Crafting Your Own Rock Polisher: A DIY Guide
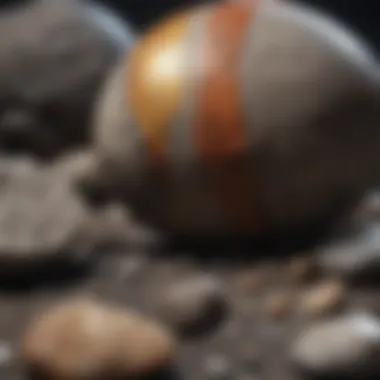
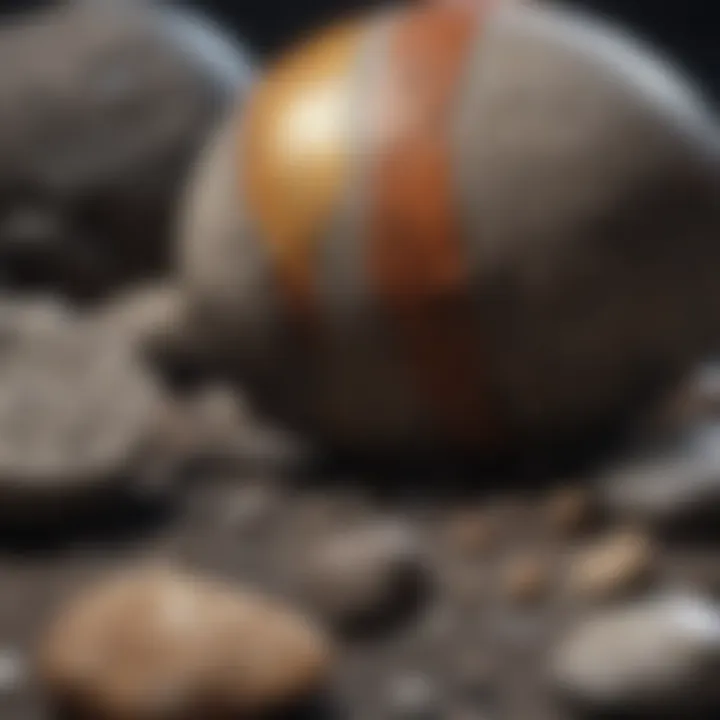
Intro
Crafting your own rock polisher can be a rewarding venture for anyone fascinated by the beauty of rocks and gemstones. For hobbyists and collectors alike, a rock polisher not only enhances the appearance of stones but also allows you to dive deeper into the art and science of rock tumbling. Whether you’re looking to create a beautiful array of polished pebbles or simply wish to understand the polishing process better, both new enthusiasts and seasoned rock hounds can reap countless benefits from building a polisher from scratch.
This guide will serve as your roadmap to understanding the history, essential materials, construction techniques, and critical polishing processes. From the choices that affect your polish's final appearance to the intricate workings of different tumblers, the aim is to equip you with the comprehensive knowledge necessary to jumpstart your rock polishing journey.
History and Origins
Overview of Collectibles, Rocks, and Fossils
Rocks and fossils have captivated humans for centuries. From early civilizations using stones for tools to modern collectors displaying breathtaking specimens, the allure of these natural artifacts transcends time. It’s fascinating to consider how the appreciation of these collectibles has evolved, reflecting trends in art, science, and even folklore.
In various ancient cultures, specific rocks were associated with spiritual significance. For instance, jade was highly valued in ancient China, believed to bring good luck and prosperity. Similarly, fossils have long been a source of intrigue, often seen as remnants of a world long gone. They tell stories of evolution and environmental changes spanning millions of years. It’s this duality of beauty and history that fuels the passion for collecting and polishing them today.
Historical Significance and Cultural Impact
The act of polishing rocks and gemstones has its roots in antiquity. For example, ancient Egyptians highly regarded lapidary arts, creating exquisite pieces of jewelry from polished stones. This tradition carried through history; notable cultures, such as the Romans and the Maya, embraced the crafting of polished stone into ceremonial objects or adornments. The meticulous processes of shaping and polishing required knowledge and expertise that were often passed down through generations.
In modern times, the rise of amateur geology and rock tumbling exploded in popularity during the mid-20th century. Home rock tumblers became increasingly available, allowing anyone with a curious spirit to give this craft a try. It ushered in a new wave of interest, connecting individual collectors and hobbyists through clubs and online forums, such as Reddit.
"Every polished rock has a story to tell, showcasing the beauty of patience and persistence."
Identification and Classification
Guide to Identifying Rocks and Fossils
To craft an effective rock polisher, understanding what you are working with is crucial. Identifying rocks and fossils can be daunting, but with a keen eye and a bit of practice, you can master it. Begin with the basics:
- Color and Texture: The surface characteristics often give away a rock’s identity. Shiny, smooth surfaces indicate polishing potential.
- Hardness: Use the Mohs scale to assess how hard the rock is; this will inform your polishing technique and how long it might take.
- Weight: Heavier rocks like quartz may require different approaches compared to lighter ones like pumice.
Common Types and Variations
When it comes to polishing, different types of rocks present unique challenges and yields. Here are some common types:
- Agate: This colorful, banded stone is quite popular for tumbling and polishing.
