Mastering the Art of Cast Molds for Collectibles
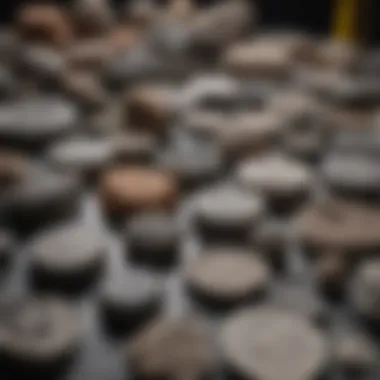
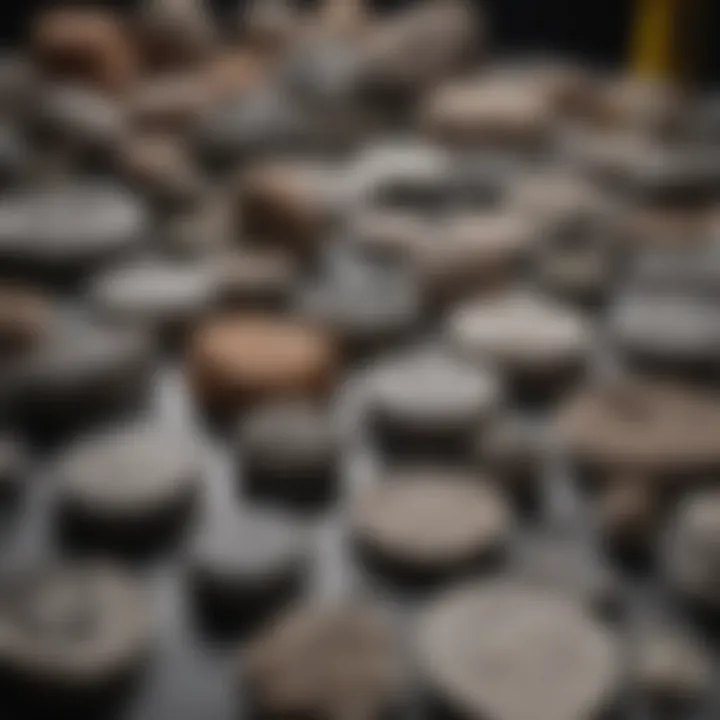
Intro
Embarking on the journey of creating cast molds for collectibles is not just a pastime; it’s an art that opens up a world of creativity and personal expression for enthusiasts of rocks and fossils. Collectors, whether they're just starting out or are seasoned veterans, often find joy in replicating the natural wonders that captivate them. In this guide, we'll unravel the intricacies of crafting cast molds, ensuring that you’re equipped with the essential knowledge to begin or enhance this rewarding process.
History and Origins
The fascination with collectibles can be traced back to the dawn of civilization. Humans have always had an insatiable curiosity for the natural world, leading them to collect items that held beauty or significance. Rocks and fossils, in particular, have captured the attention of many, with their diverse forms and historical context.
Overview of Collectibles, Rocks, and Fossils
Rocks and fossils serve as tangible links to the past, allowing us to peek into the Earth’s timeline. Collectors have emerged as vital custodians, preserving these pieces of history. Along the way, the process of molding has evolved to help capture the beauty and details of these specimens.
"To collect is to be curious about the world, to embrace its wonders, and to carry parts of it with you."
Historical Significance and Cultural Impact
Throughout history, various cultures have revered rocks and fossils. In ancient China, jade was not merely an ornamental stone; it was believed to possess spiritual significance. In Western cultures, the fascination with dinosaurs in the late 19th century spurred a surge in fossil collection, fundamentally changing how we view extinct life forms. Today’s collectors continue to uphold these traditions, often influenced by cultural and educational contexts.
Identification and Classification
Before diving into the mold-making process, one must first earn a solid grasp on their collectible’s identity. Understanding the characteristics of different rocks and fossils not only enriches your knowledge but also helps ensure the utmost care when creating molds.
Guide to Identifying Rocks and Fossils
Understanding how to identify various specimens is crucial for any collector. Each rock or fossil bears unique traits that can provide insights into its age and origin. Here’s a simplified guide to help you:
- Texture: Observe the surface; is it smooth, rough, or grainy?
- Color: Various colors reveal different mineral compositions.
- Fossil Marks: Look for any distinct patterns or imprints that signal its origin.
Common Types and Variations
When categorizing rocks and fossils, numerous types dominate the landscape:
- Igneous Rocks: Formed from solidified lava, such as basalt or granite.
- Sedimentary Rocks: Created from particle deposition, examples include limestone and sandstone.
- Metamorphic Rocks: Rocks altered by heat and pressure; marble and slate are prime examples.
- Common Fossils: Ammonites, trilobites, and dinosaur bones encompass a range of historical significance.
In closing this section, it’s clear that both collecting and creating molds from rocks and fossils is steeped in rich history and culture. It is a blend of scientific inquiry, artistic expression, and a personal journey towards understanding the Earth and its ancient past. As we move forward in this guide, we’ll unfold the methodologies and technicalities of crafting cast molds, each step designed to ensure success and satisfaction in your creative endeavors.
Prelude to Cast Molds
Creating cast molds is an art form that holds significant value for collectors, particularly those who focus on fossils and minerals. The ability to replicate unique items not only enhances one's collection but also opens the door to endless possibilities in crafting and creativity. Understanding how to create cast molds is crucial as it can lead to a deeper appreciation of the collectible itself and the intricate processes involved in preserving its likeness.
Definition and Purpose
At its core, a cast mold is a hollow form used to create copies of an original object. This involves pouring a material, such as resin or plaster, into the mold, which hardens and takes on the shape of the item being replicated. The purpose of casting molds goes beyond mere reproduction; it's about preserving the essence of an object, capturing every detail, every nuance, and every flaw that makes the original unique.
