Casting Jewelry at Home: Your Complete Guide
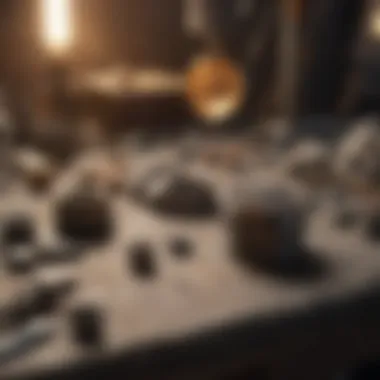
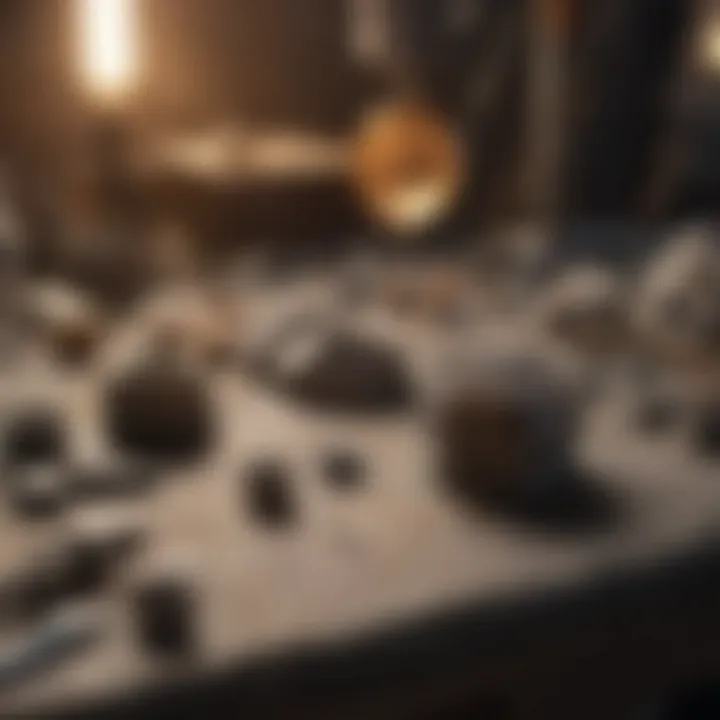
Intro
Casting jewelry at home is not just a hobby; it's a creative outlet that turns imagination into tangible art. Whether you're a complete beginner or someone with a bit of experience, understanding the nuances of this craft is essential. With the right tools, a sprinkle of patience, and a dash of creativity, you can transform metals into beautiful, personalized pieces. This guide aims to arm you with rich insights about materials, techniques, and critical safety measures to help you navigate this intricate world of jewelry making.
The journey of casting jewelry opens up different pathways, from investment casting to sand casting, each requiring unique materials and skills. Throughout this article, we will explore these methods, highlighting their advantages and disadvantages, helping you choose the best one that aligns with your vision and skill level.
This guide isn't merely about the practicality of casting but also about bringing artistry and precision to the forefront of your creations. By integrating artistic elements into your casting process, you enhance not only the aesthetic appeal of your jewelry but also your sense of achievement.
"Every piece of jewelry tells a story, a chapter of creativity and craftsmanship in metal."
When you dive into casting at home, remember that safety is paramount. Ensuring a well-ventilated workspace and wearing proper protective gear can be the difference between an enjoyable crafting experience and a hazardous one. As we delve deeper into this guide, keep in mind that each step is vital to achieving your desired outcome, and every detail matters.
Let's start by tracing back to the historical roots of jewelry casting, as understanding its origins can inspire your creative process.
Prolusion to Casting Jewelry
Creating jewelry at home is more than just a hobby; itâs a dance between craft and creativity. This intricate art allows not only for personal expression but also for the practical joy of designing something unique with your own two hands. As avid collectors of rocks and fossils might understand, the process of jewelry casting can be likened to unearthing a hidden gemâboth involve patience, precision, and an appreciation for the transformative nature of raw materials.
In this guide, readers will embark on a journey that centers on casting jewelry, emphasizing its transformative power. Understanding casting techniques and mastering the right tools enables enthusiasts to personalize their pieces significantly. Whether you want to create a delicate pendant or a striking statement ring, the importance of familiarizing oneself with each aspect cannot be overstated.
