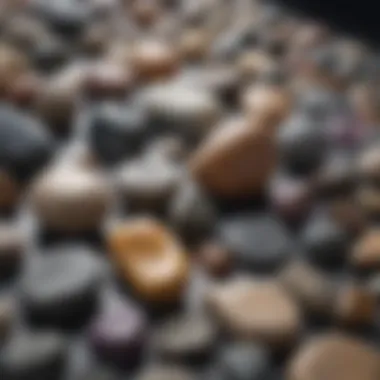
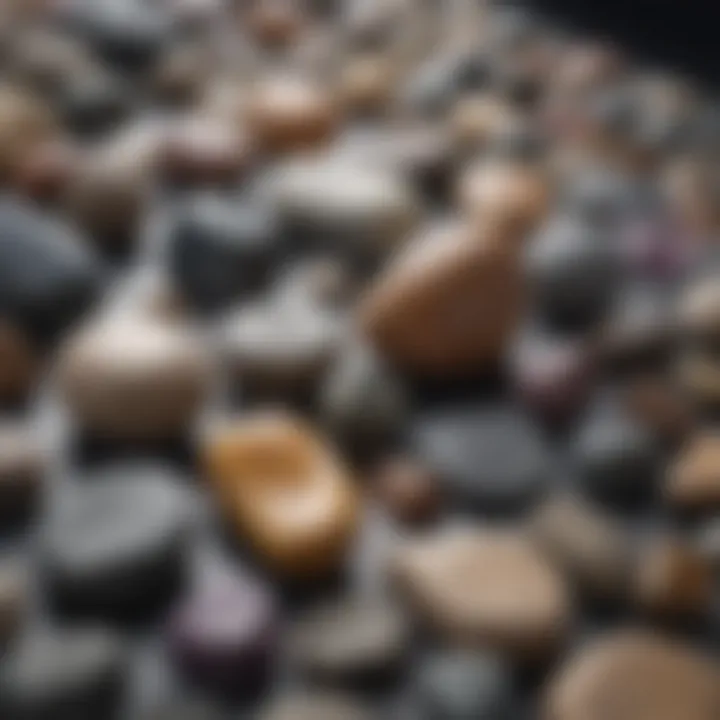
Intro
Polishing stones for metal applications play a significant role in various metalworking processes. They are not merely tools; they are essential instruments that help craft and refine metal surfaces. Metalworkers, collectors, and hobbyists can achieve remarkable results by utilizing appropriate polishing stones tailored for specific tasks. This article unfolds the intricacies of polishing stones, offering insights into their types, uses, and methods that enhance metal finishing.
History and Origins
The use of stones for polishing and finishing metals can be traced back to ancient civilizations. Early metalworkers used naturally occurring stones to buff, refine, and achieve a shine on metal artifacts. This primitive yet effective technique laid the groundwork for modern polishing methods.
Overview of Collectibles, Rocks, and Fossils
In the realm of collectibles, the historical significance of rocks and polishing stones can not be overlooked. They illustrate both the artistic endeavors and technological advancements of past societies. Collectors interested in stones often explore not only mineralogy but also the historical context in which these stones were used.
Historical Significance and Cultural Impact
Throughout history, specific polishing stones have been revered in various cultures for their unique properties. For instance, jade stones found in Asia have been utilized for their resilience and fine finish, making them favored by craftsmen. The cultural narratives tied to these stones reveal much about the societies that valued them.
Identification and Classification
For those delving into polishing stones, understanding their classification is crucial in selecting the right stone for the job.
Guide to Identifying Rocks and Fossils
Identifying polishing stones involves recognizing their physical characteristics. Factors such as hardness, texture, and bonding qualities are pivotal. A basic guide includes:
- Hardness: Ranging from soft to hard stones, which affects the polishing outcome.
- Grain size: Finer grits yield smoother finishes; coarser grits are suitable for shaping.
- Mineral composition: Different minerals interact uniquely with metals during the polishing process.
Common Types and Variations
There are many varieties of polishing stones, each with unique attributes suited for specific metalworking tasks. Common types include:
- Alumina oxide stones: Known for durability and precision polishing.
- Silicon carbide stones: Effective for rough shaping and initial polishing stages.
- Diamond stones: Ideal for achieving finely polished surfaces on hard metals.