For example, a collector of rare fossils may choose to create a mold of a unique specimen. Not only can they have replicas for educational purposes or to share with fellow enthusiasts, but they can also ensure that the original remains undisturbed and protected from handling wear.
Casting also provides a way for collectors to create custom displays or even functional items inspired by their collections. You might transform a fossilized shell into a decorative paperweight, or replicate a stunning mineral for use in jewelry-making. The possibilities are virtually endless, making the ability to create molds a vital skill for any dedicated collector.
Applications in Collectible Crafting
The applications of cast molds in crafting collectibles are vast.
- Display and Preservation: Creating molds allows collectors to showcase their items in a way that not only protects the original but also enhances the aesthetic appeal of their displays. A well-crafted replica can make a striking addition to any collection.
- Educational Use: Replicas can be utilized for educational purposes, allowing for hands-on learning experiences without the fear of damaging irreplaceable items. This is particularly useful in museum settings or classrooms, where original artifacts might be too delicate.
- Customization: Collectors can personalize their items. With molds, one can add personal touches or create unique variations of a piece, catering to individual tastes and preferences.
- Market Opportunities: There are also potential market benefits. Collectors can create replicas to sell or trade. Some might find that their custom molds turn into small businesses, allowing their passion for collecting to become a source of income.
In summary, mastering the art of creating cast molds not only enriches the collectible experience but also opens avenues for creativity, education, and potential economic gain. As we delve deeper into the specifics of this process, it becomes clear that understanding molds is indispensable for anyone serious about enhancing their collection.
Choosing the Right Materials
Choosing the right materials is pivotal in the mold-making process, especially when it comes to collectibles like fossils and minerals. The materials you select not only impact the final product’s quality but also determine the ease of working with them. By understanding the properties of mold-making materials and casting materials, you can make educated choices that enhance your overall crafting experience and ensure the longevity of your molds.
Types of Mold Making Material
Silicone Rubber
Silicone rubber is often seen as the star player in the mold-making scene. Its flexible, yet durable nature allows for detailed captures and effortless demolding. It stands out because it withstands various temperatures and doesn't break down easily. When you want to reproduce intricate features of a collectible, silicone rubber is a go-to option.
Another edge silicone has is its capacity to retain shape and minor details without compromise, which is a significant plus for collectors aiming for precision. While it can be on the pricier side, the investment tends to pay off due to its repeated usability and durability. The downside is that it can sometimes be a bit fussy during the curing process, requiring careful mixing and timing.
Latex
Latex comes in as another popular choice, often favored for its affordability and ease of use. It’s a bit more forgiving, making it ideal for beginners. The key characteristic of latex molds is their stretchiness, which aids in getting details out with less hassle. However, latex has a shorter shelf life compared to silicone and can degrade when exposed to certain elements over time. For collectors working on a budget, latex can help you whip up a mold without breaking the bank, but you should plan on replacing them more frequently than their silicone counterparts.
Plaster
Plaster holds its ground as a traditional mold-making material, especially in hobbies where weight is not an issue. Its main advantage is its cost-effectiveness and straightforward application. For items that don’t have intricate or delicate details, plaster molds can serve their purpose well. However, they do have their limitations. Plaster molds are rigid and can break if not handled gently. They also absorb moisture, which can introduce complications in the casting phase. Nonetheless, for large, simple forms, plaster is often a practical choice for those starting out.
Selecting Casting Material
The choice of casting material significantly influences the final look and feel of your collectible. Not only do you need to choose a material that suits your project, but you should also consider its compatibility with your mold material.
Resin
Resin is a popular casting choice among collectors. Its versatility and ability to replicate fine details make it a sought-after option. The characteristic clarity of resin allows for visually striking results, especially when combined with colors or other inclusions. However, the downside is that working with resin often requires precise measurement and mixing to avoid bubbles or inconsistencies. Plus, it may emit fumes that necessitate proper ventilation during the pouring process.
Metal
Casting with metal is an avenue less traveled but holds great potential for durability and longevity. Metals can yield sturdy replicas that withstand time, offering a tactile experience for collectors. The key characteristic here is the weight and solidity of the final piece; however, working with metal requires the right equipment and knowledge of handling temperatures, which could deter those just starting out in mold making. Metal molds also entail a higher cost and longer processing time, making them more suitable for serious enthusiasts.
Concrete
Concrete may not be the first material that comes to mind when thinking of collectibles, but it offers a unique texture and impressive durability. It works particularly well for larger projects or items that don't require fine detail. The affordability of concrete is a selling point for hobbyists looking to create large pieces without a hefty price tag. However, its weight and the excess time needed for curing can be cumbersome. If a collector wants a robust piece that stands the test of time, concrete can certainly fit the bill, albeit with its own peculiarities.
"Choosing the right material can make or break your molding project. Invest time in learning about your options to better your results."
In summary, understanding the various options for mold-making and casting materials is crucial for achieving quality outcomes in collectible crafting. This knowledge allows enthusiasts to elevate their projects, transform their ideas into tangible pieces, and ultimately enhance their collections.
Essential Tools for Mold Making
Creating cast molds requires not just skill but also the right tools. This section focuses on the essential tools that make mold making efficient and effective. Having the right instruments at your disposal can enhance your molding experience, ensuring that you achieve a high-quality cast without unnecessary hiccups along the way.