Casting jewelry at home opens the gate to a multitude of possibilities, inviting experimentation with shapes, designs, and materials. Novice folks may find that it fosters a deeper connection with their craft compared to simply purchasing pieces. Moreover, it could provide a sense of accomplishment that is hard to replicate. That satisfaction is not solely from the finished product; itâs what you learn about the process along the way.
"Crafting your own jewelry isn't just about aesthetics; it's about the journey that each piece embodies."
Understanding Jewelry Casting
At its core, jewelry casting is the technique of creating pieces by pouring molten metal into a mold, where it solidifies into a specific shape. This method has deep roots in history, but it thrives in modern contexts as well. Essential to this understanding is the flexibility casting offersâwhether one chooses to use lost wax casting, sand casting, or even vacuum casting, each method presents unique characteristics and advantages.
The allure lies in control over design and material selection. For instance, when choosing lost wax casting, a jeweler first carves their piece out of wax, creates a mold around it, and then melts the wax away to leave a cavity for molten metal. It's a dance of precision where the artist can see their vision come to life.
Additionally, it's crucial to recognize the enchanting aspects of materials themselves. Various metals, from gold to silver or copper, each tell a story about their origins, their properties, and how they respond during the melting and pouring process.
The Appeal of Home Casting
Home casting brings a myriad of advantages, especially for those who find joy in the crafting process. For one, it fosters an environment of creativity and innovation. When done at home, artisans can experiment without the constraints of commercial expectations, indulging in whimsical ideas that may never make it to the shelves of a store.
Moreover, there is an undeniable sense of pride that accompanies crafting something yourself. You not only savor the end product but also experience the twists and turns of the creative journey. There are mistakes, sure, but each misstep is a lesson learned, further honing your skills.
Home casting also presents a unique opportunity for customization. You can incorporate elements that resonate personallyâlike embedding tiny fragments from your rock collection into a fashion statement piece or using colors that reflect the shades of the natural world around you.
In a nutshell, the appeal of casting jewelry at home transcends purely decorative motives. Itâs an invitation to explore, create, and share a piece of your world with others, all while connecting with the ancient practice of jewelry making that continues to evolve today.
Essential Materials for Jewelry Casting
In the world of jewelry casting, using the right materials is critical. Each element has its part to play, whether it's the metal you select or the tools used to shape your creation. Understanding the ins and outs of these materials can be the difference between a piece that captivates and one that falls flat. As such, this section provides a comprehensive look into the essentials needed for effective jewelry casting at home.
Choosing the Right Metal
When it comes to jewelry casting, choosing the right metal is paramount. Metals arenât just about color or shine; they reflect personal style, durability, and even emotional connection. For instance, the choice of metal can set the tone for the entire piece.
Gold Types
Gold, particularly, is a classic choice. Its luster and resistance to tarnish make it desirable for many jewelry makers. However, when we talk about gold types, we must consider karat valuesâ24k being pure gold, while 10k has less gold content. This aspect matters because it defines the piece's value and durability.
One unique feature of gold is its ability to be alloyed with other metals. This not only modifies its color but also enhances its strength. For example, yellow gold combines with copper and silver, offering a warm hue, whereas white gold incorporates palladium or nickel for a more modern look. The downside? Higher karat gold can be softer and more susceptible to scratching. Yet, for pieces meant for special occasions, it remains a favorite.
Silver Alloys
Silver alloys present a different story. While sterling silver, composed of 92.5% silver and other metals like copper, is commonplace, the performance of these alloys can vary dramatically. They offer a bright, shiny finish and are often more affordable than gold, making them a popular choice for beginners and seasoned crafters alike.