Understanding the differences aids metalworkers in not only choosing the right stone but also in maximizing their polishing results.
Polishing stones represent a blend of art and precision, showcasing the craftsmanship that has evolved through time.
Understanding Polishing Stones
In the realm of metalworking, polishing stones serve as essential tools for achieving desired finishes. Understanding polishing stones is crucial for collectors, metalworkers, and hobbyists aiming to enhance their craft. Polishing stones come in various types, compositions, and abrasiveness levels, which directly influence the outcome of metalwork. Each element, from the type of stone to its grit, plays a significant role in shaping the final appearance of a piece. Knowing how to choose and use these stones increases the effectiveness of polishing techniques, ultimately leading to superior results in metal restoration and enhancement.
Definition of Polishing Stones
Polishing stones are abrasive materials designed specifically for refining and finishing metal surfaces. These stones can vary in composition, size, and grit levels, allowing for versatility in achieving different finishes. Polishing stones are not just simple abrasives; they are calibrated tools that help remove scratches, blemishes, and oxide layers from metal. Common types include both natural stones, like Arkansas stones, and synthetic options, such as aluminum oxide stones. Each type of polishing stone has unique properties that make it suitable for specific applications.
Historical Context
The historical significance of polishing stones is noteworthy. Historically, artisans utilized natural stones to polish metals as far back as ancient civilizations. From the Egyptians who polished gold artifacts to blacksmiths in medieval Europe refining their iron tools, the use of polishing stones has undergone both evolution and adaptation. In modern times, innovation in materials and technology has led to the development of synthetic polishing stones, broadening the possibilities for metalwork. This long history reflects the importance of polishing stones in crafting techniques and their enduring role in various trades.
Composition of Polishing Stones
The composition of polishing stones directly affects their performance on metal surfaces. Natural stones typically consist of quartz, garnet, or other minerals, with distinct properties that influence their abrasiveness. Synthetic polishing stones often incorporate materials like silicon carbide and aluminum oxide, optimizing durability and effectiveness. Understanding the composition helps users make informed decisions based on the metal type and surface finish desired. Factors such as hardness, grain size, and porosity contribute to a stone's effectiveness, which is vital in selecting the right tool for specific metal polishing tasks.
"The right composition in polishing stones can make the critical difference between a dull finish and a brilliant shine."
In summary, comprehending the various aspects of polishing stones is vital for those in metalworking and restoration. The properties, history, and definitions provided lay a foundational understanding that will support further exploration in subsequent sections of this article.
Types of Polishing Stones
Understanding the types of polishing stones is essential for anyone involved in metalworking. Each type offers unique benefits and applications, influencing the overall effectiveness of the polishing process. The right choice can lead to superior results, while the wrong choice may result in suboptimal finishes or damage to the metal surface. Thus, a thorough overview of natural and synthetic polishing stones, along with their specific grit and finish types, lays a solid foundation for effective metal polishing.
Natural Polishing Stones
Natural polishing stones come from geological formations and include materials like sandstone, marble, and slate. They are often chosen for their unique characteristics and the range of finishes they can provide. One advantage of natural polishing stones is their environmental friendliness. Those who prioritize eco-friendly practices in their work may prefer these options.
However, it is important to consider factors such as their consistency in performance. Natural stones might vary in quality and effectiveness from one specimen to another. The user should be discerning about the selection. Each type of natural stone requires specific care and handling to achieve the best results.
Examples of natural stone include:
- Alumina-silicate: Ideal for finer polishing tasks.
- Pumice: Effective for both cleaning and polishing.
Natural stones often lead to a distinctive finish that some users find appealing, adding character to the final product. It is crucial, however, to test them on scrap materials to ensure compatibility with the desired metal.