Basic Tools and Equipment
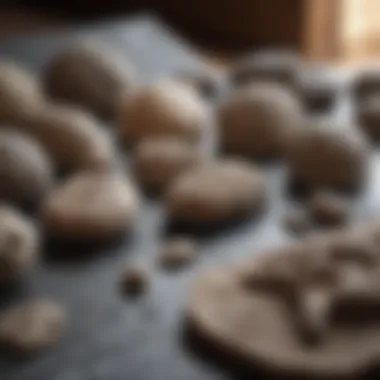
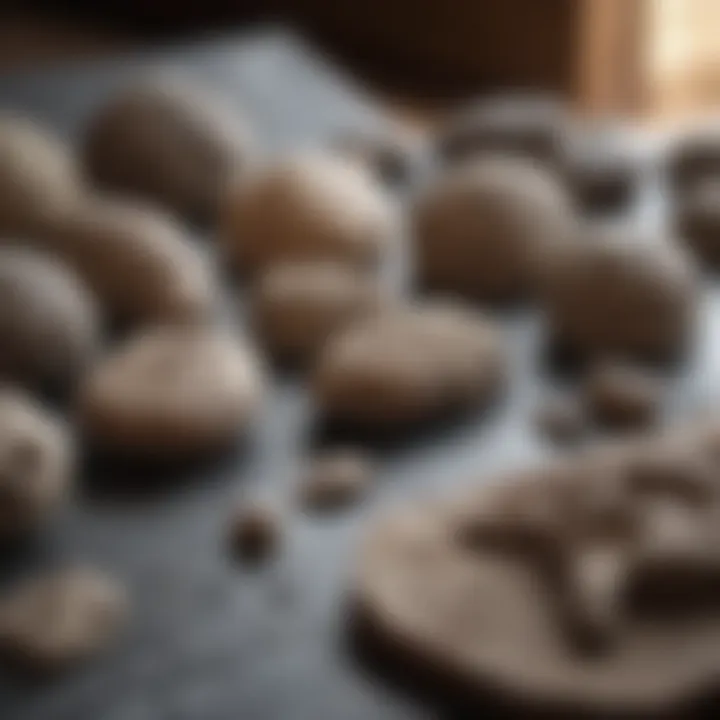
Mixing Cups
Mixing cups are pivotal in the mold-making process. They serve the essential function of holding your mold material while you prepare it for use. Usually made from plastic or silicone, these cups are designed to be flexible and durable, making it easy to pour out the contents once mixed. The key characteristic of mixing cups is their volume markings, which allow you to measure precise amounts of material, critical for achieving correct mixing ratios.
One unique feature to look for is spouts or pour lips on these cups, which facilitate an easier and cleaner pour, minimizing mess. However, it's prudent to note that using cups made from porous materials can lead to difficulties in clean-up later on.
Stirring Sticks
Stirring sticks are another fundamental tool in your mold-making toolkit. Their primary role is to thoroughly combine the various components of your molding material. Typically made from wood, plastic or even metal, these sticks come in several lengths and widths. Choosing a longer stick can be beneficial for reaching the bottom corners of larger mixing containers, promoting thorough mixing.
Notably, disposable wooden sticks are a popular choice due to their affordability and convenience. One downside, however, includes potential splinters breaking off, which could inadvertently contaminate your mixture.
Mold Box
The mold box is the container that houses your object during the molding process. It's crucial for holding the mold material in an appropriate shape while it cures. Mold boxes can be made from various materials like wood, plastic, or cardboard, depending on the project size and material used.
An essential feature of mold boxes is their ability to create a watertight seal, preventing any leakage of the mold material. Consequently, ensuring that your mold box fits snugly around your object is vital. A disadvantage could arise with homemade boxes, as they may not always hold up against pressure or temperature changes, leading to potential leaks.
Safety Equipment
Safety comes first when engaging in mold making; thus, protective gear is crucial to ensure a hassle-free experience. Below are the primary safety equipment items you should not overlook:
Gloves
Wearing gloves during the mold-making process is non-negotiable. They protect your hands from chemicals present in the mold materials, which can cause irritation or allergic reactions. Typically made from latex or nitrile, these gloves provide a reliable barrier without sacrificing finger dexterity.
A notable advantage is that they offer excellent grip while handling materials, though some individuals might find latex gloves prone to tearing if caught on sharp edges. In such cases, nitrile gloves could be a better alternative due to their more durable nature.
Masks
Masks are vital for protecting your respiratory system from fumes released by certain mold materials. Using a well-fitted mask, particularly one rated for filtering out fine particulates, can guard against inhaling harmful substances. They reduce the risk of respiratory irritation, which can often go unnoticed until symptoms escalate.
A significant characteristic of these masks is their ability to filter out even the smallest particles, making them beneficial in confined spaces. However, they may feel cumbersome for extended periods, which is something to keep in mind when spending lots of time on your project.
Goggles
Goggles are crucial for eye protection while preparing and pouring molding materials. They serve as a barrier against splashes, dust, and debris that could cause injury. The key feature you might want to consider is their anti-fog property, which can help you see your work clearly without constant adjustment.
Although goggles are generally comfortable, some types can feel bulky, leading to distractions while you're bonding with your creative side. Taking your time to find a pair that fits snugly yet comfortably can make all the difference.
Understanding and utilizing the right tools and safety equipment is imperative in the journey of mold making. Having adequate preparation can prevent mishaps and elevate the quality of your creations.
Preparing the Item for Molding
Before diving into the intricate dance of mold making, it is pivotal to understand that the success of any cast mold hinges on both the cleanliness and sealing of the item you wish to replicate. Preparing the item serves multiple purposes. It not only ensures a high-quality final product but also plays a critical role in preserving the integrity of the collectible.
When you clean and seal the item properly, it protects your mold against imperfections that might lead to disappointing results. A neglected or improperly prepared object can yield a mold that's riddled with flaws, ultimately affecting the collectible you are aiming to reproduce. With that in mind, let’s look into the specifics of why the preparation steps are essential.
Cleaning the Object
The first step in preparing your object is cleaning it thoroughly. Dirt, dust, and any residues can interfere with the mold-making process, leading to unsightly blemishes in the final product.
Start by selecting a gentle yet effective cleaning solution. A mix of warm water and mild soap is often enough to tackle the grime without harming the collectible. Use a soft cloth or a brush to carefully scrub the item, ensuring that all crevices and nooks are free from dirt. For delicate items, consider a cotton swab to reach intricate details. After cleaning, rinse the item with clean water to remove any soap residue. It's all about leaving the object spotless.