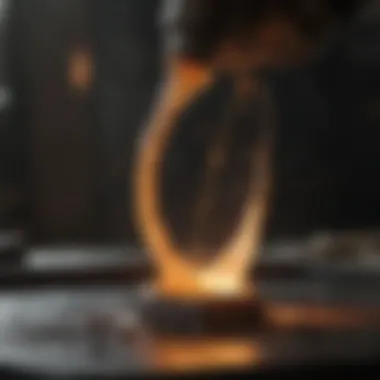
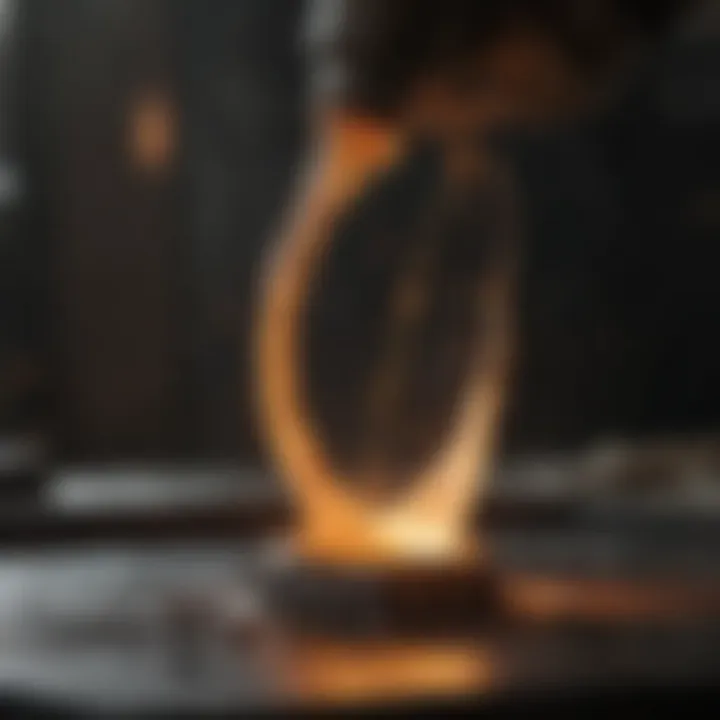
The unique aspect of silver alloys is their workability; they can be easily manipulated to create intricate designs. However, silver tends to tarnish over time, which might require extra maintenance. Still, for those who appreciate a bright shine and a vintage appeal, silver alloys strike a perfect balance between cost and aesthetic value.
Copper and Other Metals
Copper and other metals, such as brass or bronze, complete the casting spectrum. Copper is adored for its warm tones and affordability. It's malleable, enabling crafters to explore various techniques with minimal investment. The big draw with copper is its unique patina; over time, it can develop a rich green or brown hue, adding character to the pieces.
However, there are trade-offs. Copper may not have the same longevity or luster as gold and silver, and it can cause allergic reactions for some. Yet its versatility cannot be ignored, making it a wise choice for anyone looking to experiment with different styles.
Investing in Quality Tools
Quality tools make life a lot easier in the casting process. Itâs not just about picking up gadgets; the right equipment leads to better results.
Molds and Frames
The molds you choose dictate the shape of your jewelry piece. High-quality molds will ensure the integrity and detail of your creation. Silicone molds are popular because they can handle high temperatures and are reusable.
A key characteristic of molds is their ability to impart fine details, allowing even novice casters to produce professional-looking pieces. However, one drawback is that high-quality molds can be costly. Still, the investment pays off in time and effort saved during the casting process.
Melting and Pouring Equipment
Equipping yourself with reliable melting and pouring gear is essential. Melting pots, crucibles, and pouring ladles are quite literally the tools of your trade. The equipment chosen needs to withstand significant heat and allow for a smooth pouring process. A good quality melting furnace can significantly reduce the time it takes to melt metals, making your workflow more efficient.
However, the downside is that quality equipment often comes at a price. The initial investment could be steep, but it greatly enhances precision and reduces mishaps, which can be a relief when youâre deeply focused on creation.
Necessary Casting Compounds
Casting compounds play a supporting role in the whole casting operation.
Investment Powders
Investment powders are vital in creating molds that can withstand the temperatures during casting. They ensure that the mold provides an accurate impression of your model. Most jewelers use a phosphate-bonded investment due to its strength and ability to withstand high temperatures.
These powders often feature a fine particle size that enables them to capture intricate details, which is a distinct advantage in jewelry casting. However, improper mixing or incorrect ratios can lead to failures in mold strength; thus, following manufacturer guidelines is crucial.
Releasing Agents
Lastly, let's discuss releasing agents. These compounds reduce friction between the mold and the metal, facilitating easier removal after cooling. A good releasing agent enables you to get your piece out without damageâa definite plus for any caster.
Different types of releasing agents can change how well they work depending on what metal youâre casting. Itâs important to choose the right agent for the job, as a poorly chosen one can lead to a situation where the mold sticks, forcing you to scrap your work. Additionally, safety considerations should not be overlooked when working with such agents. They often require proper ventilation and protective measures to avoid potential hazards.