Synthetic Polishing Stones
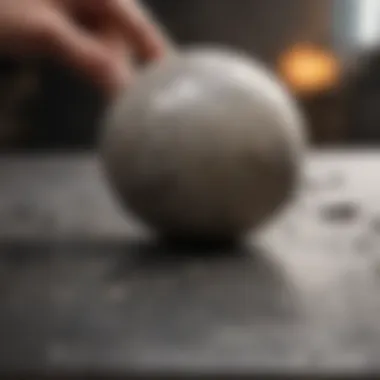
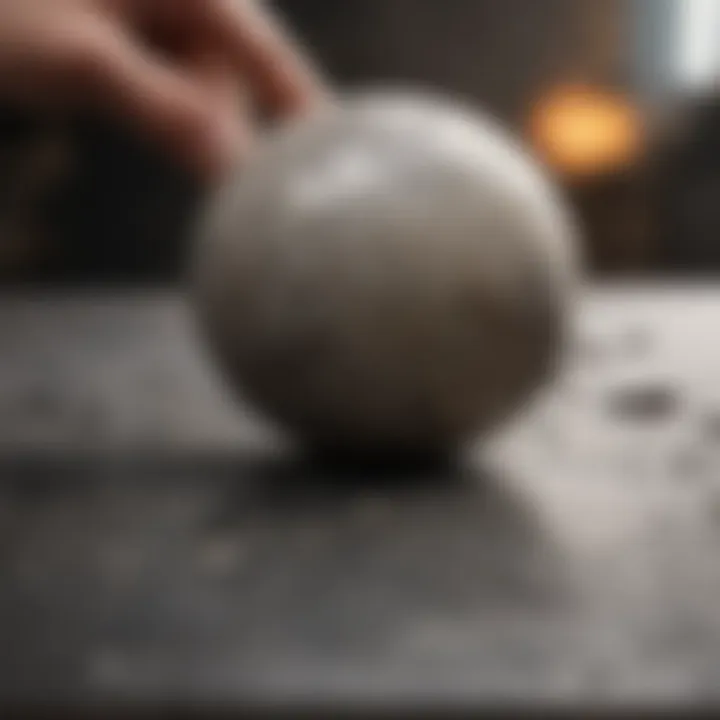
Synthetic polishing stones are engineered materials, created to offer consistent quality and performance. They typically contain a combination of abrasive compounds designed to produce a specific polishing effect. Aluminum oxide and silicon carbide are common abrasives used to manufacture these stones, making them effective for various polishing applications. The uniformity of synthetic stones allows for more controlled polishing processes, reducing the risk of damaging the metal substrate.
These stones also come in various forms, suitable for different tasks:
- Diamond stones: Known for their longevity and effectiveness on hard metals.
- Ceramic stones: Offer a good balance between cut and finish for softer metals.
Synthetic stones can be tailored to meet the specific needs of the user. This flexibility makes them favored among professionals who require predictable outcomes from their polishing work.
Types by Grit and Finish
The grit of a polishing stone plays a pivotal role in achieving the desired finish. Polishing stones are available in different grit levels, ranging from coarse to fine. A lower grit number (e.g., 80-120) indicates a rougher surface, suitable for material removal, while higher grit levels (e.g., 800-2000) are better for achieving high sheen finishes.
- Coarse Grit: Used for initial shaping and significant material removal. It lays the groundwork for finer polishing.
- Medium Grit: Suitable for refining surfaces, minimizing scratches left by coarse stones.
- Fine Grit: Ideal for final polishing stages, creating a desirable luster on the metal surface.
Each type of grit serves a purpose in the overall polishing process. The choice of grit affects not only the surface finish but also the time required for the polishing operation. Understanding these differences is vital for optimizing metal finishing techniques. Seeking the right combination of grit and stone type ensures maximum efficiency and the desired aesthetic appearance.
"The right polishing stone can transform a dull surface into a gleaming finish, making the choice of type and grit essential for professionals in the field."
Applications of Polishing Stones in Metalwork
Polishing stones are invaluable in metalwork, serving various important applications that influence the aesthetic and functional qualities of metals. Understanding these applications allows metalworkers, hobbyists, and collectors to harness the full potential of polishing stones. Use of polishing stones can results in enhanced surface finishes, improved durability, and preservation of historical artifacts. Each application plays a unique role and stems from the underlying properties of the stones used, making it crucial to comprehend their importance.
Metal Finishing Techniques
Polishing stones are central to metal finishing techniques that elevate the surface quality of metals. These techniques not only enhance appearance but also impact functionality. For instance, stones with fine grit create a smoother surface, reducing friction and wear during metal operations. Common techniques include, but are not limited to:
- Buffing with Fine Grit Stones: This method employs soft, fine-grit stones to achieve a high-polished finish.
- Lapping Techniques: Here, polishing stones help in achieving extremely flat surfaces by leveraging their even grit composition.