Cleanliness is next to moldliness. A clean object is paramount for a successful casting.
Once the object is clean, allow it to air dry completely. Any moisture remaining on the surface could lead to issues when you apply the mold material, as it might not adhere properly.
Sealing the Item
The next step, sealing the item, is just as crucial. This process involves applying a thin layer of sealant, which acts as a barrier between the object and the mold material. This step prevents the mold material from sticking to the collectible itself, potentially causing surface damage in the demolding process.
Several options exist for sealants, including commercially available release agents or even homemade mixtures, such as petroleum jelly or wax. The choice often depends on the material of the item you're working with and the variety of mold-making materials you have chosen. For instance, silicone rubber may require different sealing approaches than plaster molds.
Apply the sealant evenly, ensuring complete coverage. It’s a good practice to use a brush or a soft cloth for this task, paying particular attention to intricate details and areas where the mold material might get trapped. Allow the sealing agent to dry completely before proceeding to the next steps in the mold-making process.
By taking the time to clean and seal the object properly, you safeguard your mold creation and enhance the quality of your cast. These fundamentals lay a solid foundation and set the stage for a successful mold-making adventure.
Creating the Mold
Creating the mold is a vital step in the whole casting process, specifically when it comes to collectibles like fossils and minerals. It is not merely about pouring material into a container; it's about ensuring that every detail of the original object is captured. Getting this right can significantly impact the final appearance and quality of the casts produced. A well-constructed mold can help replicate intricate textures and features, which are fundamental in collectible crafting. This stage also requires attention to detail, as any oversight can lead to poor-quality replicas that don’t meet the expectations of discerning collectors.
Building the Mold Box
The mold box serves as the frame that holds the mold material in place. It's where the magic begins. Choosing the right size and shape is essential. You want it to fit snugly around the item you're molding without applying undue pressure on it. Typically, wood or sturdy plastic are common choices for building mold boxes. Here are a few steps to consider when constructing your mold box:
- Select Material: Choose wood or heavy-duty plastic that can withstand liquid mold materials. Plywood works well due to its sturdiness.
- Measure the Object: Carefully measure your collectible item, ensuring you leave at least a half-inch of space around it for the mold material.
- Cut and Assemble: Cut your sides to the desired height and secure them together with screws or nails. Make sure it’s leak-proof; you don’t want any mold material oozing out.
- Place a Release Agent: Before positioning your object, apply a release agent to prevent sticking.
This step is foundational as it determines the ease with which the mold material can be poured and the final quality of the mold.
Mixing and Pouring the Mold Material
Once the mold box is sorted, it’s time to dive into mixing the mold material. Different materials behave differently, so understanding how they work is key. For example, silicone rubber is favored for its flexibility and detail capture.
- Read the Instructions: Each material comes with specific mixing ratios. Don’t eyeball it; precision counts.
- Combine Ingredients: In a clean mixing cup, combine the resin and hardener—if applicable—using a stir stick. Mix slowly to minimize bubbles that can mar the mold.
- Pour Methodically: When pouring, do so from a height of about 4 to 6 inches above the mold box. This helps reduce bubbles created during the pouring process. Start in one corner and allow the liquid to flow over the object, ensuring the mold material fully envelops it.
Keeping an eye on the viscosity of your material is imperative. A mixture that’s too thick will result in air pockets, while one that’s too runny may fail to encapsulate fine detail.
Demolding the Item
After the mold material has settled and cured per manufacturer instructions, it's time for the exhilarating part: demolding. The first action is to gently pry the mold away from the sides of the mold box. You might need to lightly tap it or use a putty knife to help with this.
- Carefully Remove the Original: You want to ensure that you do this gently so as not to damage either the mold or the original collectible. Start at one end and work your way around.
- Inspect the Mold: Once out, check if the mold captured all the details you wanted. Flaws at this stage can often be fixed in subsequent pours.
- Clean Up: After demolding, clean your mold of any remaining residue. This will help maintain the quality for future castings.
Demolding is often a moment laden with anticipation because, often, it’s the first sight of your work in progress. The thrill of revealing the captured likeness of the collectible can be both rewarding and educational, providing insights into nuances you may carry into future projects.
Remember, creating molds isn't a one-size-fits-all process. Learn from each step and adjust for next time.
Types of Molds
Understanding the various types of molds is paramount for anyone looking to create cast replicas for collectibles. Each type of mold brings its own set of advantages and considerations that can significantly impact not just the quality of the finished product but also the efficiency of the molding process itself. Collectors and crafters often find themselves selecting a mold type based on the intricacies of the original item they wish to reproduce, budget constraints, and desired outcome. Let's delve into the three main types: single-part molds, two-part molds, and multi-part molds.