Casting Techniques Explained
Understanding various casting techniques is fundamental to crafting jewelry at home. Each method offers distinct characteristics and advantages, catering to different designs and materials. Knowing how to navigate these techniques can empower aspiring jewelers to create pieces that are not just beautiful but also intricately detailed. Moreover, familiarity with these methods helps in troubleshooting challenges that may arise during the casting process.
Lost Wax Casting
Lost wax casting, also known as investment casting, is a time-honored technique that has been used for centuries. In essence, it involves creating a wax model of the object you wish to cast, which is then encased in a ceramic or plaster material. Once the mold hardens, itâs heated, causing the wax to melt awayâhence the term "lost wax".
Key Considerations
- Precision in Modeling: The success of this technique lies in the detail and accuracy of the wax model. A more meticulously crafted model results in a more precise final piece. Using high-quality carving tools can enhance this process.
- Investment Material: The type of ceramic shell used can greatly influence the quality of the cast. Investing in durable, high-temperature materials will yield better results.
- Heat Control: Achieving the right melting and pouring temperature for your metal is critical. Going too hot or not hot enough can lead to defects in the finished product.
Sand Casting
Sand casting is a method that uses a sand mold to form the shape of the jewelry. This technique is particularly appealing for beginners due to its simplicity and accessibility. The typical process involves packing moist sand around a pattern of the desired jewelry piece, creating a mold that can be reused multiple times.
Benefits
- Affordability: Sand casting is one of the most economical methods of casting jewelry because you can create molds without much expensive equipment.
- Flexibility: It allows for more extensive experimentation with different designs. You can carve directly into the sand to make intricate patterns.
- Ease of Use: Even those with minimal experience can grasp the basic concepts relatively quickly. The materials required tend to be easily sourced and manageable for home projects.

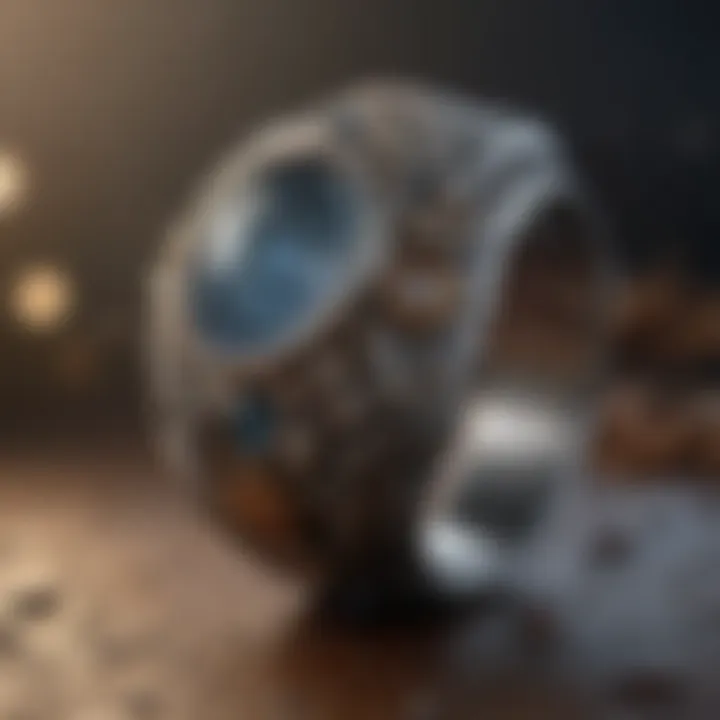
Vacuum Casting
Vacuum casting is a more advanced technique that relies on creating a vacuum to draw molten metal into a mold. This process reduces air bubbles and defects, producing a cleaner, more polished piece of jewelry.
Important Elements
- Mold Creation: This method often requires precise molds that can withstand the pressure of the vacuum. A well-made mold can significantly enhance the quality of the final product.
- Equipment Investment: To effectively execute vacuum casting, you may need to invest in certain equipment, such as a vacuum chamber. While this requires an upfront cost, the quality of the output can justify the expense in the long run.
- Metal Types: Different metals may react differently under vacuum conditions. It's crucial to understand how your chosen metal behaves during both the melting and pouring phases.