- Grinding with Coarse Stones: Coarse stones assist in aggressive material removal, perfect for shaping and correcting imperfections.
The skills employed in metal finishing vary depending on the type of stone and desired final result. Each technique is informed by the specific properties of the polishing stone selected.
Restoration of Antique Metals
Restoring antique metals is an art that showcases the capacity of polishing stones to revitalize historical artifacts. The subtlety of restoration requires tools that can remove tarnish, oxidation, and minor scratches without compromising integrity. Recognizing the age and material of each piece is vital in choosing the proper stone. Some valuable stones for restoration include:
- Pumice: Ideal for gentler applications, helps avoid damage while still providing effective cleaning.
- Alumina Stones: These are suitable for finer restoration work, allowing for the careful revival of shine in intricate designs.
Proper techniques in restoration not only conserve the piece but also enhance its historical value. Knowledge of the right stone is crucial, ensuring that antiques retain their original character while benefiting from modern preservation techniques.
Industrial Uses
In industrial applications, the efficiency of polishing stones significantly impacts production quality across various sectors. Industries such as aerospace, automotive, and precision manufacturing rely on the distinct advantages provided by these stones. They enhance various factors important to metalwork:
- Quality Control: The uniform finishes achieved by polishing stones contribute to consistency in manufactured parts, leading to reduced failure rates.
- Cost-Effectiveness: Investing in high-quality polishing stones may seem costly initially, but the longevity and performance reduce the need for frequent replacements.
- Versatility: Different stones are available for various applications, from deburring to final polishing, allowing for flexible adaptation to production needs.
In sum, the applications of polishing stones in metalwork highlight their essential role in delivering superior quality. Correct choice and application lead to enhanced durability, improved aesthetics, and preservation of valuable artifacts.
Methods of Polishing Metal with Stones
Understanding the methods for polishing metal with stones is crucial in achieving desired results in metalworking. This section details the procedures that need to be followed to ensure efficiency and effectiveness in metal polishing. The right methods help in enhancing surface finish and extending the lifespan of both the metal and the polishing stones used.
Preparing the Metal Surface
Preparation of the metal surface is a foundational step in the polishing process. A clean and smooth surface is essential for achieving the best results. Before beginning the polishing, it is necessary to remove any dirt, oil, or rust that may have accumulated over time. This can be done using solvents such as acetone or mineral spirits. Ensure that all residues are removed.
Once the surface is clean, assess its condition. Any scratches or defects should be addressed beforehand, as these can hinder the polishing process. In some cases, sanding with the appropriate grit sandpaper may be required to level out these imperfections. Planning ahead by examining the surface can lead to a more effective polishing outcome.
Selecting the Appropriate Polishing Stone
Choosing the right polishing stone is paramount for effective metal polishing. The selection depends on various factors, including the type of metal being polished and the desired finish. Natural stones, such as emery or Arkansas stones, are favored for their durability and abrasiveness. However, synthetic stones can offer consistent grit sizes and specific properties tailored for certain applications.
It is also vital to consider grit size when selecting a stone. A coarser grit is suitable for heavy material removal, while finer grits help achieve a high-gloss finish. Understanding the specific requirements of the project will guide one in choosing the appropriate stone. Moreover, always ensure the stone is free from damage to avoid contaminating the metal during the polishing process.
Techniques for Effective Polishing
Employing the right techniques enhances the effectiveness of the polishing process. Start by applying moderate pressure while using the chosen polishing stone. The pressure should be adjusted according to the stone and metal type, with lighter pressure typically best for finer finishes.
Moving the stone in varied patterns, such as circular or linear motions, can aid in producing even results. Regularly check the surface for signs of improvement and adjust your technique if necessary. It is important to maintain consistent speed throughout the polishing process, as sudden changes could lead to uneven results.