Single-Part Molds
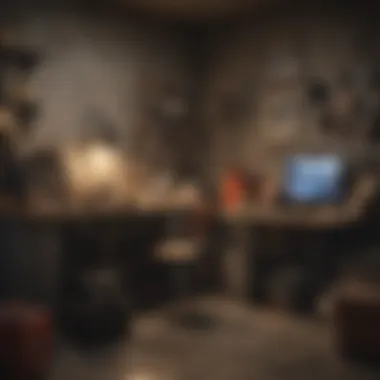
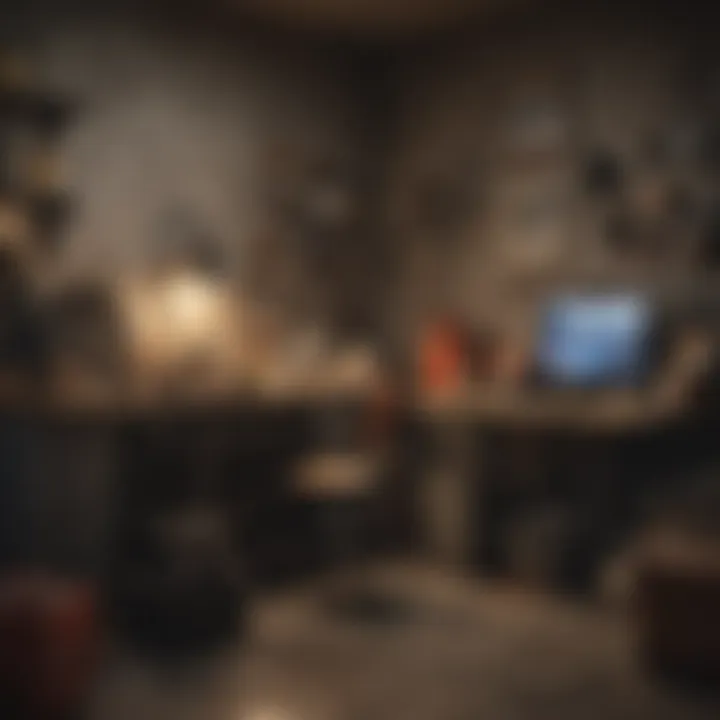
Single-part molds are in a league of their own when it comes to simplicity and efficiency. Ideal for objects that aren't too intricate, these molds allow for fast replication with minimal fuss. The design consists of a single mold cavity that captures the entire form of the original item.
- Benefits:
- Quick & Easy: Single-part molds are generally quicker to prepare and use, making them accessible for beginners or those looking for rapid results.
- Cost-Effective: With fewer materials needed, the overall investment is lower, which is ideal for hobbyists or casual collectors.
- Less Complexity: You’re less likely to encounter issues such as misalignment or excess seam from joining multiple parts.
However, there's a caveat. If the original object has undercuts or complex geometries, this mold type may not work well, leading to potential damage during removal. Therefore, it's often prudent to assess the characteristics of the item you wish to mold carefully.
Two-Part Molds
For those wanting to capture more intricate designs while maintaining a straightforward approach, two-part molds might just be the golden ticket. This type of mold consists of two halves that come together to form a complete mold cavity, ideal for items with undercuts or details that a single-part mold can't handle.
- Benefits:
- Increased Detail: The two-part design allows for a more faithful reproduction of fine details such as texture and intricate shapes, making it a go-to choice for detailed collectibles like minerals or fossils.
- Flexibility: Changeable dimensions in mold making; you can adjust the height and angle of the mold halves for various shapes.
On the flip side, you have to manage the alignment of the two parts carefully during assembly. Any misalignment can lead to a poor cast, which can be frustrating and costly. It's essential to use proper techniques and tools during the pouring and curing stages to ensure both halves fit together snugly.
Multi-Part Molds
Multi-part molds take innovation to the next level, enabling complex shapes and detailed pieces to be cast with impressive accuracy. These molds can have three or more parts and are commonly used in more advanced crafting scenarios, often favored by professional artisans.
- Benefits:
- Unmatched Complexity: Ideal for very detailed pieces, multi-part molds allow artisans to reproduce highly complex designs that would be impossible with a simple approach.
- Creative Flexibility: The ability to create multiple parts can enhance creativity, allowing for unique designs and forms.
Nevertheless, working with multi-part molds demands higher skills and more time. You might find that the setup takes longer, and achieving a properly aligned mold can involve quite a bit of fiddling around. As such, they may not be the best fit for novices or those looking to make quick, uncomplicated casts.
As you contemplate the kind of mold to utilize for your collectibles, think about the object’s intricacies, the time you’re willing to invest, and the final outcome you desire. It’s not just about replication; it’s about creating a lasting piece that mirrors the original’s beauty.
Choosing the right type of mold can significantly enhance your crafting journey, ensuring that each cast you make is a reflection of skill and passion. With careful consideration of your selected method, you can pave the way for successful and precise replicated creations.
Casting the Mold
Casting the mold is a pivotal step in the process of creating collectibles, particularly in the realm of fossils and minerals. It is at this stage where all the preliminary work—selecting materials, preparing the item, and creating the mold—comes together. This section will outline not just the mechanics of casting itself but also its significance in enhancing the quality and durability of the finished collectible.
One of the primary benefits of proper casting is the accuracy it ensures. Any errors during casting can lead to distortions in the final piece, diminishing its value significantly. Thus, understanding the nuances of this step can elevate a collector's craftsmanship.
Moreover, the choice of casting material and technique can either enhance or compromise the aesthetic appeal of the finished piece. Factors to consider include the texture, weight, and color of the mold. A well-cast item should not only replicate the original object's features but also have a fitting finish that appeals to potential buyers or collectors.
"The essence of a well-crafted collectible lies in the details—an artisan’s touch, if you will."
In the next subsections, we’ll delve into the specifics of preparing the casting material, which is vital for achieving consistent results, followed by techniques for pouring that ensure perfection.
Preparing the Casting Material
To achieve a successful casting, preparing the casting material is essential. This stage involves selecting the right type of casting medium that suits the specific requirements of your mold and desired collectible. Depending on what look and feel you’re aiming for, options like resin, metal, or concrete could come into play.
Here are some key considerations:
- Resin is popular among collectors for its clarity and adaptability. It captures intricate details and can be tinted to match the original item's colors, making it a favored choice.
- Metal casting can create very robust collectibles with a weighty feel. It conveys a sense of timelessness but involves a steeper learning curve and more complex preparation.
- Concrete is suitable for items with a more rustic or earthy aesthetic. Its affordability and ease of use lend it to beginners or those on a budget.
Once the material is selected, it must be measured and mixed according to the manufacturer's instructions. Precise measurements are crucial—too much hardener may lead to brittleness, while too little can make the final piece too soft.
Pouring Technique
Pouring technique plays a major role in the quality of the final product. This part isn't just about getting the material into the mold; it's about doing it in a way that prevents air bubbles and ensures uniform distribution.