"Choosing the right casting technique can make or break your project; select wisely based on your goals and resources."
Setting Up a Casting Workspace
Setting up a casting workspace is a crucial aspect of jewelry casting at home. A well-organized and thoughtfully designed workspace creates an atmosphere that fosters creativity and precision. Having everything in its right place not only increases productivity but also minimizes the risk of accidents, which is vital when working with metals and tools that can be hazardous. This section discusses important factors in creating an effective casting workspace, emphasizing safety, organization, and layout.
Safety Considerations
Ventilation
When discussing the importance of ventilation, it is vital to highlight its role in maintaining a safe and comfortable environment. Proper ventilation helps to disperse harmful fumes and ensure that your workspace remains fresh. It's particularly essential when melting metals because certain metals can release toxic gases if heated improperly.
A key characteristic of ventilation systems is their ability to circulate air, which can prevent the buildup of noxious fumes. The best option often involves utilizing a fume hood or an exhaust fan installed near your workstation. However, an open window can also serve as a simpler yet effective solution. Always remember that fresh air is your best friend in jewelry casting.
Unique features of good ventilation include adjustable speed settings and filtration systems to catch harmful particles before they escape into your workspace. The main advantage of a well-ventilated area is the reduction of health risks associated with prolonged exposure to fumes. Fumes can cause dizziness or other severe respiratory issues if proper precautions arenât taken.
Protective Gear
Protective gear plays a significant role in ensuring your safety while casting jewelry. Wearing the right clothing, gloves, and eyewear can prevent injuries from accidental spills or sharp objects. A popular choice among enthusiasts is investing in a good pair of high-heat-resistant gloves. These not only protect your hands from burns but also offer a sturdy grip while handling hot materials.
The standout feature of protective gear is that it acts as a physical barrier between you and potential hazards. This gear often includes safety goggles, face shields, and heat-resistant aprons, ensuring comprehensive coverage. The advantage is clear: safeguarding against injuries allows you to focus on crafting your masterpieces without the constant worry of accidents.
Organizing Your Tools and Materials
Organizing tools and materials is vital for a smooth workflow. When casting, having everything within arm's reach can make the process efficient. Use divided containers to keep your metals, casting compounds, and tools sorted. Clearly label storage boxes to save time looking for specific items. Ensure that heavier items are stored lower to avoid accidents, while lighter items can be placed higher. This will also help you maintain a clean and tidy workstation, reducing distractions while working.
One effective method to organize your tools is to categorize them based on their function. For instance:
- Melting tools: torches, melting crucibles
- Casting tools: molds, vacuum systems
- Finishing tools: saws, files, polishers
Creating a Functional Layout
The layout of your workspace can significantly impact your casting experience. A functional design allows you to move seamlessly from one task to another, minimizing the time spent switching between tools and materials. Think about the workflow youâll be using and arrange your work area accordingly.
Having a dedicated space for each phase of casting, from model fabrication to finishing, will help to create a logical flow. Consider adopting a U-shaped layout, where you can face inward toward your tools, making it easier to access everything as needed while fostering a cozy, focused environment.
Also, lighting should not be understated in this setup. Invest in bright, adjustable lighting, preferably LED, to illuminate your workspace correctly. Good lighting helps to avoid mistakes and allows for meticulous detailing, which is especially important when casting intricate designs.
Steps in the Casting Process
Understanding the casting process is crucial for anyone interested in creating jewelry at home. This section lays out the step-by-step approach that turns an idea into a tangible piece of art. The casting process involves several key phases that help ensure the highest quality results. Each step must be diligently executed, as the smallest oversight can lead to significant flaws in the final piece. Essential aspects include preparing the model, creating the mold, melting and pouring the metal, and finally cooling and finishing. Each of these steps will be explored further, highlighting their unique roles and importance in achieving that perfect finished piece.
Preparing the Model
Preparing the model is the foundation of the casting process. This step determines the final look and feel of the jewelry. Without careful consideration at this stage, the subsequent steps may not yield the desired outcome.
Design Considerations
Design considerations are vital when creating a model for casting. It's not just about aesthetics; it also influences functionality and manufacturability. Effective design means understanding what materials youâre working with and how they will behave during the casting process. One crucial characteristic of thoughtful design is ensuring the piece is functional and wearable. Good design can be the difference between a beautiful pendant and one that you can't wear comfortably.