- Jasper: Often opaque with vibrant colors, it can show striking patterns when polished.
- Obsidian: A volcanic glass that creates an exquisite shine, but requires careful handling.
- Flint: Known for its toughness, it can be beautifully polished if the right technique is used.
With these insights, you're set to pursue crafting your rock polisher. The subsequent sections will delve into necessary materials, construction methods, and the science behind the polishing process, ensuring you take your first steps with confidence.
Prolusion to Rock Polishing
Rock polishing is not merely an activity; it’s a venture into the realms of nature's artistry and craftsmanship that many enthusiasts find deeply fulfilling. For hobbyists and collectors, understanding the nuances of rock polishing is essential. It is like unlocking a hidden treasure within common stones, turning dull, rough surfaces into reflective, sleek finishes that can catch the light in beautifully intricate ways. But why should one bother with this process?
Importance of Rock Polishing
Polishing rocks serves several critical benefits.
- Enhances Aesthetic Appeal: A polished rock shines and showcases its true colors, often revealing a layer of beauty that can go unnoticed at first glance. This transformation can make a significant difference when it comes to displaying collections or creating art.
- Improves Value: For those who consider rock polishing as part of a business or collection, polished stones generally fetch higher prices than their raw counterparts. It's not uncommon for beautiful specimens, when polished well, to attract the eye of buyers at fairs and galleries.
- Educational Insights: The polishing process allows collectors to better understand the characteristics of various minerals. Observing how different grit levels affect the rock can provide invaluable knowledge about material properties and geology.
- Therapeutic Benefits: There’s also something meditative about polishing rocks. The repetitive act—combined with the anticipation of revealing something new—can provide an outlet for stress relief. It’s about more than just enhancing a rock; it’s a form of mindfulness practice for many.
Historical Context of Rock Tumbling
The art of rock tumbling dates back thousands of years. Archival evidence suggests that ancient civilizations recognized the beauty within stones and utilized rudimentary methods to smooth and polish them.
Many historians credit the first significant use of tumbling techniques to indigenous people who stone tool making. They often observed how vigorous actions could refine the edges of their tools, leading to a more efficient and effective product. Later, in the 20th century, the modern rock tumbling process was refined as machinery became more sophisticated, allowing hobbyists to engage in polishing without the manpower previously needed.
Today, the growth of rock tumbling as a hobby has made it accessible to a larger audience. Whether for personal enjoyment or competitive showcasing, rock enthusiasts relish the opportunity to learn both the craft and the history that accompanies their hobby.>
"Rock polishing is like peeling back the layers of ages. Each turn reveals not just a mirror-like surface but a deeper understanding of the earth beneath our feet."
As the field evolves, knowledge surrounding the materials and techniques continues to expand, keeping the practice both engaging and educational.
Understanding Rock Types
When embarking on the adventure of rock polishing, grasping the differences among various rock types isn’t just helpful; it’s essential. Each rock possesses unique characteristics that significantly impact the polishing process. For example, harder rocks like quartz can achieve a mirror-like finish, whereas softer rocks like limestone might not endure the same level of abrasion. Recognizing these details can save you time and resources, ensuring you select the right materials for your polishing endeavors.
Furthermore, understanding rock types lays the groundwork for future projects and experimentation. You may find that some stones have intriguing color patterns or textures that make them more desirable to polish and display. Equipping yourself with this knowledge creates a richer and more rewarding relaxing experience as you bring out the beauty hidden within each stone.
Common Types of Rocks for Polishing
When it comes to rock polishing, not all stones are created equal. Here are some common types you might encounter:
- Agate: A prized choice for many due to its striking colors and banding. Polishes beautifully under the right conditions, revealing vibrant patterns.
- Jasper: Known for its earthy tones and unique surface designs, jasper can be an excellent option for those looking for a more natural look.
- Quartz: This is a hard and durable stone, perfect for novices aiming for a stunning finish. Clear quartz is especially popular for its clarity and shine.
- Obsidian: A volcanic glass that can deliver an ultra-smooth surface. Due to its sharp edges, handle with caution when polishing.
- Limestone: Softer and easier to polish, limestone can yield a subtle sheen, but be mindful that it may wear away faster than other types.
Exploring these categories helps you figure out the best candidates for polishing, ensuring you obtain the desired results.
Profile of a Polished Rock
A polished rock differs significantly from the raw stone you might first acquire. The transformation is dictated by several key features:
- Luster: A polished rock should exhibit a lustrous sheen. This reflects how smooth the surface has become after going through the grits.
- Color Depth: The polishing process often brings out vivid colors that were invisible in the natural state. Various minerals can contribute to this transformation.
- Texture: The tactile difference can be substantial. A well-polished rock feels smooth and pleasant to the touch, enhancing its visual appeal.
- Hardness: The durability of a polished stone can surprise many. Proper techniques bear a direct relationship to how well a rock withstands wear over time.