Here are some tips for effective pouring:
- Pour Slowly: When you pour your casting material, do it slowly and steadily. A rushed pour can lead to trapped air, which creates imperfections on the surface of the collectible.
- Use Multiple Pours: If you’re working on large or complex molds, consider multiple pours. Start with a small portion to fill the deep areas and allow it to set before continuing.
- Tilt the Mold: If your mold design allows, tilting it slightly at the start of the pour can help the material cover all corners and reduce the chance of air getting trapped.
The key to successful casting is taking your time and being observant. Each pour is a step toward achieving a collectible that stands the test of time and showcases the beauty of the original piece.
By carefully preparing and pouring your casting material, you'll be well on your way to creating impressive collectibles that not only capture the spirit of the original item but stand tall on their own.
Finishing the Cast
Once the casting material has been poured and cured, moving on to the finishing phase is vital. This stage is where your work truly comes to life, transforming a raw cast into a stunning replica that meets your collectible standards. Finishing the cast is not just about aesthetics; it’s about skillfully refining your creation and addressing any imperfections that may arise during the casting process. The attention you give during this stage can greatly affect the final product's overall quality and, ultimately, its value to collectors.
Removing from the Mold
Removing the cast from its mold can be a delicate affair. Patience is key, as each mold material behave differently. Generally, for silicone molds, gently flexing the mold throughout its edges is a good start. The more rigid molds, like plaster, may require a bit more coaxing. Here’s a step-by-step approach:
- Assess the Mold Material
Check if the type of mold has any specific requirements for removal. For instance, silicone is usually easier to peel away compared to harder molds. - Loosen the Cast
Carefully run a thin object, like a palette knife or a flat spatula, around the edges to loosen the cast from the mold. Avoid using excessive force, as it may damage your cast. - Handle with Care
Once you feel the cast loosening, gently pull it away from the mold. Some molds may even require you to push from underneath, so be mindful of the specific contours of your design. - Inspect the Result
After taking out the cast, check for any visible defects or areas that might need attention. It is not uncommon to find small imperfections, which is completely normal and part of the crafting journey.
Trimming and Smoothing Edges
Once you pop out your cast successfully, it’s time to tidy up. The edges may not be as crisp and clean as you’d like, especially if you are working with a more complex mold. Trimming and smoothing out these edges is vital, not only for looks but for the overall touch and feel of the collectible. Here’s how to approach this task:
- Choose the Right Tools
A sharp utility knife is an excellent tool for trimming raw edges. You could also consider using fine-grit sandpaper or a rotary tool with a sanding attachment for added finesse. - Work on a Stable Surface
Ensure you are working on a flat, stable surface that allows you to maneuver easily without accidents. - Trim Excess Material
Take your utility knife and carefully trim away any excess material along the edges. It is best to trim small amounts at a time to avoid taking off too much. - Sand for Smoothness
After trimming, use fine-grit sandpaper to smooth out any rough spots. Moving in circular motions works best to avoid creating flat patches. If you're using a rotary tool, be gentle—instead of applying too much pressure, let the tool do the work. - Final Inspection
After smoothing, take a good look at your piece. A polished edge gives a professional finish that collectors will surely appreciate.
"The difference between ordinary and extraordinary is that little extra."
Crafting collectibles is not just about reproducing a form; it’s about creating a piece worth cherishing. Paying attention to the finishing touches can elevate your work substantially, making it a prized possession for any collection.
Care and Maintenance of Molds
Taking proper care of your molds is crucial for preserving their usability and extending their lifespan. Just like any tool or craft item, neglecting maintenance can lead to inefficiencies and failure to produce quality casts. For collectors, especially those invested in creating custom pieces, understanding the nuances of mold care is as essential as mastering the casting process itself.
Proper Storage Techniques
Storing your molds correctly is the first pillar of effective mold care. Improper storage can lead to deformities, deterioration, or even complete failure, which no collector wants to face. Here are some guidelines to follow:
- Cool, Dry Place: It’s best to keep molds in a cool and dry location. Heat can warp silicone and rubber molds, while moisture can lead to mold and mildew. A desiccant in the storage area can help control humidity.
- Wrapped or Placed in Boxes: If possible, wrap your molds in a soft cloth or keep them in sturdy boxes. This extra layer of protection can prevent unwanted scratches or damage.
- Avoid Heavy Objects: Never place heavy items on top of your molds. This can cause pressure that might deform your molds over time.
- Keep Away from Sunlight: Prolonged exposure to sunlight can adversely affect the material properties of molds, leading to brittleness and fading. Store them away from direct light sources.
By following these simple guidelines, you can significantly enhance the longevity of your molds and keep them performing at their best for numerous projects to come.