If you focus too heavily on elaborate designs, you might run into challenges like complexity in mold-making or structural issues in the final product. Keeping designs manageable without sacrificing creativity is an essential balance in this stage.
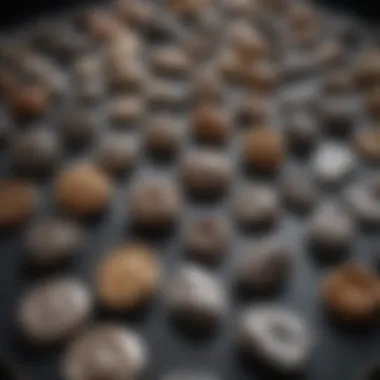
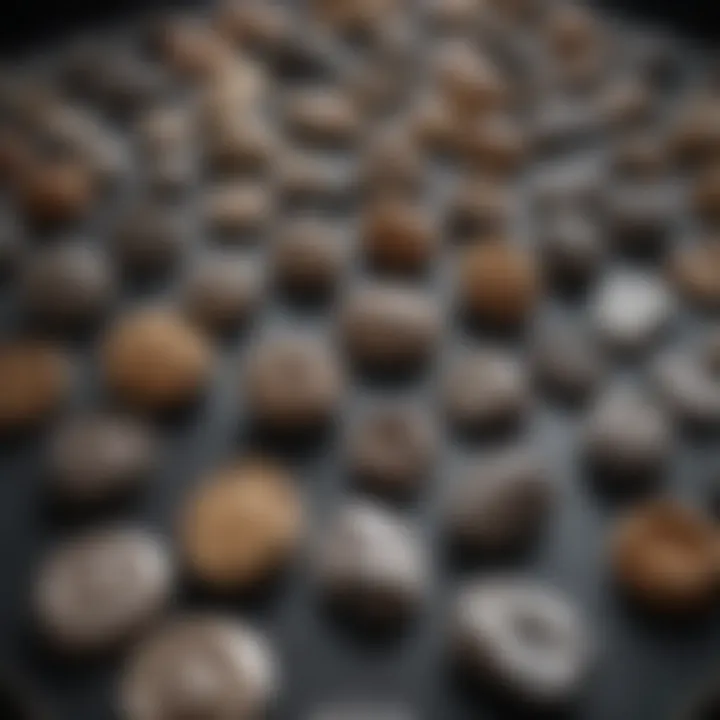
Scaling Techniques
Scaling techniques refer to the methods applied to maintain proportionality while adjusting the size of the model. This step is significant, especially if one is creating multiple pieces or adjusting a prototype. The ability to accurately scale your design helps achieve uniformity and can reduce material waste, which is a plus in any home workshop.
A main characteristic that sets effective scaling techniques apart is precision. They utilize drafting software or basic hand-drawn sketches, to help visualize the final piece. An important point to remember is that scaling down too much may lead to unnecessary fragility in the model, while scaling too large might complicate your casting endeavors. Hitting the sweet spot is crucial for success.
Creating the Mold
Once the model is prepared, it's time to create the mold. This step is integral in ensuring that the molten metal takes on the exact shape of your design. The chosen method for molding, whether itâs sand, silicone, or investment, needs to complement the design.
Melting and Pouring
Melting and pouring are two interconnected tasks that require careful attention and timing. The melting point of the metal must be adequately reached, which involves using appropriate tools and techniques. The pouring process needs to be swift but careful, ensuring that there are no air bubbles or defects introduced into the mold.
Cooling and Finishing
Trimming
Trimming is a critical finishing step that involves cutting away excess material post-casting. This step is significant because it helps refine the shape and details of the piece, setting the stage for what's next. Effective trimming enhances the overall appearance and can bring out intricate design features that were hidden beneath unwanted excess.
One key characteristic of trimming is the precision needed. A well-trimmed piece looks more polished and professional, which is crucial for self-respect in the craft. In a home setting, careful handling of tools ensures safety as well as a clean result.
Polishing Techniques
Polishing techniques are the final touch that can elevate a piece from good to exceptional. Proper polishing brings out the shine and luster that draws attention. The right polishing method depends on the metal used and the finish desired. Techniques such as buffing, tumbling, or using chemical polish can be explored, each offering different levels of finish.