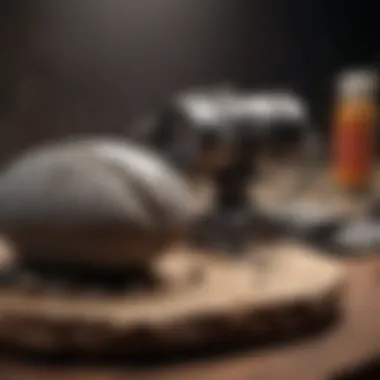
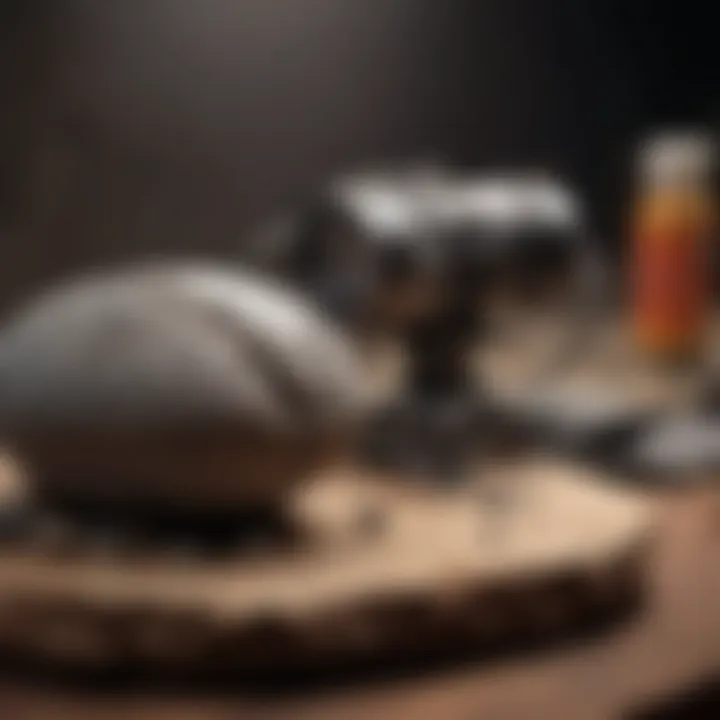
"The art of rock polishing isn’t just about aesthetics; it’s about revealing the story each rock has to tell."
By understanding these aspects, you will appreciate not just the process but also the final result, enhancing your collection with truly remarkable pieces.
Essential Tools and Materials
When embarking on the journey of crafting a rock polisher, understanding the essential tools and materials is like having a sturdy map in hand before venturing into uncharted territory. It's not just about having the right equipment; it’s about enhancing the quality of your work and ensuring efficiency throughout the process. In this section, we’ll delve into the fundamental tools you’ll need, materials required to construct your polisher, and the safety precautions that go hand in hand with this exciting project.
Basic Tool Requirements
The backbone of any successful DIY project rests in the tools you wield. When crafting a rock polisher, your toolbox should be stocked with a few key items:
- Drill: A powerful drill is vital for making precise holes and adjustments in your polisher's assembly.
- Screwdrivers: Both flat-head and Phillips screwdrivers are essential for securing various components.
- Wrenches: Adjustable wrenches or socket sets might come in handy when dealing with nuts and bolts.
- Measuring Tape: Accuracy is key, so a reliable measuring tape ensures that your cuts and placements are spot on.
- Saw: Depending on the materials used, a hacksaw or jigsaw can be used for cutting wood or metal parts.
These tools don’t have to break the bank. A well-rounded mix of basic tools will suffice, allowing you to build with confidence.
Materials for Building a Polisher
Now that you have the tools at your fingertips, it's time to gather the materials necessary for creating your rock polisher. Here’s a closer look at the indispensable components:
- Container Drum: This is where the magic happens. You can repurpose plastic containers or purchase steel ones meant for tumbling.
- Motor: A durable motor, preferably one that operates quietly, will ensure consistent tumbling without a hitch.
- Grit Media: Essential for the polishing process, you’ll need different grades of grit such as coarse, medium, and fine.
- Seals and Bearings: These components will keep the tumbler running smoothly, preventing leaks or wear.
- Vibration Dampening Material: This can be useful to reduce noise and wear on the surfaces of your workspace.
Before you start, make sure to acquire materials that are suitable for your design choice. Different designs might favor specific materials, and this selection can significantly impact the performance of your polisher.
Safety Measures and Precautions
In the excitement of building your own rock polisher, don’t forget the importance of safety.
Safety first! Always wear protective eyewear and gloves when working with tools and materials.
- Eye Protection: It's crucial to safeguard your eyes from flying debris, especially when cutting materials.
- Gloves: Wearing gloves can help protect your hands from sharp edges and hot surfaces.
- Workspace Ventilation: If you're working indoors, ensure that your work area is well-ventilated, especially if your materials release fumes.
- Secure Your Workspace: Make sure your tools and materials are organized to prevent accidents.
- Follow Instructions: When handling machinery and tools, following the manufacturer’s instructions helps mitigate risks.
By incorporating these safety measures, you create a conducive environment for both productivity and creativity in your rock polishing endeavors.
Step-by-Step Construction of a Rock Polisher
Constructing a rock polisher from scratch is a gratifying project that merges practical skills with creativity. Understanding the step-by-step approach is vital because it does not simply involve putting together parts, but also ensures a comprehensive grasp of each component's role and function. This process is about more than just making a tool; it’s about creating an efficient piece of equipment that will serve a purpose over time. A well-thought-out construction can significantly affect the efficiency and results of your rock polishing endeavors, making it essential to tackle each step without haste.