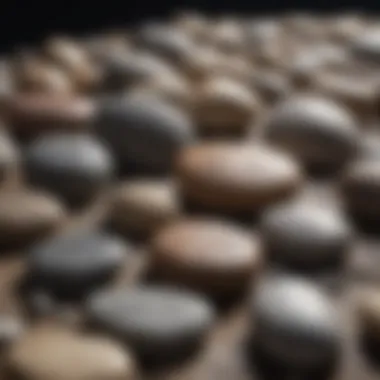
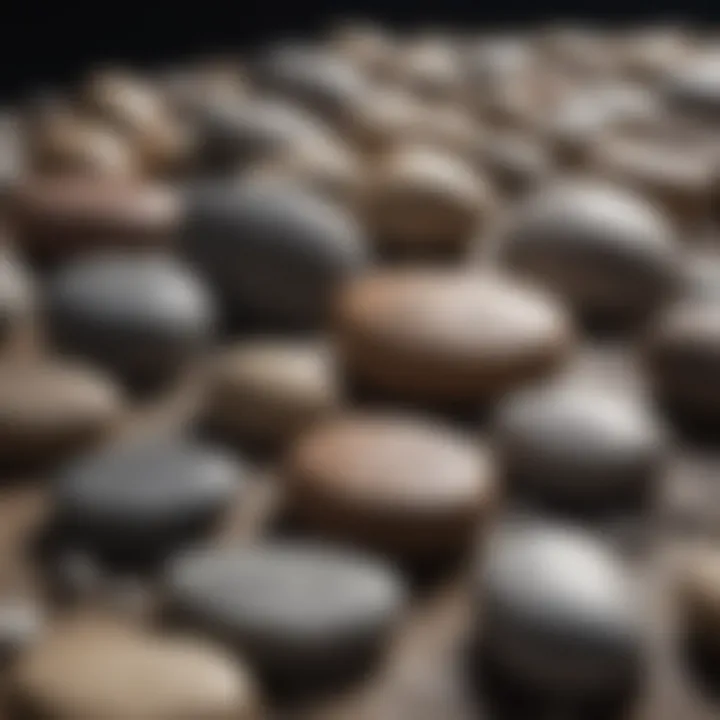
Always remember: Regularly rinsing the polishing stone and metal surface helps minimize debris build-up, allowing for smoother operation.
In summary, mastering the methods of polishing metal with stones involves meticulous preparation of the surface, careful selection of the polishing stone, and refined polishing techniques. Communicating these details fosters understanding and enables enthusiasts to refine their metalwork skills more proficiently.
Factors Affecting Polishing Efficiency
Polishing metals is a nuanced process, influenced strongly by various factors that can affect overall efficiency. These aspects are critical for those engaged in metalwork, whether professionals or hobbyists. Windfall results can stem from understanding how to select and use polishing stones effectively.
Stone Integrity and Quality
The integrity of the polishing stone plays a vital role in the efficiency of the polishing process. A high-quality stone delivers consistent results, ensuring that the metal surface is treated uniformly. Quality can refer to the stone's durability, structure, and uniformity in texture. For instance, a stone with an uneven surface can create scratches or inconsistent finishes on metals, which ultimately requires additional time and effort to correct.
When examining the integrity of polishing stones, consider the following factors:
- Material Type: Natural stones like Arkansas stones tend to have unique properties that may differ from synthetic options such as aluminum oxide. Each type contributes differently to the polishing process.
- Grain Structure: Finer grits produce a smoother finish, while coarser grits are useful for initial shaping. Selecting the right grit is essential for achieving desired outcomes without added labor.
- Durability: The lifespan of a stone depends on the material and the frequency of use. Regularly inspect stones for chips, cracks, or wear, as these could lead to decreased effectiveness.
Investing in quality polishing stones can minimize the need for replacements and enhance your polishing efficiency in the long run.
Moisture and Lubrication Considerations
Another crucial factor in polishing efficiency is the presence of moisture and lubrication. When polishing metals, lubrication can serve multiple purposes, such as reducing friction and preventing heat buildup. The type of lubrication used can vary based on the specific polishing stone and metal involved.
Key points to remember include:
- Type of Lubricant: Different metals and stones may require specific lubricants. For example, water might be effective for softer metals, while oil can work best for harder materials to maintain a consistent glide during polishing.
- Moisture Control: Insufficient lubrication can lead to increased friction, causing the polishing stone to wear faster. This results in uneven surfaces and can even damage the metal being polished.
- Application of Lubrication: Apply lubricant evenly over the stone before beginning the process. Regularly adding lubricant as needed ensures that the polishing surface remains efficient.
Incorporating proper moisture and lubrication practices is crucial for maintaining polishing efficiency. Without these considerations, even the best stones may fall short of delivering optimal outcomes.