Cleaning Guidelines
Cleaning your molds after each use is another critical aspect of maintenance that cannot be overlooked. Simple cleaning procedures can prevent buildup of casting materials and ensure that each casting holds its shape and detail. Here’s how to go about it:
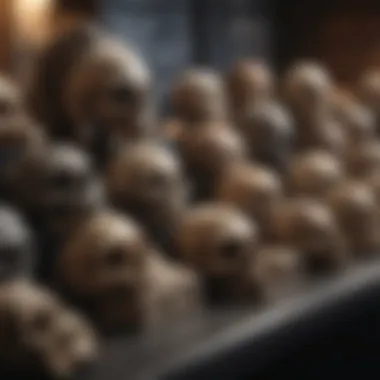
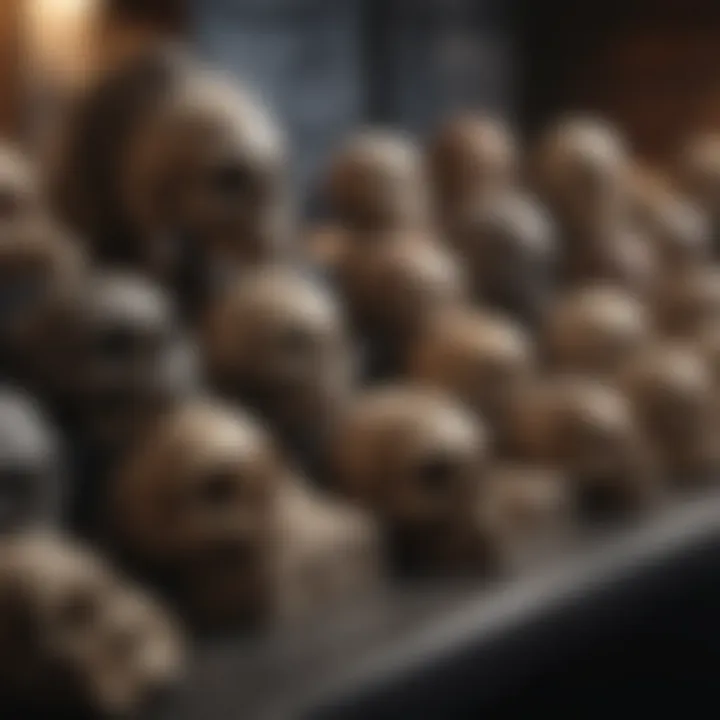
- Immediate Cleaning: Clean your molds soon after use. The longer residues stay on, the harder they become to remove.
- Gentle Soap and Warm Water: Use a mild soap solution with warm water to clean the molds. Avoid abrasive cleaners or scrubbers as they can scratch the surface, compromising the mold’s ability to create detailed casts.
- Rinse Thoroughly: After cleaning, make sure to rinse out all the soap and residue. Leftover soap can affect your next casting.
- Dry Completely: Allow the molds to air dry thoroughly before storage. Trapped moisture can lead to mold growth, which is not ideal for mold longevity.
- Inspect for Damage: After cleaning, inspect your molds for any signs of wear or damage, such as cracks or softness, which could negatively impact future casts.
Remember: A clean mold makes for a happy collector and a successful cast. Maintaining cleanliness in your tools is as important as the craftsmanship you apply to your creations.
By adhering to these care and maintenance protocols, collectors can ensure their molds remain as good as new, ready to bring their creative visions to life, time and time again.
Common Mistakes to Avoid
When it comes to creating cast molds, especially for collectibles like fossils and minerals, even the tiniest missteps can lead to considerable setbacks. Understanding common mistakes not only saves time and resources but also enhances the quality of the final product. The journey of mold making can be intricate, and by steering clear of these pitfalls, you ensure a smoother path toward achieving impressive results.
Inadequate Sealing
One of the most frequent errors seen in mold making is inadequate sealing. A proper seal is essential when creating molds, particularly when dealing with intricate items or detailed designs. If the item isn’t adequately sealed, the mold material can seep into the nooks and crannies of the collectible, leading to a compromised mold and potential ruin of the original object.
Moreover, using the wrong type of sealant or not applying it evenly can lead to air pockets. These pockets are not just a cosmetic issue; they can cause weaknesses in the mold leading to breaks or defects during the casting process. To avoid this, it’s important to thoroughly clean the collectible and apply a sealant specifically designed for mold making.
- Ensure Complete Coverage: When applying sealant, make sure to cover every section of your item. Double-check areas that might be hard to see or reach.
- Use Quality Sealants: Always use a sealant that is compatible with your mold material. Low-quality sealants might fail early and lead to more headaches down the line.
"A well-sealed item is the cornerstone of a successful mold. Cut corners here, and you might end up with a costly error."
Incorrect Proportions in Mixing
Another major error mold makers stumble upon is incorrect proportions when mixing materials. The success of your mold and the final cast relies heavily on the right mixture of components, especially when dealing with resin or silicone. Too much hardener can cause brittleness, while too little might result in a mold that never sets properly.
Getting your proportions right might sound straightforward, but it’s often a tricky balance. One small miscalculation can lead to a mold that doesn’t cure, resulting in wasted time and resources. Here’s what you might want to consider:
- Follow Manufacturer Instructions: Each material will come with its own set of instruction, so pay close attention to the recommended ratios.
- Use Accurate Measuring Tools: Trying to eyeball measurements never works well for precision projects. Invest in a scale or dedicated measuring cups for accuracy.
- Conduct Small Test Batches: If unsure about the mix, conduct a small test. This can reveal any issues before you commit to the full mold-making process.
By being cautious and detail-oriented, not only do you sidestep major pitfalls, but you also enhance the overall quality of your collectibles.
Ensuring that you avoid these common mistakes can significantly increase the success of your molding endeavors. Pay attention to sealing and mixing, and you’ll find your path to collecting becomes even more rewarding.
Innovative Techniques in Mold Making
Innovations in mold making have revolutionized the crafting of collectibles over the years. Embracing cutting-edge technologies not only makes the process more efficient but also enhances the quality of the final products. Understanding these innovative techniques is essential for collectors as they can yield molds that are more precise, durable, and easier to produce. Let's dive into two significant advancements in this field that every enthusiast should be aware of: 3D printing and the use of advanced materials.
3D Printing for Molds
3D printing is a game-changer for creating molds, especially in the realm of collectibles. This method allows for intricate designs that would be near impossible to make by hand. With software, collectors can design personalized molds tailored to their unique items, like rare fossils or minerals that need precise replication.
The advantages are plentiful. First and foremost, accuracy is significantly improved. Errors from manual crafting can lead to imperfect molds, which in turn can affect the quality of the cast. 3D printing negates that risk by ensuring high precision in dimensions, capturing every detail.
Furthermore, speed plays a crucial role. Traditional methods may take hours, whereas a 3D printed mold can be ready in minutes after the design is finalized. This swift production time lets collectors quickly make adjustments to their designs as needed. However, considerations must be taken into account regarding the initial costs of 3D printers and materials. Getting started may be an investment, but the long-term benefits can outweigh these costs.