Designing the Structure
When you dive into designing the structure of your rock polisher, it’s best to start with a clear idea. You need to consider the size and shape depending on the types of rocks you plan to polish. A rectangular or cylindrical design may work better depending on the tumbling method you choose. This phase also involves sketching out your design on paper. Think of it like a blueprint where you envision your creation before putting it together.
Important aspects to think about include:
- Material choice: Plywood, PVC pipes, or metal; each has its own merits.
- Size considerations: Bigger isn’t always better; ensure it fits your workspace.
- Portability: If you’ll be moving it around, consider lightweight materials.
Using a sturdy base is crucial to minimize vibrations during operation. This foundational support will bear the load of the tumbler and reduce wear over time.
Assembling the Components
Once the design is in place, it's time to assemble your components. Take your time here, as careful assembly can prevent future problems.
- Gather your tools: You’ll need a drill, screws, a saw, and possibly a welding kit if you're working with metal.
- Follow your blueprint: Cut materials according to your measurements, ensuring accuracy in dimensions.
- Secure the base: Fix your base to a platform with screws and make sure it’s level.
- Attach the tumbler: Depending on whether it’s rotary or vibratory, you'll fix it securely, making sure it aligns perfectly.
- Add any compartments: If you want to customize storage for grits or other materials, this is the time to include them.
While assembling, ensure that each joint is tight and that the tumbler spins freely. You can’t rush this phase; attention to detail pays off.
Testing for Stability and Durability
The final step before calling your polisher complete is testing its stability and durability. This phase will determine how well your polisher holds up during actual use. Run tests at various speeds, monitoring for any vibrations or instability.
- Safety check: Ensure that all components are securely fastened.
- Test run: Do a preliminary test with some less valuable rocks or pebbles to see if it operates smoothly
- Material resilience: Pay attention to the materials used and how they react. If there are cracks or signs of wear, adjustments might be necessary.
"A rock polisher's efficacy is as strong as its weakest component; thus, crafting each section with care is paramount."
If the construction sways or makes unusual noises during operation, re-evaluate the component alignments and stability checks. This stage is crucial as it could prevent larger issues down the line, ensuring your polishing endeavors are both effective and safe.
Polishing Process: A Detailed Guide
The polishing process is the heart of transforming rough stones into captivating gemstones. It’s not just a mundane task; it’s a delicate interplay of science and art. Understanding this phase is crucial for hobbyists and collectors alike because it determines the final look and feel of the polished rocks. With the right approach, the dullest piece of rock can suddenly shimmer, catching the eye and sparking curiosity.
Selecting the Appropriate Grit Sizes
When embarking on the polishing journey, the choice of grit size is paramount. Grit refers to the particles in the polishing media, and they play a vital role in shaping the rock’s surface. A systematic approach to grit selection involves starting with coarse grits and gradually moving to finer ones.
- Coarse Grit (40 to 60 mesh): Ideal for shaping rough stones, these grits will remove imperfections and start to define the rock's initial contours.
- Medium Grit (80 to 220 mesh): This stage refines the shape, smoothing out the scratches left by the coarse stage.
- Fine Grit (400 to 600 mesh): At this point, the surface begins to glow, as finer particles polish it almost to a mirror-like finish.
- Super Fine Grit (1200 mesh and above): This is where the real magic happens; it enhances the shine and brings out colors and patterns in the rock.
Selecting the correct grit size can make or break your polishing efforts, so keep the grit range in mind as you move through the stages.
Stages of Rock Polishing
Rock polishing is not simply about repetitive tumbling; it’s a structured process consisting of distinct phases. Each stage plays a crucial role in achieving that coveted shine:
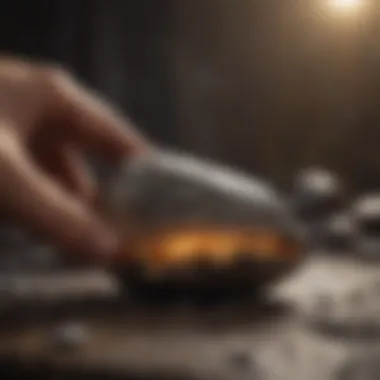
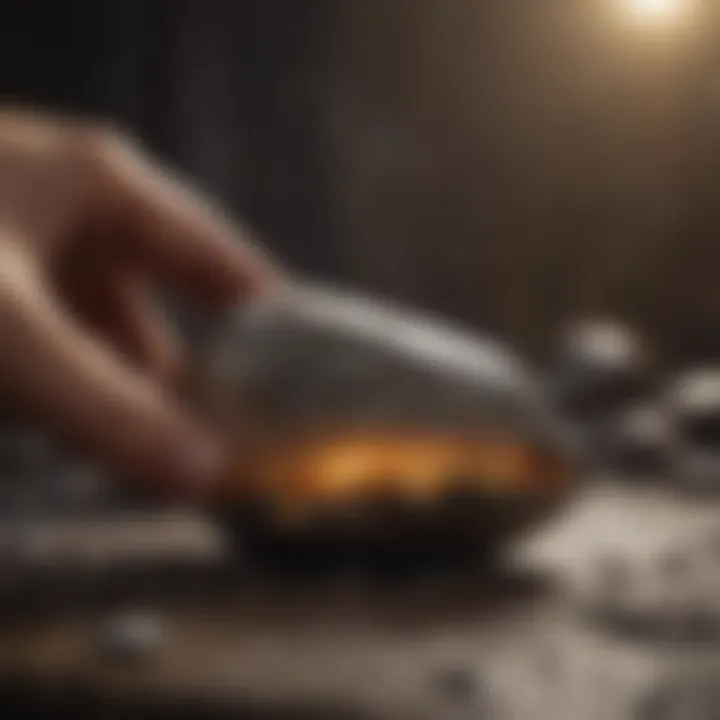
- Shaping and Grinding: As mentioned, the process kicks off with coarse grit to define the shape, effectively generating the rough outline of your stone.