"Understanding the mechanics behind polishing is vital for achieving professional-grade finishes in metalwork."
Together, these factors – stone integrity and quality, alongside moisture and lubrication – shape the effectiveness of polishing operations. Adequate attention to these elements not only maximizes efficiency but also results in superior polished finishes that reflect meticulous care and skill.
Safety Measures During Polishing
Polishing metal is a meticulous process that requires precision and skill. However, during this procedure, one must prioritize safety to prevent accidents and injuries. Employing proper safety measures is critical for protecting oneself and maintaining an efficient work environment. This section outlines essential safety protocols and equipment that should be considered during metal polishing.
Personal Protective Equipment
Personal protective equipment (PPE) acts as the first line of defense against potential hazards. When polishing metal, the metallic dust and debris generated can pose serious health risks. Common types of PPE that should be utilized include:
- Safety glasses: Protect eyes from flying particles.
- Respirators: Prevent inhalation of harmful dust and fumes.
- Hearing protection: If using power tools, it is important to protect against high noise levels.
- Gloves: Durable gloves can safeguard hands from sharp edges or hot surfaces while polishing.
Using PPE is not merely a recommendation; it is necessary to ensure long-term safety and health for anyone involved in metalworking.
Workplace Safety Protocols
In addition to wearing appropriate PPE, adhering to workplace safety protocols is vital for creating a secure environment while polishing metal. These guidelines can significantly reduce the risk of accidents. Important protocols include:
- Adequate ventilation: Ensure that the workspace is well-ventilated to avoid the accumulation of harmful dust and fumes.
- Proper tool maintenance: Regularly inspect and maintain polishing equipment to prevent malfunctions that can lead to injuries.
- Clear workspace: Keep the work area organized. Remove unnecessary items to avoid tripping hazards.
- Emergency procedures: Familiarize yourself and others with emergency procedures, including the location of first aid kits and emergency exits.
Implementing safety measures in the polishing process not only enhances productivity but also safeguards the well-being of the user.
Overall, a combination of personal protective equipment and strict workplace protocols creates an environment that promotes safety. By being proactive about safety measures, metalworkers can focus on their craft while minimizing risks.
Choosing the Right Polishing Stone
Selecting the proper polishing stone is critical for achieving desired results in metalwork. The right stone not only enhances the surface quality but also prolongs the life of your tools and materials. With various options available, each brings unique characteristics, which contribute to the efficiency and effectiveness of the polishing process. Understanding these nuances is essential for collectors and hobbyists aiming for precision in their metal projects.
Key Considerations
When deciding on a polishing stone, several key considerations come into play. The first aspect to consider is the type of metal being polished. Different metals have distinct properties that can affect how they respond to polishing. For instance, softer metals like aluminum require softer polishing stones, whereas harder materials like stainless steel might need more robust options.
Another consideration is the grit of the stone. Grit levels determine the fineness of the polishing process. A coarser grit will remove material more quickly, making it suitable for rough shaping, while a finer grit is best for achieving a smooth, glossy finish. It is also important to evaluate the bond type of the polishing stone. Some stones have harder bonds, providing durability, while others are designed for enhanced flexibility.
Finally, the specific application should guide your choice. For example, if you are restoring an antique piece, you may want a gentler stone that prevents damage to the original metal. On the other hand, for industrial applications, a more aggressive stone may be appropriate to expedite the process.