"The future of mold making is here, and it runs on technology!"
Using Advanced Materials
When it comes to material selection, there’s much more than just silicone and plaster these days. Advanced materials are making waves in the world of mold crafting, enabling more robust and versatile solutions. These materials can include thermoplastics, urethane rubbers, and even unique composites that offer enhanced characteristics.
For instance, thermoplastics are known for their structural integrity and can withstand higher temperatures compared to traditional materials. They are especially useful when casting metals or other materials that require more heat-resistant molds. Similarly, urethane rubbers exhibit remarkable flexibility and durability which allow for multiple castings without wear and tear. This is particularly beneficial for collectors who intend to make several copies of the same collectible.
Another point worth mentioning is environmental impact. Many advanced materials aim for sustainability, using non-toxic properties and increasing life-span. For collectors concerned about ecological implications, this factor plays a significant role in their choices.
In summary, innovative techniques in mold making not only cater to the craftsmanship of custom collectibles but also address the nuances of safety, efficiency, and environmental considerations. Collectors looking to enhance their practice should consider incorporating these advancements for better outcomes.
Applications Beyond Collectibles
In the world of mold making, the uses extend far beyond the realm of personal collections. This section delves into how molds can be harnessed in various creative and functional realms, highlighting their versatility and significance in both artistic expression and practical applications.
Artistic Creations
Creating molds is not solely about preserving and replicating collectible items; it also opens doors for artistic chance-taking. For artists, molds serve a canvas of limitless possibilities. They can be used to reproduce intricate designs, allowing for consistent and detailed copies of a single piece. Think about sculptors or painters who want to add dimension to their work; using molds can breathe life into their ideas.
For example, a sculptor wanting to replicate a unique design can create a mold from a prototype. By doing so, they can produce multiple casts, each one ready for personalization with paints or finishes, allowing for creative variations. Moreover, performance artists may use molds to create props or sets that enhance their storytelling, offering audiences something visually captivating. Collectors of art or unique sculptures also stand to gain from mold making as it can help them appreciate the breadth of creative interpretations possible with each mold design.
Highlights of Artistic Applications:
- Reproducing intricate designs consistently
- Allowing for creative variations in finished pieces
- Enabling performance art enhancements with crafted props
- Expanding an artist's portfolio through diversified pieces
By utilizing mold making techniques, artists not only enhance their own capabilities but also invite broader interpretations of their works, enriching the artistic community as a whole.
Functional Objects
Apart from artistry, molds offer practical applications in daily life, particularly when it comes to functional objects. These are not just limited to decorative items; think of cookware, tools, and even components for machines that might require custom shapes or sizes. The beauty of creating these molds lies in the ability to tailor designs to exact specifications, effectively reducing waste and improving efficiency.
For instance, a home engineer might require a specific component that isn't readily available on the market. By creating a mold, they're able to cast replicas of functional parts, like gears or brackets, that fit perfectly, maintaining the integrity of their project. This kind of custom approach can also minimize costs—no more paying for expensive replacements when a simple mold can do the trick.
Key Practical Benefits:
- Customizable design to fit exact needs
- Cost savings on supplies and replacements
- Increased efficiency by reducing waste
- The potential for innovation in product design and development
"Creating a mold is about capturing possibilities, not just objects."
By looking at the larger picture, mold making becomes an essential skill not just for collectors, but for anyone seeking to innovate in both creative and practical fields.
Finale and Future Prospects
Crafting cast molds for collectibles, particularly in the niche of fossils and minerals, evokes both an art form and a science. Bringing together diverse materials and techniques, custom mold creation opens a breadth of possibilities for collectors. This section delves into the importance of continuing to evolve your techniques and fostering community within the mold-making landscape.
The journey doesn’t end once you’ve mastered the basics of mold making. Instead, it’s just the tip of the iceberg. as collectors delve deeper into effective mold-making methods, they will discover how the process can further enrich the significance of their collections. Engaging in this craft also allows for a personal touch, giving you control over the outcome, from the texture to the finish of your collectibles. By prioritizing experimentation and innovation, you can elevate your artifacts to new heights.
Next Steps in Mold Making
Taking your mold-making skills to the next level requires exploring various pathways:
- Experiment with Different Materials: Don’t shy away from trying out new mold-making materials, such as polyurethane or hybrid silicones. Each brings unique properties that could enhance your final cast.
- Advanced Techniques: Build on your foundational knowledge by diving into advanced techniques like pressure molding or vacuum forming. These methods can yield more detailed and precise casts—perfect for intricate fossil reproductions.
- Contribute to the Process: Share your knowledge and experience by creating tutorials or guides, providing insight into what works and what doesn’t. Being transparent about your learning process can aid others in their journey.
Each step involves a willingness to fail and learn. Embrace the hiccups along the way as opportunities to innovate and refine your skills.
Community Engagement and Knowledge Sharing
The spirit of mold making thrives within a community that actively embraces collaboration and knowledge sharing. Here are a few avenues to engage with fellow mold makers and collectors in the field:
- Participate in Online Forums: Engage with communities on platforms like Reddit, en.wikipedia.org, and facebook.com. These spaces allow for discussions about techniques, troubleshooting, and inspiration from other like-minded individuals.
- Attend Workshops and Events: Look out for mold-making workshops or collector events. These gatherings serve as ideal opportunities to exchange ideas, learn from experts, and connect with local artisans.
- Create Collaborative Projects: Consider partnering with others in your community. By pooling resources and knowledge, you can tackle larger or more complex projects, which might be a monumental task solo.
Engaging with others not only enhances your understanding but also keeps the passion for mold making alive. This collective energy allows everyone to thrive, share in successes, and mutually overcome challenges within the mold-making process.
When you stand on the shoulders of giants, the view is clearer. It’s about learning, teaching, and growing together in an enriching mold-making journey.