- Pre-Polishing: Transitioning to medium grit, this stage smooths out the surface, prepping it for the final polish.
- Final Polishing: Using fine or super fine grits makes the surface gleam. This stage elevates the texture and clarity, allowing the natural beauty to shine through.
It's worth noting that skipping any of these stages can lead to unsatisfactory results. Rushing through the polishing can result in rough patches or, worse, a dull finish.
Time Management in Polishing
Patience is an invaluable trait for any serious rock polisher. Managing the time spent on each stage is essential to ensure quality results. Here are a few tips to optimize your polishing regimen:
- Don’t Rush: Each stage may vary in duration; however, it’s generally advised that you should let rocks tumble for at least a week per grit size.
- Keep Records: Maintaining a log can help track how long each batch spends in the tumbler. It can also inform future runs by providing insights into what worked best.
- Check Regularly: Regularly inspect your stones to gauge progress. This practice allows you to adjust timing based on actual outcomes—a bit like getting the feel of dough while baking.
Troubleshooting Common Issues
When diving into the world of rock polishing, it’s crucial to anticipate potential hiccups that might pop up along the way. Troubleshooting common issues not only enhances the overall experience but also ensures that you get the most out of your DIY rock polishing ventures. The importance of this topic lies in empowering rock and fossil collectors with the ability to recognize and resolve problems swiftly. Addressing these issues can be the difference between a polished masterpiece and a frustrating mishap.
Identifying Problems during Polishing
As you embark on your polishing journey, it’s essential to keep a keen eye on the process. Issues can arise at any step, whether it's in the initial grinding phase or during the final shine. Here are some common signs that trouble is brewing:
- Uneven Surface: If the stones remain rough or exhibit inconsistent shine, it points to improper grit utilization or uneven processing time.
- Excessive Noise or Vibration: A rock tumbler that rattles or performs loudly might indicate misalignment in the components, which could not only harm the tumbler but also hinder effective polishing.
- Grit Contamination: Using grit that is mixed with previous powders can lead to subpar results. Contamination can be easily overlooked, making it essential to inspect your materials closely.
Recognizing these issues early on can save you a great deal of time and resources. A thoughtful approach ensures that you can pinpoint whether the problem stems from the choice of rocks, the grit being used, or the machine itself.
Solutions to Common Troubles
Once you’ve identified an issue, the next step is addressing it effectively. Here are some tried-and-true solutions that seasoned polishers recommend:
- Adjust Grit Sizes: If uneven surfaces are noticed, consider fine-tuning your grit selection. Perhaps you need to go coarser before moving onto finer grits, or double-check the grit size you’re currently using.
- Check Alignment: If unusual sounds or excessive vibrations occur, stop the tumbler immediately. Ensure that all components are properly aligned. Sometimes, just a simple tightening of screws can do the trick.
- Clean Grit Between Batches: To avoid contamination, clean the barrel thoroughly after each cycle. This might be cumbersome but will pay off with clearer and shinier results.
- Record Observations: Maintain a log of your polishing activities, noting any unusual occurrences or changes. Over time, you’ll develop a better sense of what might need tweaking for optimal performance.
"Troubleshooting isn’t just fixing the problem; it’s about understanding the dynamics of the polishing process.”
In the end, addressing these challenges not only imparts valuable knowledge but also enhances skills that translate into exceptional polishing. The more adept you become at troubleshooting, the more satisfying each polishing journey will be.
Types of Rock Tumblers and Their Applications
Understanding the different types of rock tumblers is crucial for anyone looking to delve into the art of rock polishing. Each tumbler type offers unique features, and knowing how these can affect the polishing process can make a significant difference in the quality of the final product. There are basically two major categories of rock tumblers: rotary and vibratory. By exploring these, you will appreciate the benefits each one brings to your rock polishing journey.
Rotary vs. Vibratory Tumblers
Rotary tumblers tend to be the most classic choice for rock polishing. They work by using a constant rotating motion, allowing rocks and grinding media to tumble against each other. This sustained action is fantastic for creating a smooth finish on rocks, but it does require a longer time commitment for results to shine through. You’ll find rotary tumblers can handle larger batches of rocks, making them ideal for those who are looking to polish many stones at once.
"Patience is a virtue that applies well to rotary tumbling; great results take time to reveal themselves".