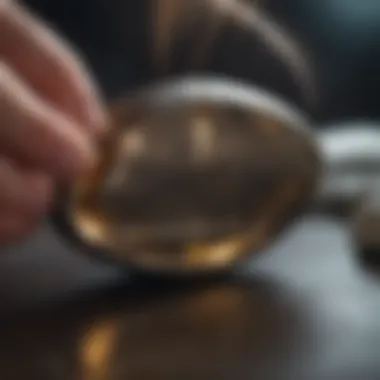
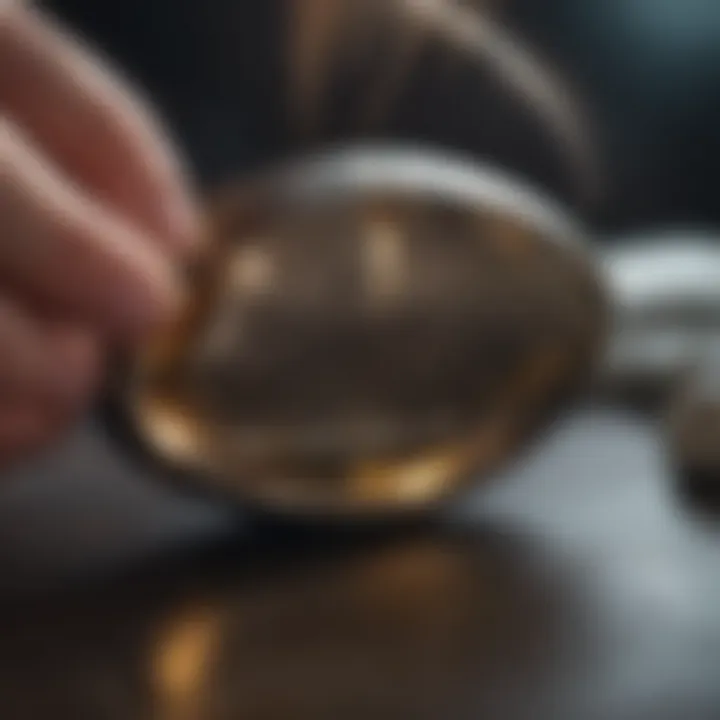
Evaluating Stone Properties
Evaluating the properties of a polishing stone is essential before making a purchase. Various characteristics should be assessed:
- Composition: Different materials are used in polishing stones, including aluminum oxide, silicon carbide, and diamond. Knowing the composition helps determine the stone's suitability for your specific polishing needs.
- Grit Size: Evaluate the grit size according to the desired finish. Grit size is commonly categorized into coarse, medium, and fine. The right choice ensures optimal results, whether you aim for smoothing or high shine.
- Bond Strength: The type of bond can greatly affect performance. Harder bonds have advantages in durability while softer bonds can deliver better finishes.
- Shape and Size: The physical shape of the stone may determine accessibility to different areas of the metal. Specific shapes like tapered ends can be more effective for intricate designs.
When choosing a polishing stone, understanding these properties will direct you to make an informed selection that aligns with your metalworking objectives.
"The efficacy of polishing stones lies in their specific properties; knowing these can greatly enhance your metal polishing endeavors."
Further research and practical experimentation with different stones can bring about nuanced insights tailored to your specific needs, enhancing not only skill sets but also outcomes in metalworks.
Maintaining Polishing Stones
Maintaining polishing stones is critical for ensuring their effectiveness and longevity. Proper care can enhance the performance of these tools, making them more efficient in metalworking applications. When polishing stones are not maintained well, they may lose their cutting and polishing abilities, which can lead to subpar results and potentially damage the metal surfaces being worked on. Therefore, understanding the cleaning, storage practices, and signs of wear is essential for anyone who utilizes these important tools.
Cleaning and Storage Practices
To keep polishing stones in optimal condition, it is vital to adopt proper cleaning and storage methods. After each use, stones should be cleaned thoroughly to remove any metal residue, abrasives, or other contaminants.
- Cleaning Method: Use a soft brush or cloth to gently scrub the stone. For stubborn residues, a solution of water and mild detergent can be utilized. Avoid harsh chemicals that may harm the stone.
- Drying: Once cleaned, allow the stone to dry completely. Storing a wet polishing stone can lead to mold growth or degradation of the material.
Storage is equally important. Polishing stones should be stored in a dry area away from direct sunlight, as UV rays can break down the materials over time. Using protective cases or pouches can also prevent accidental cracks or chips. This careful approach helps maintain the integrity of the stones and ensures they perform at their best for future projects.
Signs of Wear and Replacement
Recognizing when a polishing stone has worn out is essential for maintaining quality metalwork. Over time, continuous use can lead to a reduction in effectiveness. Here are a few key indicators to watch for:
- Surface Appearance: A noticeable change in the surface texture of the polishing stone can signal wear. If the stone appears smooth or glossy, it may no longer be effective at cutting or polishing metals.
- Performance Decline: If you notice that polishing is taking longer or yielding poorer results than before, it might be time to evaluate the condition of your stones.
- Cracks or Chips: While minor chips can sometimes be acceptable, significant cracks may compromise the stone's function. If the stone is damaged, it is advisable to replace it.