One unique feature of these polishing methods is their flexibility; each technique can produce varying results depending on the approach used. Itâs worth noting that poor polishing can lead to scratching and a dull finish, overshadowing even the best elements of the design. Thus, investing time in this stage is essential for achieving a stunning final product.
Challenges in Home Jewelry Casting
Casting jewelry at home can feel like a daunting task. While it opens up a world of creativity, it also comes with its fair share of challenges. Understanding and preparing for these hurdles is essential for anyone who wishes to explore this craft. Not only will it reduce frustration, but it will also ensure that the pieces you create are of high quality, reflective of your skill and vision.
Common Mistakes
When diving into jewelry casting, especially as a novice, youâre likely to encounter a series of pitfalls. Here are some of the most prevalent mistakes:
- Skipping Research: Jumping headfirst into casting without understanding the materials and processes can lead to disappointing results. It's vital to read up on various techniques and materials used.
- Ignoring Safety Precautions: Forgetting about safety measures can have severe consequences. Always remember to wear protective goggles and gloves, and work in a well-ventilated space.
- Poorly Made Molds: A mold that isn't made correctly will yield poorly shaped pieces. Attention to detail during this stage is crucial; itâs often said that a bad mold leads to a bad cast.
- Inconsistency in Temperature: Metal needs to be melted to specific temperatures. Failing to maintain the right temperature can result in incomplete melting or defects in the final product.
- Neglecting Finishing Touches: Rushing the finishing process can ruin the aesthetic appeal. Take the time to trim and polish your pieces properly; this makes a big difference.
Understanding these common mistakes can help you sidestep them and focus on fine-tuning your craft.
Dealing with Defects
Defects in jewelry casting can stem from several sources, but the good news is that many of them can be repaired or mitigated with practice and knowledge. Here are some tips on handling these issues:
- Air Bubbles: If your piece has air bubbles, they can often be fixed by carefully re-melting and pouring again. To prevent this, ensure that your metal is properly heated and agitated before pouring.
- Uneven Surfaces: These can usually be smoothed out through sanding or polishing. Itâs essential to pay attention during the cooling stage, as the way the piece cools can affect its surface quality.
- Cracks or Fractures: These defects can often be a sign of temperature fluctuations during pouring. For minor cracks, consider using a strong adhesive or solder for repairs. If the piece is significantly damaged, it may be best to start over.
- Color Inconsistencies: Variations in metal quality can lead to uneven coloring. Make sure to source your metals from reputable suppliers to avoid this. When melting, keep an eye on the mix to ensure consistent results.
âEvery piece tells a story, even if it has a few flaws.â
By addressing these potential defects proactively, you can preserve the integrity of your work and continue honing your skills. Remember, every mistake you encounter is a stepping stone on your journey to mastering the art of home casting.
Final Thoughts on Home Casting
Casting jewelry at home is not merely a hobby; itâs an art form that allows creators to express themselves while honing their technical skills. By diving into the nitty-gritty of the casting process, both novices and experienced jewelers can develop a deeper appreciation for the nuances involved. The allure of crafting something from scratch can be incredibly rewarding, fostering a sense of personal achievement that is often absent in store-bought alternatives.
Bridging Tradition and Modern Techniques
Imbedding oneself in jewelry casting means interacting with a rich history of craftsmanship while also embracing modern advancements. The age-old methods of lost wax casting, for instance, showcase a technique that has withstood the test of time. However, todayâs technology, like 3D printing, offers exciting possibilities to elevate traditional methods. Imagine a world where age-old techniques are enhanced by digital designs tailored to one's creative vision, this blend of old and new not only increases precision but also opens doors to unique possibilities in jewelry design.
Craftsmanship will always carry roots in tradition, yet advancement will define the future; itâs a delicate balance that every aspiring jeweler must navigate.
The Future of Home Jewelry Crafting
Looking ahead, the future of home jewelry crafting seems brighter than the sparkle on a freshly polished ring. With the rise of online communities, forums, and educational resources, sharing knowledge and techniques has become more accessible than ever. Websites like Reddit and specialized Facebook groups provide platforms for feedback and inspiration, fostering a robust culture of shared learning.
As technology continues to innovate, one can expect materials to evolve as well. New eco-friendly metal options and improved molding materials ensure that craftsmanship remains sustainable and relevant. As more people become aware of the environmental impact of their art, shifting towards responsible practices will be crucial.