On the other hand, vibratory tumblers offer a different approach. They utilize vibrational motion to create a chaotic but controlled environment for the rocks. This method is quicker, often cutting the polishing time significantly compared to rotary tumblers. This can be a huge advantage if you're urgently trying to finish a project. However, the downside might be that vibratory tumblers typically handle smaller batches of stones, limiting the number you can work on at once.
- Rotary Tumblers:
- Vibratory Tumblers:
- Can tumble a greater amount of rocks in one go
- Takes longer to achieve final polish
- Ideal for more extensive polishing jobs
- Faster polishing process
- Generally better for smaller quantities
- In many cases produces impressive results in hours rather than days
Rating Efficiency and Output
The efficiency and output of your tumbler can depend heavily on this choice between rotary and vibratory types. Evaluating both types involves considering factors such as power consumption, time taken, and how effectively the tumbler does its job.
For instance, rotary tumblers tend to consume more power over a longer duration. They excel in polishing larger items but may also lead to higher energy bills if you run them consistently without breaks. On the flip side, vibratory tumblers, despite their smaller output potential, perform efficiently in shorter bursts of time, leading to quicker results without drastically raising your electricity usage.
When determining the best option, think about what you prioritize more: time, quantity, or possibly the type of stones you generally work with. If you often find yourself polishing smaller stones and prefer efficiency, a vibratory tumbler might just be the ticket. However, if you are looking to process larger quantities of raw rocks, a rotary tumbler is a worthy investment.
To sum it up, evaluating both rotary and vibratory tumblers outlines the paths for effective rock polishing based on personal preferences and objectives. Making an informed choice will undoubtedly enhance your rock polishing experience.
Exploring Advanced Techniques
When it comes to perfecting the art of rock polishing, exploring advanced techniques can be a game changer for both novices and seasoned hobbyists. This section is pivotal as it dives into sophisticated methods that can significantly enhance your polishing results. By stepping beyond the basics, you can achieve a level of shine and smoothness that is truly remarkable. This deep dive into advanced techniques allows collectors to differentiate their work and improve efficiency, tapping into the nuances that make each rock unique.
Experimenting with Different Media
Experimenting with different media during the rock polishing process opens up a treasure chest of possibilities. While most enthusiasts might start with common abrasives like silicon carbide, trying out alternative media can yield surprising results. Here are a few options that deserve a mention:
- Aluminum Oxide: Known for its durability, aluminum oxide can help achieve a high polish on harder stones.
- Ceramic Media: This can work wonders when you are dealing with softer rocks, protecting them from scratches while enhancing the smoothness.
- Polishing Powders: Materials like tripoli or rouge can be used in the final stages to give a dazzling finish.
Moreover, you can even combine different media in the same batch. Just imagine combining silicon carbide with a bit of finer diamond dust—your rocks might end up looking so good they could charm the scales off a snake! Experimentation not only spices up your polishing routine but also gives you insight into each stone’s behavior during the process.
Chemical Polishing Agents Overview
Chemical polishing agents provide a more modern approach to the traditional rock polishing methods. These agents can assist in refining the surface more effectively, especially on those stubborn pieces that simply refuse to shine.
A few notable chemical agents to consider:
- Dissolved Zinc Selenide: Great for polishing quartz, offering an unusually bright finish.
- Cerium Oxide: Known as a champion in polishing glass, it also works well with certain gemstones.
- Vinegar Solutions: Amazingly, a simple vinegar solution can help clean and brighten softer rocks without the harsh effects of more abrasive materials.
It's crucial to understand that while chemicals can elevate your polishing game, they require careful handling and proper safety precautions. Knowledge is key to utilizing these agents effectively.
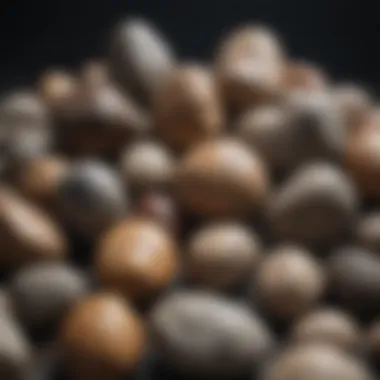
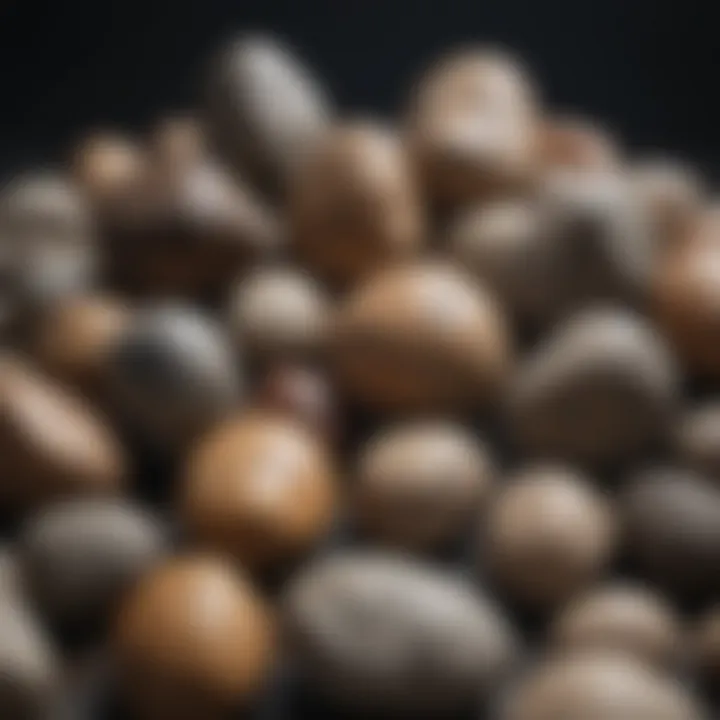
In addition to improving your polish, chemical agents can also reduce the time spent on polishing. However, they require an understanding of how different stones react to chemicals, making this a topic worth learning thoroughly before jumping in.