Regularly assessing your polishing stones for these signs is crucial to maintaining their performance. Investing in high-quality replacement stones can lead to more effective work and ultimately save time and resources.
Proper care of polishing stones greatly impacts the quality of metalworking outcomes. Taking the time to clean, store, and assess stones will pay dividends in the long run.
Cost Considerations
Understanding the cost implications of polishing stones is essential for anyone engaged in metalwork. Both hobbyists and professionals need to assess not just the price of the stones themselves but also the overall expenditure involved in polishing projects. This section delves into budgeting strategies and how to determine the value of specific polishing stones.
Budgeting for Polishing Projects
When planning a metal polishing project, it is crucial to establish a budget. This budget should cover the purchase of polishing stones, additional equipment, and maintenance supplies. One must consider the following elements:
- Initial Stone Costs: Different polishing stones vary widely in price based on composition and quality. Natural stones may be more expensive but often provide superior results compared to synthetic options.
- Accessories and Tools: Beyond polishing stones, you may need tools such as holders, stands, and even polishing compounds. These can add up, impacting your overall budget.
- Quantity of Stones: Depending on the project scale, you may need multiple stones. Bulk purchasing might save money but evaluate the necessity carefully.
- Project Scale: A small restoration job may not justify high-end stones, whereas large, intricate restorations certainly would.
Effective budgeting involves not just looking at the immediate costs but also evaluating long-term value—picking stones that will last through numerous jobs may lead to cost savings over time, despite higher upfront prices.
Value Assessment of Gold Polishing Stones
Gold polishing stones are a specific niche that merits its assessment regarding value. These stones are often used for delicate finishing tasks, particularly on gold and other precious metals. Here’s how to evaluate the worth of gold polishing stones:
- Material Quality: Genuine gold polishing stones will use actual gold particles in their makeup. This quality directly impacts their effectiveness and longevity.
- Brand Reputation: Established brands often provide better quality guarantees. Researching product reviews and user experiences can inform your buying decisions.
- Performance Attributes: Consider how well a polishing stone performs during use. Factors like grit retention, compatibility with various metals, and ease of cleaning are key.
- Market Availability: The more accessible a specific stone is, the less expensive it may be. However, rare stones can command higher prices due to limited supply.
Assessing the value of gold polishing stones requires a blend of examining their material properties and their practical application in your metalwork. Investing in higher-quality stones can yield better results and save money in the long run by reducing the need for frequent replacements.
"A well-thought-out budget not only preserves financial resources but also aligns project expectations with tangible results."
The End and Future Directions
The exploration of polishing stones for metal marks an essential component of metalwork. In this article, we have examined the various types of polishing stones available, their applications, and the techniques for effective polishing. This section will summarize key takeaways and also consider where the field of polishing technology may be heading.
Summary of Key Takeaways
Polishing stones play a critical role in achieving high-quality finishes on metals. Here are the main points covered:
- Types and Composition: Understanding the differences between natural and synthetic polishing stones is crucial. Materials such as diamond, silicon carbide, and aluminum oxide offer varying levels of grit and efficiency for specific applications.
- Techniques and Safety: Techniques for effective polishing depend on the chosen stone type and the metal surface being polished. Adhering to safety protocols, such as the use of personal protective equipment, is vital in ensuring safety during the polishing process.
- Maintenance and Cost: Regular maintenance and proper storage of polishing stones extend their lifespan. Evaluating costs in relation to project budgets can enhance financial planning for both hobbyists and professional metalworkers.
Vision for Emerging Polishing Technologies
The future of polishing technologies looks promising. Innovations are likely to focus on the following elements:
- Advanced Materials: New materials may emerge to provide superior grit and durability, enhancing polishing effectiveness. Nanotechnology could play a pivotal role in this evolution.
- Eco-Friendly Options: As sustainability becomes a priority, the demand for eco-friendly polishing solutions might increase. This could lead to the development of biodegradable polishing stones that do not compromise performance.
- Smart Technology Integration: Automation and smart technologies may transform traditional polishing techniques. Devices that use artificial intelligence can analyze metal surfaces and provide recommendations for optimal polishing methods.
The landscape of polishing metal is transforming rapidly, unfurling new possibilities for both craftsmanship and technology.