Combining advanced techniques like experimenting with different media alongside chemical agents can make your rock polishing process not only more effective but also more interesting. You may just surprise yourself with the results you can achieve through these explorations.
Maintaining Your DIY Rock Polisher
It's easy to get lost in the excitement of creating a rock polisher from scratch. After all, every turn of the tumbler unveils the hidden treasures within stones. However, the journey does not end with the initial assembly; proper maintenance of your DIY rock polisher is pivotal for longevity and efficiency. Neglecting the upkeep can turn your polished dreams into abrasive disappointments.
Keeping your polisher in tip-top shape ensures not just better performance but also safety, as a malfunctioning machine could lead to accidents or subpar results. A little elbow grease during routine maintenance can go a long way, saving money spent on repairs. It’s not just about polishing rocks; it’s about nurturing your hobby.
Routine Cleaning and Maintenance
Routine cleaning of your rock polisher might feel like a chore, but think of it like a stone that needs to be lovingly shaped over time. Regularly check for wear and tear after each tumbling session. This includes inspecting the motor, belts, and any seals. Some specific steps you could follow:
- Empty the barrel: Once the polishing session is done, make sure to empty all media and rocks immediately. This prevents small particles from grinding away at the surfaces and causing unnecessary damage.
- Wipe down components: Grit and grime can accumulate, impacting the operation. Use a damp cloth to wipe down the outside, and use a brush to clean any buildup in crevices.
- Check the belts: Over time, belts can fray or wear out. Make sure to check them for signs of wear. A loose or frayed belt can greatly decrease efficiency.
- Lubricate moving parts: This is key. Use a light machine oil on gears and other moving components to minimize friction, ensuring smoother operation.
By following these steps, you can extend the life of your machine and its components. Remember, a clean and well-maintained rock polisher not only lasts longer, but it can also perform better, yielding shinier rocks.
Upgrading Components for Longevity
Eventually, like all things that undergo wear, your rock polisher might need upgrades. This doesn’t mean you have to give up the old friend you built from ground up. Instead, you can keep enhancing its performance. Here are a few aspects you could consider upgrading:
- Barrel Material: Over time, the barrel can wear down. Consider upgrading to a thicker, more durable material that can withstand prolonged use. Some recommend using polyethylene, as it is known for its durability and resistance to impact.
- Motor Upgrade: If you find the motor is struggling with your tumbler load, a more powerful one may be needed. A stronger motor can handle larger batches of rocks, improving polishing efficiency. Just make sure to check compatibility.
- Seal Improvements: Upgrading seals can also be a smart move. Look for seals designed to endure more pressure and frequent use. Well-sealed barrels minimize leaking and enhance the effectiveness of your polishing media.
- Gasket Enhancements: Gaskts can rot or wear over time, so upgrading to high-quality materials will prevent the stalling or leaking of the compound. This is crucial in maintaining consistent polishing results.
By taking steps to upgrade components, you are making a conscious effort towards the longevity of your polisher. It’s all about optimizing and refining your setup, which will pay off in perfectly polished rocks.
"Maintenance is like polishing a stone; it could be tedious, but the shine at the end makes it all worthwhile."
Exploring the Community of Rock Polishers
Engaging with the community of rock polishers can be a game changer in your rock polishing journey. Rock tumbling is not just a solitary activity; it thrives on shared experiences, insights, and techniques. By tapping into this community, whether online or in person, you gain access to a treasure trove of resources and support. The diverse range of skills and knowledge within these groups can fill pivotal gaps in your own expertise, making the process more enjoyable and productive. Those who participate can exchange tips and complicity in troubleshooting while also celebrating the beauty of polished rocks together—after all, there's something incredibly rewarding about showcasing your polished stones and getting feedback from like-minded individuals.
Connecting with Other Enthusiasts
Finding fellow rock polishing enthusiasts doesn't have to be a daunting task. There’s a multitude of platforms available where you can meet others who share your passion. Social media platforms such as Facebook have dedicated groups for rock tumblers, where members regularly share their work and techniques. Additionally, sites like Reddit have communities that focus on not just rock polishing but also geology, providing a broader context for your endeavors.
Being part of these online groups can open doors to local meetups. Attending rock shows or club events can also rekindle your enthusiasm and broaden your understanding of the craft. You will find people who are just as eager to share their knowledge as they are to learn from you. These connections can lead to valuable friendships and collaborations, enriching your rock polishing experience.
Sharing Knowledge and Techniques
Nothing complements the art of rock polishing more than the sharing of knowledge and techniques. Within the community, many enthusiasts are eager to exchange ideas on polishing methods and materials, which can help elevate your skills to a whole new level.
For instance, some may have mastered the nuances of using specific grits or polishing compounds that yield better finishes. Others might have clever strategies for reducing noise or improving the efficiency of their tumblers. By discussing their processes, you can identify what might work best for your own projects.
"Every piece of advice, every shared mistake, is a lesson in disguise. Do not hesitate to ask questions—there’s no such thing as stupid queries in this realm."
Utilizing platforms for knowledge sharing may help foster this atmosphere, where questions and experiments are encouraged. Workshops and webinars are other options to consider, where you can learn from seasoned veterans face-to-face, or from the comfort of your home. By participating in such sessions, you can not only improve your technique but also contribute your insights, thus enriching the community overall.
Maintaining a flow of reciprocal learning ensures that everyone, regardless of their skill level, continues to develop and thrive in their rock polishing journeys.
Case Studies of Successful Rock Polishers
Exploring the journey of rock polishers who have successfully crafted their machines and perfected the art of rock tumbling can offer invaluable insights. Case studies encapsulate the practical application of theories and techniques, bridging the gap between theoretical knowledge and hands-on experience. This section provides a glimpse into their unique projects and methodologies, which will serve as a source of inspiration for both novice and seasoned collectors alike.
Showcase of Notable Projects
In the realm of rock polishing, several projects stand out for their ingenuity and results. One such project involved a rock tumbler made from an old washing machine drum. This inventive user repurposed the drum to create a rotating tumbler that effectively smoothed and shined various rock types. The key to this project’s success lay in understanding the balance between the tumbler's rotation speed and the type of grit used, ultimately achieving a stunning finish on quartz and agate.
Another notable example features a DIY rock polisher constructed from PVC pipes and rubber lining. This project is particularly impressive due to its simplicity and low cost. Enthusiasts utilized inexpensive materials, allowing anyone interested in rock polishing to replicate the design easily. The builder carefully selected the right size of the pipes to maintain optimal space for rocks and tumbling media. The result was a highly effective tumbler capable of yielding glossy stones in a fraction of the time compared to conventional tumblers.
Project outcomes like these illustrate practical and creative approaches to rock polishing, showcasing the potential of DIY solutions.
Analyzing Their Techniques
By scrutinizing these successful case studies, several key techniques emerge that can enhance your rock polishing endeavors:
- Material Selection: The case studies highlight the choice of materials, which often balances cost and durability. Using items like old appliances or PVC pipes encourages eco-friendly practices while producing effective results.
- Understanding Grit Usage: Different polishing stages depend on selecting appropriate grit sizes. The users in these case studies emphasize a gradual increase in grit size to ensure smoother finishes and reduce the likelihood of scratches. Observing their grit selection can guide you in establishing a step-by-step process tailored to the specific rocks being polished.
- Maintaining Consistency: Achieving a consistent tumble is vital for even polishing. Many of these projects incorporate features that aid in balance and stability, underscoring the importance of crafting reliable machinery.
- Experimentation: Perhaps the most striking lesson from these case studies is the spirit of experimentation. Rock polishers are encouraged to document their processes, tweaking variables like time, rotation speed, and media type until they achieve their desired results.
In collecting and analyzing these methods, you'd gain more than just inspiration; you'd find a framework for your projects.
"Innovation often sprouts from the gardens of creativity and practicality. Coalesce the two, and you might just tumble upon brilliance."
These case studies not only demonstrate diverse possibilities within DIY rock polishing but also encourage an interactive approach to learning—each project holds lessons beneficial for anyone venturing into this multifaceted hobby.
Closure: The Art and Science of Rock Polishing
As we draw the curtain on our exploration of rock polishing, it is clear that this charming hobby marries craftsmanship with science in a way that's both intriguing and fulfilling. The journey of crafting your own rock polisher not only equips you with the skills of construction and maintenance but deepens your understanding of geological sciences and the metamorphosis of raw stones into polished gems.
Reflecting on the Journey of Rock Polishing
Embarking on the adventure of rock polishing is akin to peeling layers off an onion—each layer revealing more layers beneath. You start with the rough exterior of natural stones, often disregarded, yet bursting with potential. When you sift through the steps of selecting materials, designing your machine, or adjusting grit sizes, you are essentially partaking in an ancient tradition that marries art and experimentation.
The benefits are profound. A well-polished rock not only serves as a stunning display piece but represents hours of patience and dedication. Your understanding of the various types of rocks and their properties emerges, turning a simple pastime into a channel for knowledge and creativity.
Considering the elements of rock polishing, one might argue that it stands as a metaphor for personal growth. Just as a rough stone is transformed into a shimmering masterpiece, each troubleshooting step you encounter bolsters your confidence and skill set. There’s no eureka moment quite like gazing at the final product of your toil and realizing that you crafted it all with your hands.
To wrap it all up, rock polishing isn’t merely a task; it’s a nuanced blend of art and science that deserves reflection. From the initial design considerations to exploring more advanced techniques, each phase is enriching. Whether you continue polishing as a hobby or branch into more advanced methods, rest assured this journey will mold you, much like the stones you so lovingly refine.